Alcoa 발전소의 신뢰성
오래된 톱은 나쁜 홍보 같은 것은 없다고 말합니다. 어떤 홍보든, 심지어 아첨하지 않는 종류라도 아예 없는 것보다 낫습니다.
인디애나주 뉴버그에 있는 Alcoa의 Warrick Power Plant 사람들은 이에 동의하지 않을 것입니다. 2001년에는 732메가와트의 석탄을 태우는 발전소가 글로벌 기업의 72페이지에 달하는 연례 보고서에서 여러 번 언급되었습니다.
공장 관리자인 Peter DeQuattro는 "우리의 신뢰성은 세 번이나 결함이 있는 것으로 나타났습니다. "여기 발전소의 신뢰성 문제는 Alcoa가 2001년 수익에 대해 세전 4,500만 달러의 비용을 지출했습니다. Alcoa 400개 지점 중 연간 보고서에서 세 번이나 그런 유형의 인정을 받는 것은 좋지 않습니다."
Warrick 참조는 회사의 이웃 알루미늄 제련 작업의 용량에 심각한 영향을 미친 대규모 발전소 고장에 대해 투자자에게 설명/사과를 제공했습니다. 고장은 2001년 12월 4일에 발생했습니다. 발전소와 제련소가 정상 기능으로 복귀하는 데 거의 4개월이 걸렸습니다.
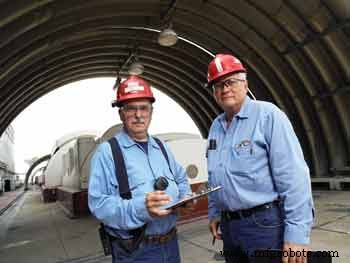
신뢰성이 향상되어 인디애나주 뉴버그에 있는 Alcoa의 발전소는 4억 4천만 달러의 자본 프로젝트 자금을 확보할 수 있었습니다.
발전 관리자인 DeWayne Todd는 "우리의 주요 목적은 저비용 전력을 제공하는 것입니다. "저비용 전력은 켜져 있고 사용 가능함을 의미합니다. 제련 작업을 중단할 수 없습니다. 우리의 신뢰성은 수익성과 비즈니스 지속 능력에 필수적입니다."
이 공생 관계에서 제련소가 끊어지면 발전소도 피를 흘립니다.
International Brotherhood of Electrical Workers Union Local 702의 건강 및 안전 대표이자 헤드샵 스튜어드인 운영 직원인 Brian Hall은 "공급하지 않으면 실직하게 됩니다."라고 말합니다.
그러나 12월 4일은 발전소의 과거 신뢰성 문제의 징후가 아닌 하나의 사건이었습니다.
2005년 1월에 사이트의 유지 관리 관리자로 고용된 Rick Fox는 "솔직히 그 당시 이곳은 다른 유틸리티와 마찬가지로 운영되었습니다."라고 말합니다. 계획하고 예측한 작업을 수행하지 않고 일이 진행됩니다. 당신은 소방관입니다."
기계 유지보수 팀 리더이자 IBEW 회원인 Steve Strahl은 당시의 고통스러운 기억을 가지고 있습니다.
"우리는 일하러 왔고 마치 그 장소가 불타고 있는 것 같았습니다."라고 그는 말합니다. "긴급 상황이 우리를 기다리고 있었습니다. 부서에서 부서진 물건 목록을 전달했습니다. 전화가 끊겼습니다."
45명의 유지보수 작업자가 7,000개의 플랜트 자산(이 중 80%가 1950년대와 60년대에 설치됨)을 책임지고 있어 과부하 상황이었습니다.
매일의 초과 근무와 주 6일에서 7일 근무가 일반적이었고, 심야 전화도 마찬가지였습니다. 휴가와 휴일은 짧게 - 때로는 갑자기 줄었습니다. 사냥 여행을 떠난 수석 기계 엔지니어 Rick Mayer를 찾기 위해 한 정비공이 켄터키로 파견되었습니다. 정비공은 Mayer를 나무 가판대에 놓고 캠프를 폐쇄하는 것을 도왔고 보일러 급수 펌프 문제를 해결하기 위해 공장으로 다시 데려갔습니다.
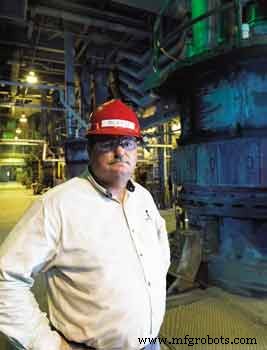
유지 관리 관리자인 Rick Fox는 자신의 부서가 성공할 수 있었던 것은 고위 경영진의 지원 덕분이라고 생각합니다. "(Alcoa Primary Metals 위치 관리자) Royce Haws와 (공장 관리자) Peter DeQuattro는 더 높은 신뢰성으로 유지 관리가 비용이 아니라 투자라는 것을 이해하고 있습니다."라고 그는 말합니다.
사진:Glenn Tang, Photics LLC
'DOING THINGS RIGHT'
그 시점에서 2005년 초반으로 이동합니다. 대화의 주제(모르나요?)는 홍보입니다.
Fox는 "유지보수 팀 앞에 앉아 이 식물을 잡지 표지에 올리는 것이 내 목표 중 하나라고 말했습니다. "표지 표지에 오른다는 것은 옳은 일을 하고 있다는 핑계를 대고 있다는 뜻입니다. 그룹으로서 올바른 일을 하면 잡지 표지에 실릴 것이라고 말했습니다."
이 기사를 읽으면 이 목표가 달성되었음을 알 수 있습니다. Warrick Power Plant는 Reliable Plant 2007년 11월/12월호의 표지를 장식했습니다. 스포트라이트 커버 스토리에서 롤 모델 식물 역할을 합니다.
이 사이트를 연간 보고서 나쁜 소년에서 전국 간행물 핫샷으로 전환한 이유는 무엇입니까? 사임한 사람에서 소방에 이르기까지 계획적이고 사전 예방적인 솔루션에 집중했습니까? 신뢰할 수 없는 공장에서 90%의 계획된 작업, 93%의 가용성, 90%의 일정 준수, 97%의 PM 준수 등을 자랑하는 안정적인 공장으로? 생존이 두려운 시설에서 모회사로부터 4억 4천만 달러의 자본 투자를 확보한 시설까지?
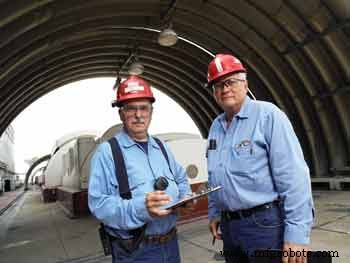
기계 유지보수 팀 리더인 Steve Strahl(왼쪽)과 예측 유지보수 기술자 Gary Seaton이 인디애나주 뉴버그에 있는 Alcoa 발전소에서 일련의 발전기를 검사하기 전에 작업 체크리스트를 검토하고 있습니다.
사진:Glenn Tang, Photics LLC
Alcoa 사이트는 유지 관리 및 안정성에 대한 관점을 변경했습니다.
DeQuattro는 "유지 관리는 유지 관리 담당자에 관한 것이 아닙니다. 문제를 수정하는 것이 아닙니다. 생산 능력과 생산 가용성을 유지하는 것입니다."라고 말합니다. "신뢰성은 수익성과 장기적 생존을 달성할 수 있는 기본 실행 전략입니다. 이것은 자산 관리의 기초입니다. 기본 가정은 장비가 제품의 양과 품질을 생산하는 데 사용할 수 있다는 것입니다. 생산하는 데 필요한 시간입니다. 유지 관리와 신뢰성은 모두의 일이며 모두의 책임입니다."
공장은 어려운 상황을 최대한 활용했습니다.
변화를 수용했습니다.
성장을 저해하는 사일로를 무너뜨리기 위해 열심히 노력했습니다.
변화는 빨랐고 그 결과는 장관이었습니다.
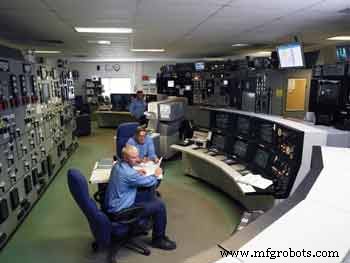
42년 Alcoa 직원인 운영자 Bob Braun은 최근 고용된 Adam Thorne과 함께 제어실을 모니터링합니다.
형제 자매 간의 경쟁
발전소 및 제련소가 전체 기업의 관점에서 비즈니스/생존에 접근하기 시작한 후 초기 진전이 이루어졌습니다.
"예전에는 발전소가 '필요한 악'이었습니다."라고 유지보수 부서 관리자인 Kim Woods는 말합니다.
"사일로 주위에는 울타리가 있고 울타리에는 면도칼 철사가 있는 2개의 사일로가 있었습니다."라고 Fox는 덧붙였습니다.
그러나 Alcoa Primary Metals 위치 관리자 Royce Haws는 이러한 위치 형제 간의 긴밀한 협력 관계가 효율성을 높이고 총 비용을 절감하며 궁극적으로 인디애나 남부에서 장기적으로 생존할 수 있다는 비전을 지지했습니다.
기계 엔지니어 빌 블러드워스(Bill Bloodworth)는 "중요한 것은 우리가 회사의 비용 곡선에서 어느 위치에 서 있는지였습니다."라고 말합니다. "우리는 그 곡선을 낮출 필요가 있습니다. 이 사이트는 전체적으로 값싼 금속을 생산해야 합니다. 값싼 금속을 생산하는 유일한 방법은 그들에게 값싼 전력을 공급하는 것입니다. 금속 생산과 관련된 다른 비용의 대부분은 다소 고정되어 있습니다. 유일한 작업할 수 있는 실제 델타는 전력 비용입니다. 이것이 우리를 핵심으로 만든 것입니다."
DeQuattro는 "지금 우리는 공통의 비전 아래 작업하고 있습니다. "우리는 글로벌 원자재 사업에서 경쟁하고 있습니다. 따라서 팀의 일원으로서 우리 모두는 우리의 몫을 하기를 원합니다."
신뢰성은 전력 생산 및 분배를 위한 전사적 총 비용을 줄이기 위한 노력의 은총알이 되었습니다.
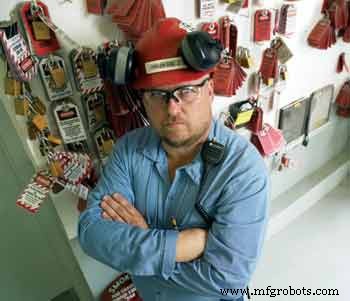
IBEW Local 702의 본사 직원인 Brian Hall에게 안전은 심각한 문제입니다.
그것은 의미가 있었다. 장비가 더 안정적이면 가동 중지 시간이 줄어들고 계획에 없던 가동 중단이 줄어들고 긴급 상황이 줄어듭니다. 높은 신뢰성은 일반적으로 발전소의 유지 보수 비용과 총 비용 절감을 의미합니다. 그리고 저비용 전력과 신뢰성을 제공할 수 있다면(오프라인 상황이 아님) 제련소는 비용이 일반적으로 2~3배 더 높은 외부 시장에서 전력을 조달할 필요가 없습니다.
Fox는 "Royce Haws와 Peter DeQuattro는 안정성이 향상되면 유지 관리가 비용이 아니라 투자라는 것을 이해합니다."라고 말합니다.
사전 조치
유일한 질문은 이러한 유형의 신뢰성을 제공하는 방법이었습니다.
제련소에서 영감을 얻었습니다. 2003년 초, 유지보수 리더는 LCE(Life Cycle Engineering) 및 Ron Moore Group의 컨설턴트와 팀을 이루어 Reliability Excellence Process라는 접근 방식을 만들었습니다. 아주 좋은 결과를 보고 있었습니다.
발전소는 배포의 측면을 관찰하고 운영에 Reliability Excellence(또는 Rx)를 도입하기로 결정했습니다. LCE는 2004년 11월에 방문하여 2005년 1월에 공식 평가를 수행했습니다. 초기 평가 점수는 나쁘지 않았습니다. - .528로 사이트를 "신흥" 범주(LCE는 .400에서 .549 사이로 정의)로 분류했습니다. "반응형"(.000 ~ .399)을 넘어 "선제형"(.550 ~ .749) 범주의 문앞에 있습니다. (최고 수준인 "우수"에 대한 점수는 .750에서 1.000 사이입니다). 그러나 .528 번호는 실제 이야기를 말하지 않았습니다.
"우리는 반응적인 조직이었습니다."라고 Fox는 말합니다. "우리는 작은 일들이 깔끔하게 진행되고 있었지만 아무 것도 연결되어 있지 않았습니다. 바퀴는 있었지만 스포크가 많지 않았습니다. 결론은 우리가 사업을 하는 방식에 대한 철학을 바꿔야 한다는 것이었습니다. 우리는 사후 대응 모드에서 사전 예방 모드로 전환합니다."
2005년 봄, Rx 리드 팀은 향후 3년 동안 달성해야 할 일과 이정표를 제시하는 초기 마스터 플랜을 개발하기 시작했습니다. 작업 제어 프로세스, 창고 공급 및 예측 유지보수를 감독하기 위해 3개의 하위 팀이 생성되었습니다. "그들은 마스터 플랜의 일부를 가져와서 작업을 시작했습니다."라고 Fox는 말합니다.
"바지 자리로 날아가는" 환경을 현미경으로 관찰하고 해부했습니다. 표준화된 프로세스 형태의 구조가 주입되었습니다. 계획과 일정의 씨앗이 뿌리를 내리고 자랄 수 있는 토양입니다.
팀은 또한 모든 현장 자산에 대한 위험 기반 중요도 분석을 수행하여 필요한 수준의 관심과 일상적인 작업 우선 순위를 결정했습니다. 가장 비즈니스 관련 위험을 유발할 가능성이나 능력이 있는 장비가 목록의 맨 위에 놓였습니다. 본질적으로 덜 위험한 장비(이중화, 자주 사용하지 않는 사용, 비용 또는 기타 요인으로 인해)는 목록에서 떨어졌습니다.
Fox는 "우리(내부적으로 또는 운영팀과의 논의에서)는 첫 번째, 두 번째, 세 번째 등의 작업에 대해 더 이상 논쟁할 필요가 없습니다. "중요도 목록은 작업의 계층 구조를 결정합니다."
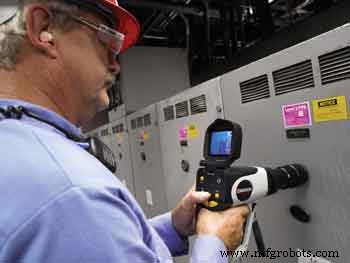
유지보수 기술자인 Tom Anderson은 SpyGlass 어안 렌즈가 장착된 Mikron 카메라를 사용하여 전기 캐비닛의 적외선 판독값을 가져옵니다.
두뇌 및 구매
2005년 늦여름까지 사이트는 롤아웃 및 교육을 위한 준비가 되었습니다. Fox와 Todd는 모든 공장 작업자에게 프레젠테이션과 워크숍을 제공했습니다. 이 세션에서는 Rx 프로세스와 기본 작업, 마스터 플랜을 구현하는 방법, 혁신을 위한 모든 사람의 역할, 궁극적으로 성공을 측정하는 방법에 대해 설명했습니다. 문화 반전이 시작되었습니다.
제어 엔지니어인 Chad Estes는 "초기 단계의 핵심 중 하나는 노조의 참여와 도움이었습니다. "노조 지도자들이 나와서 작업장과 작업장에서 이를 지지했습니다."
홀은 "리드 팀은 노조 지도부에 대해 많은 정보를 제공했습니다. "그들은 정보와 모든 숫자를 공유했습니다. 우리는 리드 팀 회의에 참석했습니다. 그 결과, 노조 지도부는 '우리는 이것을 지원할 것입니다. 우리는 직원들이 참여하도록 장려할 것입니다. 우리는 이점을 봅니다.'라고 말할 수 있었습니다."
당근으로서 Fox는 능동적인 조직으로 전환하면 기계공과 전기 기술자가 자신의 기술과 지식을 더 잘 사용할 수 있는 기회를 얻을 수 있다고 설명했습니다.
"나는 내 친구들이 게이트에서 두뇌를 떠나는 것을 원하지 않습니다."라고 그는 말합니다. "이 일은 그들의 힘과 근간 그 이상에 관한 것입니다. 저는 그들의 아이디어, 창의성 및 지성을 원합니다."
현금도 있었습니다.
일년 내내 다양한 마커에 도달하면 근로자가 성과 보너스를 받을 수 있습니다. Fox는 "그것은 추구할 가치가 있는 돈입니다."라고 말합니다.
Rx의 중요한 요소는 공식화되고 잘 정의된 파트너십이 유지 관리와 운영 사이에 필수적이라는 믿음입니다. 이 파트너십에서 작업은 장비를 소유하고 안정성에 대한 주요 이해 관계가 있습니다. 유지 관리는 적시에 효과적인 방법, 기술, 전문 지식 및 지원을 제공하기 위해 헌신하는 동등한 파트너입니다.
Todd는 "모든 것은 운영자로부터 시작됩니다. "그들은 매일 식물의 눈과 귀입니다."
직관적인 경험, 상태 판독값 및 프로세스 데이터를 기반으로 장비가 최적의 매개변수를 벗어나 작동하기 시작할 때 유지보수에 알릴 수 있습니다. 또한 광범위한 PM(예방 유지 관리) 작업을 수행하여 자산 상태를 지원합니다.
사실만 <블록 인용>
식물: 인디애나주 뉴버그에 있는 Alcoa Power Generating Inc. 공장은 4개의 석탄 연소 발전 장치와 해당 석탄 야적장으로 구성되어 있습니다. 1호기와 2호기는 1956년에 건설되었습니다. 3호기는 1962년에 건설되었습니다. 4호기는 1970년에 추가되었습니다.
식물 크기: 발전소 시설을 포함하는 Alcoa의 Warrick Operations는 총 9,000에이커에 걸쳐 있으며 그 중 120에이커는 지붕 아래 있습니다.
공장 고용: 유지보수 부서 45명을 포함하여 150명의 발전소 직원. 총 유지 보수에는 22명의 정비사, 15명의 전기 기사 및 8명의 급여 직원이 포함됩니다. International Brotherhood of Electrical Workers Local 702는 시간제 근로자를 대표합니다.
제품: 이 시설은 Newburgh에 있는 Alcoa의 알루미늄 제련 및 가공 작업에 전기, 증기, 온수 및 음용수를 제공합니다.
제작: 이 사이트는 732메가와트의 전력을 생성합니다.
참고: 이 발전소는 200,000명의 도시에 공급할 수 있는 충분한 전력을 생산합니다. ... 원래 Vectren Corp.에서 운영 및 유지 관리했습니다. ... Alcoa는 2001년 3월에 현장 운영 및 유지 관리를 인수했습니다. ... Vectren은 여전히 4호기의 50%를 소유하고 있습니다.
계획에 따라
전체 프로세스 구현은 2005년 후반에 시작되었습니다. 프로세스, 교육, 노조의 동의, 경영진 지원 및 견고한 기반이 마련되면서 발전소는 빠른 결과를 얻었습니다.
강조 및 성장 분야:
계획 및 일정: 3년 전, 유지 보수 조직은 교대 근무를 시작하고 운영자를 만나 어떤 자산이 파손되었는지 알아냈습니다. 그런 다음 작업은 단일 "계획자"에 의해 할당되었습니다. 미늘은 계획이 백지라는 것이었습니다. 오늘날에는 3명의 기획자로 구성된 팀이 2주 전에 정규 작업을 계획하고 유지 관리 및 운영 리더가 일정을 잡습니다.
Fox는 "모든 사람이 매일 무엇을 할지 알고 있습니다. "그들은 자신이 무엇을 성취해야 하는지 알고 있습니다. 얼마나 많은 인시가 필요한지, 그리고 이를 올바르게 수행하는 데 얼마나 필요한지 알고 있습니다."
계획은 제안이 아닙니다. 최고 수준에서 측정되고 모니터링되는 기대치입니다.
DeQuattro는 "일정을 준수하는 것이 중요합니다. "우리는 매일 그리고 매주 우리가 한 일과 일정에 대해 스스로를 추적합니다. 우리는 매일 모든 사람에 대해 합리적인 기대(RE)를 가지고 있습니다. 누군가는 하루에 X개의 작업을 완료할 수 있어야 합니다. 우리는 그것을 포착하고 RE에 도달하지 못하게 하는 문제를 포착합니다. 관리 또는 생산성을 저해하는 문제를 해결합니다. 가장 큰 병목 현상과 가장 많은 시간과 비용이 소요되는 문제에 중점을 둡니다."
대규모 정전에 대한 계획도 몇 달 전에 수행됩니다. 2008년에는 165일의 중단 날짜가 있을 예정입니다. 각 날짜는 하루뿐 아니라 어떤 경우에는 한 시간까지 조정되어 궁극적으로 일정에 대한 진행 상황을 추적하고 보장합니다.
계획된 다운타임 최대화: 또한 신중한 계획을 통해 자산 중단이 예정되어 있을 때 유지 관리에서 더 많은 보조 작업을 수행하고 완료할 수 있습니다.
Fox는 "더 짧은 시간에 더 많은 품질의 작업을 수행하고 있으므로 장치가 작동하는 동안 더 나은 신뢰성을 얻을 수 있습니다."라고 말합니다. "예전에는 3주 동안 중단되었던 정전이 이제는 12~14일입니다. 이 모든 것은 계획을 계획하고 실행하고 장치가 가동 중단되는 즉시 해당 계획을 실행할 준비를 하는 데서 비롯됩니다.
"다운되었을 때 장치에서 더 많은 작업을 수행하면 장치가 더 오래 실행되고 모든 일에 대해 다운되지 않습니다. 우리는 그 기간 동안 할 수 있는 모든 것을 처리합니다."
자산 내역: 3년 전만 해도 유지 보수 조직에는 서면 장비 이력이 없었습니다.
"그것은 모두 부족의 지식이었습니다."라고 전기 계획가인 Mark Payne은 말합니다. "아무것도 문서화되지 않았습니다."
마찬가지로, 청사진, 도면 및 기술 매뉴얼이 구식이거나 누락되었습니다.
"우리는 역사가 이제 시작된다고 말해야 했습니다."라고 Fox는 말합니다.
완료된 작업 주문 및 상태 보고서는 이제 개별 자산에 연결되고 공장의 Oracle 소프트웨어 시스템에 보관됩니다(2003년 10월에 가동되었으며 2005년부터 더 효과적으로 사용됨).
청소 활동에는 자재를 보관하는 구역이 있습니다. 작업자들은 인쇄물, 도면 및 설명서를 검토하고 업데이트가 필요한 항목에 플래그를 지정했습니다. 올바른 최신 매뉴얼을 디지털화하여 유지보수 컴퓨터에 PDF 파일로 저장합니다.
오늘날 작업 지시 패킷에는 숙련된 작업자가 작업을 완료하는 데 필요한 모든 정보가 포함되어 있습니다. 또한 장비에 대한 기록을 작성하는 작업 종료 피드백 양식도 포함되어 있습니다. 이 양식은 기술자가 작성하고 관리 비서가 Oracle에 입력합니다.
표준화된 작업: 작업 절차 및 프로세스의 공식 서면 표준화는 또 다른 주요 단계였습니다. 이 지침은 정비사, 전기 기술자 및 작업자가 작성하고 검토하고 승인합니다. 그들은 안전, 품질, 신뢰성 및 적시성을 가장 잘 보장하기 위해 작업을 수행하는 방법을 단계별로 설명합니다. 이 정보는 작업 주문 패킷에 들어 있습니다.
"그것은 사고방식의 변화를 가져왔습니다."라고 전기 유지보수 그룹의 리더인 Dan DeCastra는 말합니다. "여기에 있는 전체 인력은 신뢰성이 장기적 이익을 창출한다는 것을 알고 있습니다. 이를 제거하고 올바른 방법으로 수행하십시오. 장기적으로 보상을 받게 될 것입니다."
근본 원인에 집중: 공장은 패치워크 솔루션을 피하고 문제의 근본 원인을 해결하는 구제책을 추구했습니다.
"'수리하고 잊어버려'가 아니다. '다시는 이런 일이 발생하지 않도록 진짜 이유를 찾으러 가자'라고 기획자인 Tom Schmitt는 말합니다.
그것은 소방관 시절과 비교할 때 엄청난 변화입니다.
Fox는 "우리는 오류가 발생했을 때 최대한 빨리 해결하고 장치를 다시 온라인 상태로 만드는 데 매우 능숙했습니다."라고 말합니다. "때때로 원인을 알 수 없는 고장이 발생했습니다. 고장의 원인을 찾지 못했지만 장치를 다시 가동했습니다. 이제 무슨 일이 일어났는지 알 때까지 장치를 다시 켤 수 없습니다. 비용에 관계없이 공장 관리자가 직접 제공하는 것입니다. 나에게 그것은 아래에서 메인 맨의 지원을 보여줍니다."
문제 해결을 돕기 위해 유지 보수 작업자는 근본 원인 고장 분석에 대한 교육을 받습니다. 또한 5-why 비판적 사고 및 피쉬본 다이어그램과 같은 린 방법을 사용하는 방법도 배웁니다.
예측 유지보수: 이 기사의 앞부분에서 언급했듯이 Alcoa의 Warrick Power Plant는 대부분 40년 및 50년 된 장비에서 실행됩니다. 이는 예측 기술로 해결되는 과제를 제공합니다.
공장의 PdM 무기고는 적외선 열화상 측정, 진동 분석, 초음파, 저항 온도 장치, 망상 내시경, 그리고 (곧 제공될) 완전히 통합된 윤활/오일 표준화 및 상태 모니터링 프로세스와 같은 강력한 도구로 구성됩니다.
Fox는 "많은 경우 이 공장이 약 50년이 되었음에도 불구하고 우리는 일부 첨단 장비를 배치하고 직원들에게 사용법을 교육했습니다."라고 말합니다. "만약 이 사람들이 우리를 더 효율적이고 더 안정적으로 만들어 줄 장비를 요구한다면 나는 그것을 얻을 것입니다. 유지 관리 관리자로서 당신은 모든 새로운 기술에 뒤쳐지지 않아야 합니다. 좋은 것을 분리해야 합니다. 시설에 사용할 수 있고 그렇지 않은 경우."
이 부서는 적외선에서 가장 큰 영향을 받았습니다. 최근 애플리케이션을 통해 변압기의 핫스팟을 식별할 수 있었습니다. 변압기 고장으로 인해 플랜트는 수리 비용과 용량 손실로 수백만 달러의 손실을 입었을 것입니다. 문제를 조기에 파악하고 계획에 따라 필요한 수리를 수행함으로써 총 비용은 $55,000였습니다.
IR은 또한 부서의 시간과 노력을 절약하고 있습니다.
Alcoa는 NFPA 표준 70E보다 훨씬 더 엄격한 전기 고전압 안전 표준 32.60에 따라 작동합니다. 아크 플래시 위험은 심각한 문제입니다. 결과적으로 표준 적외선 조사를 수행하기 위해 전기실을 열려면 두 명의 전기 기술자가 "우주 비행사 복장"으로 알려진 100칼로리 레벨 5 복장을 입어야 합니다. 슈트는 필요하지만 번거롭다. 일반적으로 이 방법을 사용하는 작업자 2명이 한 장치에 들어 있는 차단기 18개를 스캔하는 데 4시간이 걸립니다.
적외선 공급업체인 Mikron이 적외선 카메라용 SpyGlass 어안 렌즈를 제공했을 때 안도감을 느꼈습니다. Alcoa는 정전 중에 전기 캐비닛 뒷면에 작은 포트를 설치했습니다. 이제 IR 스캔을 수행하기 위해 한 전기 기술자가 포트 덮개를 제거하고 SpyGlass 렌즈가 장착된 카메라를 포트에 놓고 구획을 열지 않고 후면을 촬영합니다. 100칼로리 슈트는 필요하지 않습니다. 발전소 작업자가 평소 바닥에서 착용하는 2등급 안전장비면 충분하다. 렌즈 솔루션은 장치당 IR 조사 시간을 4시간에서 20분 또는 30분으로 줄였습니다. 그리고 한 사람이 작업을 처리합니다.
차트 상승
휠에 스포크를 추가함으로써 Alcoa 공장은 실제로 사전 예방적 모드로 전환되었습니다. 2006년 초에 LCE에서 수행한 두 번째 Reliability Excellence 평가에서는 사이트를 0.652로 고정하여 컨설팅 회사의 성장 차트에서 "선제적" 영역의 중심에 배치했습니다.
LCE는 124포인트 증가가 Rx 프로세스 배포 역사상 가장 큰 첫 번째 평가에서 두 번째로 증가한 것이라고 말합니다. 제련소는 106포인트(2003년 .444에서 2004년 .550으로) 상승하여 이전의 최고 개선 사항 중 하나였습니다.
DeQuattro는 두 공장 간의 경쟁력을 얕잡아 보았지만 "때때로 형보다 더 나은 점수를 내는 데 신경 쓰지 않습니다."
2007년 1월에 수행된 세 번째 평가에서는 발전소를 62포인트 높은 0.714 - 36포인트로 "우수" 범주에 속합니다. (이 목표는 2008년 6월로 예정된 네 번째 평가를 통해 충족되어야 합니다.)
게다가 36개월의 마스터플랜을 30개월 만에 완성했다.
대체로 엄청난 노력을 기울였습니다.
"우리는 사막을 헤매고 다닐 시간이 없었습니다."라고 Fox는 말합니다. "10년 간의 노력으로 이 일을 할 수는 없었습니다. 우리는 계획이 있었고 그것을 따랐습니다. 이 모든 것은 공장의 모든 사람이 참여하지 않았다면 일어나지 않았을 것입니다."
보수 및 배당금
확실한 Rx 점수 외에도 많은 추가 혜택이 있습니다.
가장 눈부시고 결과적인 것은 2005년 Alcoa가 공장에 부여한 4억 4천만 달러의 자본 투자입니다. 현재 진행 중인 대규모 건설 프로젝트가 시설의 공간과 스카이라인을 바꾸고 있습니다.
DeQuattro는 "다른 많은 곳에서는 그렇지 않은데도 상당한 유지 자본 투자를 얻었습니다."라고 말합니다. "우리는 신뢰성 향상 프로세스, 우리가 수행한 철저한 분석 및 제공할 수 있었던 결과 덕분에 보상을 받았습니다."
투자는 공장의 미래와 신뢰성 이니셔티브의 미래를 확고히 했습니다.
Hall은 "이는 신뢰성의 중요성에 대해 여전히 존재하는 모든 회의론을 제거했습니다."라고 말합니다.
Alcoa 기업의 안정성은 금전적 보상도 받았습니다. Alcoa는 Midwest 대용량 전력 시스템의 안정적인 운영을 책임지는 기관인 Midwest Independent System Operators의 시장 참여자입니다. 인디애나 발전소가 전력을 보충하거나 공급할 수 없는 전력을 교체해야 하는 경우 MISO에서 시장 가격으로 구매해야 합니다. 가동 시간과 최적의 성능 덕분에 공장은 초과 전력을 판매하거나 높은 시장 수요를 충족하기 위해 추가 전력을 유료로 생성할 수 있습니다.
"1 메가와트가 초과되면 시장 가치로 판매할 수 있습니다."라고 Todd는 말합니다. "그것은 우리 비즈니스에 매우 큰 영향을 미쳤습니다. 그것은 우리가 제련 작업과 전력 시스템을 운영하는 방식을 변경할 많은 기회를 만들었습니다. 이 모든 것은 우리가 식물."
안정성이 향상되어 긴급 작업 비용이 크게 절감되었습니다. 작년에 공장은 이러한 활동을 위해 수리 비용으로 2백만 달러를 지출했습니다. 공장은 이 수치를 2007년에 $650,000로 낮추기 위해 속도를 내고 있습니다.
4년 전, 발전소 문제로 인해 제련소에서 거의 90번의 포트라인 중단이 발생했습니다. 올해는 7건이 되었습니다.
"신뢰성이 높아짐에 따라 우리가 제련소에 제공하는 전력 및 서비스 비용이 훨씬 낮아졌습니다."라고 Woods는 말합니다. "전체 기업의 비용이 더 저렴합니다."
Alcoa 직원들도 돈을 벌고 있습니다. Fox는 공장 직원들이 건전한 성과 보너스를 달성하는 것이 목표라고 말합니다.
기타 개인 혜택은 무엇입니까?
<울> <리>
조금 더 건전합니다. "불을 진압하기 위해 뛰어다니는 대신 오늘, 내일, 다음 주에 일어날 일에 대해 논의할 시간이 있습니다."라고 Strahl은 말합니다.
<리>
더 많은 가족 시간 주 80시간 근무는 과거의 일입니다. 몇 년 전만 해도 유지 보수 직원은 시간의 60%를 추가로 주말 교대로 일해야 했습니다. 오늘날 그 수치는 거의 0입니다. 모든 주말 시간은 작업 주문의 백로그를 줄이기 위해 특별히 설계되었습니다(2005년 26주에서 현재 9주로 이동). Fox는 "이것이 직원들의 사기와 삶의 질을 향상시키는 데 도움이 되었다고 생각합니다."라고 말합니다.
<리>
더 나은 숙면. Todd는 "개인적으로 신뢰성이란 한밤중에 전화를 받지 않는다는 것을 의미합니다."라고 말합니다. "우리가 90번의 중단을 받았을 때 나는 심야에 신뢰성 전화를 많이 받았습니다. 저는 공장에서 7마일 떨어진 고속도로에서 살고 있습니다. 나는 위기가 닥쳤을 때 11분 만에 공장에서 잠든 상태에서 여기까지 왔습니다. 1년에 여러 번 발생했습니다. 올해는 전혀 발생하지 않았습니다. 제게는 엄청난 일입니다."
끝? 끝이 없다
인디애나와 켄터키 신문은 뉴버그에서 신축 공사가 진행되고 있다고 연대순으로 보도했습니다.
Alcoa의 최근 연례 보고서에는 Warrick Power Plant에 대한 긍정적인 정보만 있었습니다.
이 잡지의 표지에는 유지 관리 부서가 나와 있습니다.
그런 홍보는 금물입니다.
Fox는 "열심히 일한 이들 모두가 주목을 받는 것을 보니 뿌듯합니다."라고 말합니다.
지도자들은 장애물이 남아 있음을 인정합니다.
DeQuattro는 "비용을 올바른 방향으로 유도하려면 생산성 향상으로 임금 인상을 계속 상쇄해야 합니다."라고 말합니다.
Fox는 "현재 예방 유지 관리 작업 지시를 97% 준수하고 있습니다. 이 부분은 제가 조금이라도 소리를 지르며 뛰어올라야 했던 영역 중 하나입니다. 허용되는 유일한 수치는 100%입니다."라고 말합니다.
Bloodworth는 "대부분의 경우 장비가 다운되는 것은 장비 때문이 아니라 작업자나 유지 관리 담당자 때문에 발생합니다. 인적 오류입니다. 우리는 이러한 인적 오류를 대부분 제거할 수 있도록 성능 교육을 진행하고 있습니다."라고 말합니다. /P>
하지만 사과할 필요는 없습니다. 달러와 센트, 백분율 포인트 및 신뢰성을 방해하는 나머지 요소를 적극적으로 찾는 것이 합리적입니다. 일에 끝이 없다면 잠재적인 보상도 끝이 없습니다.
ALCOA 공장은 숙련된 인력을 충원할 것으로 보입니다. <블록 인용>
Warrick Power Plant는 유동적인 유지 보수 인력을 처리하고 있습니다.
현재 승무원의 평균 연령은 45세이고 Alcoa의 평균 근속 기간은 15년입니다. 그러나 근로자의 연령과 근속기간이 고르게 분산되어 있지 않습니다.
지난 2년 동안 45명의 유지 보수 부서에서 6명의 직원이 퇴직했습니다. 향후 몇 년 동안 매년 4~5명의 은퇴가 추가로 예정되어 있습니다. 지난 18개월 동안 유지 관리 관리자인 Rick Fox는 빈 자리를 새로운 직원으로 채워왔습니다.
공장 관리자인 Peter DeQuattro는 "적절한 사람을 고용해야 합니다."라고 말합니다. "당신은 당신의 열정을 공유하는 팀에 적합한 사람들이 필요합니다. 그들은 까다로워야 합니다. 그들은 그 달러를 받으면 기뻐할 것이지만 다음 한 푼도 얻기 위해 열심히 일할 것입니다. 사람들은 탁월함에 대한 그 비전을 공유해야 합니다."
이 오래된 공장:유지 관리 인력이 어려운 상황을 최대한 활용합니다. <블록 인용>
인디애나주 뉴버그에 있는 Alcoa의 Warrick 발전소는 오래되었습니다.
몇 살입니까?
너무 낡아서 장비의 80%가 정품입니다(1950년대 중후반 및 1960년대 초 빈티지).
이는 공장과 유지보수 조직에 상당한 문제를 야기합니다.
유지 보수 관리자인 Rick Fox는 "예비 부품이 더 이상 없는 장비 문제에 일상적으로 부딪칩니다. "우리는 우리가 필요로 하는 것을 리버스 엔지니어링하고 제조하는 일을 꽤 잘 해왔습니다. 몇몇 지역 기계 공장은 그것에 관해서도 좋은 평판을 얻고 있습니다. OEM이 지원되지 않는 완전한 장비의 경우, 업그레이드된 모델 또는 이와 유사한 것으로 교체하겠습니다."
부서에서도 이리저리 뒤지는 것을 꺼려하지 않습니다.
Fox는 "우리는 현장에 나가서 그가 찾을 수 있는 모든 골조를 파헤치는 부품 expediter인 Kevin King을 두고 있습니다."라고 말합니다. "그는 아마도 90%의 성공률을 가지고 있을 것입니다. 이는 놀라운 일입니다."
Fox와 승무원은 현재에 살고 있지만 미래를 바라보고 있습니다.
"저는 우리가 운영하고 운영하는 대부분의 장비에 대해 계획된 유지 관리를 매우 잘 수행하고 있으며 꽤 좋은 상태로 유지하고 있다고 생각합니다. 교체했다"고 말했다. "우리는 매일 그것을 받아들이지만 실패로 인해 우리에게 닥칠 일에 대해서도 미리 내다보고 있습니다. 예측 유지 보수가 그 중 큰 부분을 차지합니다. 우리는 앞을 내다보려고 노력합니다. 우리는 10개년 자본 계획이 있음을 알고 있습니다. 장비가 너무 오래되어 더 이상 효율적이지 않거나 사용할 수 없게 되므로 주기적으로 교체해야 합니다."