창고 운영 모범 사례:창고 관리, 조직 및 운영을 개선하기 위한 55가지 유용한 팁 및 전술
창고 관리자는 창고 시설의 운영 관리 작업이 단순하지 않다는 것을 너무나 잘 알고 있습니다. 창고 운영 관리자는 시설 안팎으로 제품의 효율적인 흐름을 보장하고, 건물 레이아웃을 최적화하고, 주문이 이행되고 제품이 재고가 있지만 과잉 재고가 되지 않도록 해야 합니다. 수익성 보장과 간접비 및 인건비 최소화를 추가하면 창고 운영자가 자신의 작업을 줄일 수 있습니다.
균형을 맞춰야 할 요소가 너무 많고 모든 결정에 고려해야 할 고려 사항이 있으며 모든 측면에서 이해 관계자의 압력이 있습니다. 생산성을 높이고 비용을 최소화하며 원활한 공급망 흐름을 유지하기 위해 창고 운영 모범 사례를 설명하는 많은 기사와 리소스가 있다는 것은 놀라운 일이 아닙니다.
창고 운영 모범 사례에 대한 방대한 정보를 분석하려면 다양한 출처의 모범 사례를 비교적 간결하게 정리했습니다. 우리는 웹 구석구석을 샅샅이 뒤져 창고 운영에 대한 이러한 51가지 모범 사례를 식별하여 해당 분야에서 최고의 성과를 거두고 회사에 가능한 최고의 결과를 제공하려는 창고 관리자에게 유용한 리소스를 제공합니다. 주제별로 분류되지만 다음 모범 사례는 특정 중요도에 따라 다르게 평가되거나 순위가 매겨지지 않습니다. 특정 섹션으로 이동하려면 아래 목차의 링크를 사용하십시오.
창고 운영 모범 사례 55개
목차:
- 창고 운영을 위한 자산 추적 모범 사례
- 창고 운영 물류 모범 사례
- 창고 운영의 안전 및 위험 관리
- 창고 운영 워크플로 최적화
- 재고 관리 개선을 위한 모범 사례
창고 운영을 위한 자산 추적 모범 사례
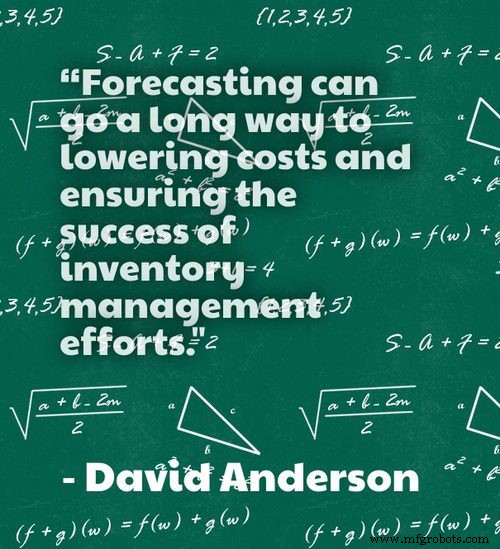
1. 자동 데이터 수집을 사용합니다. "'사람들이 종이에 숫자를 쓰거나 키보드에 숫자 문자열을 입력하는 것은 나쁜 징조입니다'라고 McKnight는 말합니다.
바코드 및 무선 주파수 식별을 통한 자동 데이터 수집의 이점은 잘 알려져 있습니다. 생산성과 정확성 향상, 인건비 절감 등을 포함합니다. 그러나 많은 기업이 여전히 자동 데이터 수집을 구현하지 않았습니다.
'30,000개 또는 40,000개 항목 번호와 여러 시설을 갖춘 일부 조직은 여전히 기술이 없는 것이 더 낫다고 확신합니다.'라고 McKnight는 말합니다. – Denny McKnight, 파트너, 노스캐롤라이나주 롤리에 본사를 둔 공급망 통합 회사인 Tompkins Associates Inc., Leslie Hansen Harps가 오늘날 유통 센터의 모범 사례에서 인용 , InboundLogistics.com
2. 수동 데이터 입력 프로세스에 의존하지 마세요. “대신:수신 도크에서 바코드 스캐너 또는 RFID 리더가 있는 모바일 컴퓨터를 사용하여 도착 즉시 제품을 식별하십시오. 이렇게 하면 제품을 도크에서 빠르게 꺼내고 식별, 계산 및 데이터 입력 오류를 포함하여 수동 수신과 관련된 거의 모든 오류를 제거할 수 있습니다. 스캐닝 및 RFID 기술을 사용하면 재고 정확성을 파괴하고 수정하는 데 시간과 리소스를 소모하는 실수를 피할 수 있습니다. 이는 창고 직원이 고객 주문 처리에 보다 신속하게 집중할 수 있음을 의미합니다." – 상위 10가지 창고 전략 손실 및 이를 방지하는 방법 , 모토로라 솔루션; 트위터:@MotoSolutions
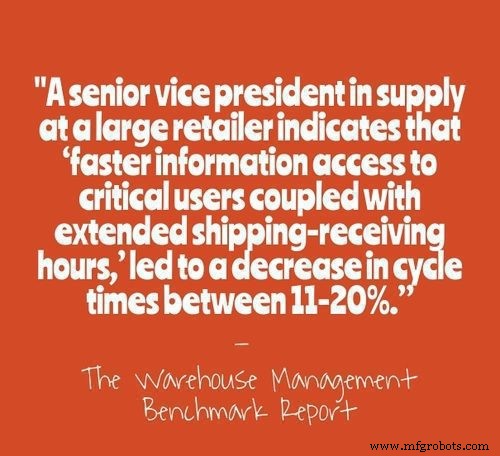
3. 전사적으로 정보 가시성을 높입니다. “Best in Class는 운영 전반과 회사 전반에 걸쳐 정보를 공유할 수 있도록 하는 광범위하게 확산된 창고 가시성 인프라를 가리킵니다. 또 다른 응답자는 가시성을 개선 수단으로 지적했습니다. 한 대형 소매업체의 공급 담당 수석 부사장은 '주요 사용자에 대한 더 빠른 정보 액세스와 연장된 배송 수령 시간'으로 주기 시간이 11~20% 감소했다고 밝혔습니다." – 창고 관리 벤치마크 보고서 , 애버딘 그룹; 트위터:@aberdeengroup
4. WMS(창고 관리 시스템)와 결합된 자산 추적은 창고 생산성을 극대화하는 데 필요한 자동화를 제공합니다. “똑똑한 기업은 재고, 주문 처리 및 배송 비용을 관리하는 것이 성공에 필수적이라는 것을 이해합니다. 기업은 민첩성, 가시성 및 노동 효율성을 높여 창고 운영을 개선하기 위해 끊임없이 노력하고 있습니다. 이를 위해서는 총 운영 또는 소유 비용(TCO)을 최소화하면서 유통 작업 내의 모든 리소스를 최적으로 관리하는 정교한 창고 관리 시스템(WMS)과 결합된 모범 사례를 사용해야 합니다.” – 창고 및 주문 처리:주문 처리 프로세스를 간소화하고 고객 만족을 유지 , 넷스위트; 트위터:@NetSuite
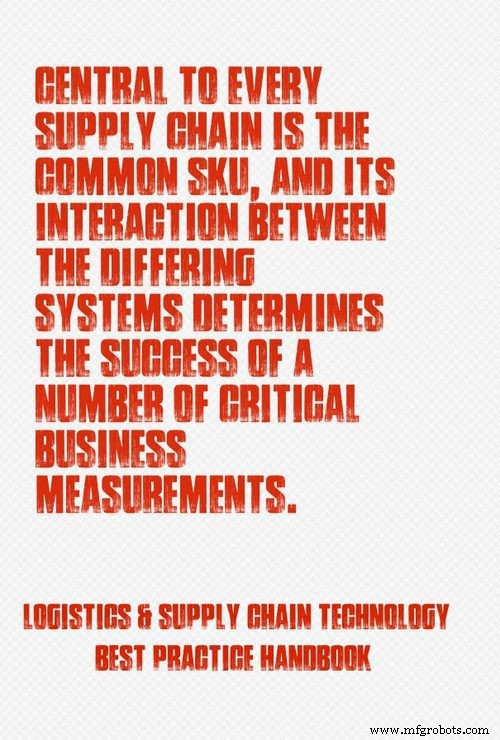
5. 데이터 동기화는 가시성을 개선하고 일반적으로 노동 집약적인 데이터 통합 작업을 간소화합니다. “모든 공급망의 중심에는 공통 SKU가 있으며 서로 다른 시스템 간의 상호 작용이 여러 중요한 비즈니스 측정의 성공을 결정합니다. 모든 규모의 조직에서 복잡한 소프트웨어 응용 프로그램 제품군 간의 데이터 흐름을 조화시키는 핵심은 기업 내에서 공통 SKU와 관련된 모든 데이터를 수평 또는 수직으로 동기화하는 것입니다. 시스템 수준에서 공통 제품 데이터를 표준화하고 데이터 변환에 대한 장벽이 없는 이러한 접근 방식은 노동 집약적인 데이터 통합 작업을 빠르게 대체하고 있습니다. 조직 간 데이터 거래의 다음 진화 단계는 데이터 저장소가 공급업체로부터 직접 최신 SKU 정보로 업데이트되는 단계입니다. 상호 운용 가능한 데이터의 이러한 전송은 이제 글로벌하고 비용 효율적인 수준에서 이루어지며 재고 리포지토리를 원활하게 업그레이드하고 키를 다시 입력할 필요가 없고 투명도가 줄어듭니다. WMS, BOS, POS 투자를 위해 SKU 정보의 연속성이 필수적인 모범 사례가 될 것입니다. 하나의 데이터 소스가 의미가 있습니다. 그 결과 소매업체, 공급업체 및 소비자 모두가 승자가 됩니다. 대부분의 회사는 반품 및 재배송을 제거하는 것을 목표로 하고 있습니다. 공급망 벌금 또는 지불 거절을 줄입니다. 더 나은 인보이스 매칭 및 재고 보유를 제공한다면 언젠가는 탄소 발자국보다 탄소
지문에 대해 이야기하게 될 것입니다.” – 물류 및 공급망 기술 모범 사례 핸드북 , 바스다; 트위터:@BASDAUK
6. 빈 위치를 사용하여 제품을 빠르게 찾습니다. “제품을 찾기 위해 빈 위치를 사용하고 있습니까? 오늘날 사용 가능한 대부분의 배포 소프트웨어 패키지는 빈 위치를 사용합니다. 이를 통해 쇼룸 및 창고 구역 내에서 제품의 즉각적이고 정확한 위치를 찾을 수 있습니다. 많은 유통업체는 공급업체 라인을 함께 유지해야 한다는 인식 때문에 이 도구의 활용을 꺼립니다. 실제로 빈 위치를 사용하면 판매량을 기준으로 제품을 찾을 수 있으므로 대부분의 주문에 표시되는 경향이 있는 주요 품목을 선택하는 데 필요한 단계 수를 줄일 수 있습니다. 나는 이것을 속도 순위로 제품을 찾는 것을 호출합니다.
“'온도 테스트'를 통과할 수 있습니까? 새로운 직원이나 임시 직원을 데려오고 이 직원이 2~3시간 내에 생산성을 발휘할 수 있다고 확신할 수 있습니까? 빈 위치를 활용하면 신입 사원이 따라갈 지도가 제공됩니다. 이를 통해 자재 취급 분야에서 숙련된 사람을 찾을 수 있습니다. 빈 위치가 없으면 주문을 채울 제품을 찾기 위해 가지고 있는 제품 라인 내에서 경험이 풍부한 사람을 찾아야 합니다. 그들은 서로 다른 제품 라인이 4개의 벽 내에서 어디에 보관되어 있는지 알기 위해 더 많은 손을 잡고 있어야 합니다.” – Dan Belanger, 효율적이고 안전한 창고 운영 시 해야 할 일과 하지 말아야 할 일 , 가스 및 용접 유통업자 협회(GAWDA); 트위터:@GasWeldEdge
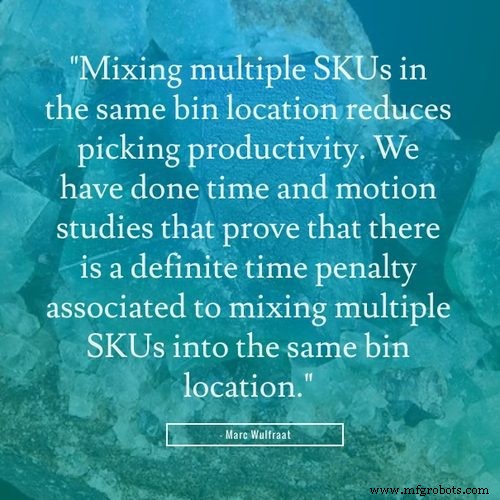
7. 단일 빈 위치에 여러 SKU를 혼합하지 마십시오. “동일한 빈 위치에서 여러 SKU를 혼합하면 피킹 생산성이 감소합니다. 우리는 여러 SKU를 동일한 빈 위치에 혼합하는 것과 관련된 확실한 시간 패널티가 있음을 증명하는 시간 및 동작 연구를 수행했습니다.
“빈 위치가 5개를 포함하는 선반 수준을 나타낼 수 있는 많은 창고에서 이러한 현상을 볼 수 있습니다. – 10 SKU 선택 페이싱. 작업자는 선반 수준으로 이동한 다음 선택할 항목을 찾기 위해 다양한 SKU를 검색해야 합니다.
“이렇게 하면 정확도가 떨어질 뿐만 아니라 작업자의 속도가 15초 이상 느려집니다. 피킹 트랜잭션 당. 모든 SKU에 대해 개별적인 선택 위치를 갖는 것이 규칙 #1입니다.” – Marc Wulfraat, MWPVL 사장, 주문 피킹 생산성을 향상시키는 5가지 방법 , 공급망247; 트위터:@SupplyChain247
8. 자산 추적 시스템을 사용하여 특정 기간 동안 인벤토리가 선택된 횟수를 기록합니다. “상품 재고를 확보하는 것이 합리적이지 않을 때가 있습니다. 예를 들어 1년에 5번만 품목을 선택하는 경우 제조업체의 직송을 통해 보관 비용을 없앨 수 있습니다. 제품이 선택된 횟수를 기록하여 재고가 있는 공간의 가치를 결정할 수 있습니다.” – 모범 사례 – 재고 관리 , 프로모션 이행 센터; 트위터:@PFCFulfillment
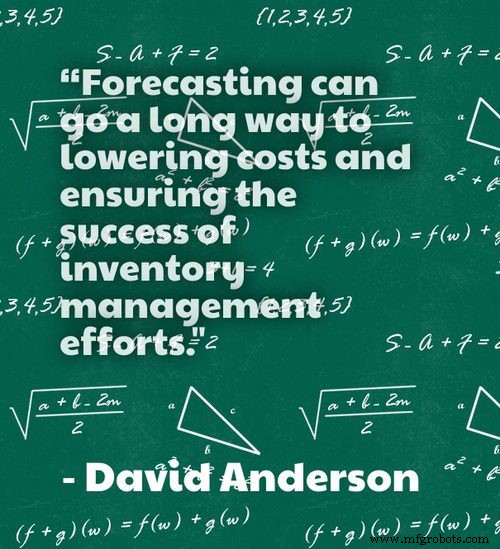
9. 자산 추적을 사용하면 비용을 절감하고 재고 관리를 개선하는 데 필수적인 보다 정확한 예측이 가능합니다. “예측은 비용을 낮추고 재고 관리 노력의 성공을 보장하는 데 큰 도움이 될 수 있습니다. 소매업체가 필요한 품목과 정확한 수량을 정확하게 예측할 수 있을 때 잉여 재고 없이 고객의 기대를 충족하는 데 더 적합할 것입니다. 더 나은 예측을 위해서는 시장 조사, 시장 수요 모델, 수요 패턴, 최소 재고 수준 및 과거 기술에 대한 능숙한 관찰이 필요하며 성공적인 재고 관리에 큰 역할을 할 수 있습니다.” – David Anderson, 재고 관리 모범 사례 3가지 , SalesWarp; 트위터:@SalesWarp
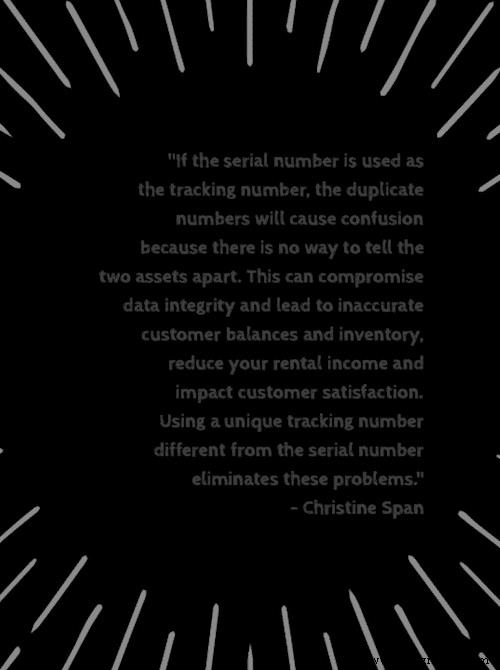
10. 자산의 일련 번호가 아닌 고유한 추적 번호를 사용하십시오. "자산의 일련 번호가 다른 자산의 일련 번호와 동일할 수 있습니다. 일련 번호를 추적 번호로 사용할 경우 두 자산을 구분할 수 있는 방법이 없으므로 중복된 번호로 인해 혼동이 발생할 수 있습니다. 이는 데이터 무결성을 손상시키고 부정확한 고객 잔액 및 재고로 이어져 임대 수입을 줄이고 고객 만족도에 영향을 미칠 수 있습니다. 일련 번호와 다른 고유한 추적 번호를 사용하면 이러한 문제가 해결됩니다. 추적 번호를 분실한 드문 경우에도 일련 번호를 사용하여 자산을 조회하고 자산 기록을 유지하기 위해 적절하게 레이블을 다시 지정할 수 있습니다.” – Christine Span, 상위 5가지 자산 추적 모범 사례 , TrackAbout; 트위터:@trackabout
창고 운영 물류 모범 사례
11. 고급 배송 알림을 설정합니다. “간단한 일처럼 보일 수 있지만 많은 물류 센터에서 전자적으로 전송되는 ASN(Advanced Shipping Notifications)을 아직 구현하지 않았습니다. "정기적인" 배송 및 입고 일정에 의존하면 물류 센터 전체에서 비효율적인 결과를 초래할 수 있습니다. 지연이 발생하고 중단이 발생하며 "정규" 일정에서 벗어나게 됩니다. 결과적인 문제는 입고 부두의 부적절한 직원 배치로 시작되어 창고 전체에 파급됩니다. 그러나 구매 주문 및 재고 관리 기능 내에서 전자 고급 배송 알림을 활용하면 작업을 보다 확실하게 계획할 수 있습니다. 적절한 서비스 시간 요구 사항이 충족되도록 주문 이행 및 운송 활동을 조정할 수 있으며 운송 모드는 비용 절감을 위해 최적화됩니다.” – 11 공급망을 위한 창고 및 유통 센터 모범 사례 , 기존 공급망 서비스
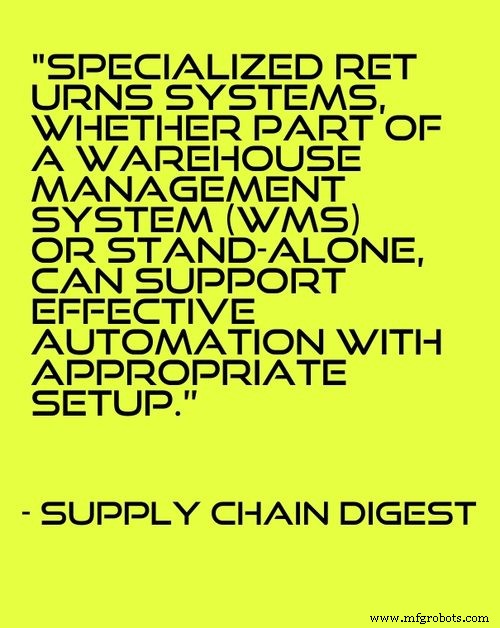
12. 효율적인 반품 프로세스를 구현하세요. “반품은 재고 실사, 전자 재고 및 회계 시스템에 미치는 영향 때문에 근본적으로 복잡합니다. 모든 항목을 식별하고 고객 또는 계정에 할당하고 처리를 할당한 다음 물리적으로 분류하여 처리해야 합니다. 일부 제품은 공급업체 지불 거절을 위해 폐기되거나 보관될 수 있으므로 모든 상품이 전자 재고에 들어가는 것은 아닙니다. 일부 상품은 재포장해야 하며 수동 대 전자 계산이 필요합니다. 마지막으로, 크레딧은 일반적으로 나중에 폐기되거나 판매 불가능한 상품을 포함하여 반품의 일부에 대해서만 발행됩니다. 이 프로세스는 일반적인 ERP 패키지로 자동화하기 어렵고 간단한 종이 프로세스로는 매우 어렵습니다. WMS(창고 관리 시스템)의 일부이든 독립 실행형이든 특수 반품 시스템은 적절한 설정으로 효과적인 자동화를 지원할 수 있습니다.” – Expert Insight:창고 반품 모범 사례 , 공급망 다이제스트; 트위터:@scdigest
13. 작업을 효율적으로 처리하고 미루지 마십시오. “가끔 공급업체로부터 대량의 배송물을 받을 때 '올'을 주기 쉽습니다. 이것만 나중에 처리하자.” 미루는 일을 끝내고 시간을 내어 상자를 부수고, 재활용 쓰레기통에 넣고, 제품 포장을 풀고 그에 따라 비축해 두십시오. 이것은 반드시 지켜야 하는 습관입니다. 배송이 매일/매주 같은 시간에 오면 달력에서 일정을 잡으십시오. 미루면 더 큰 야수가 되어 당신의 주의를 기다립니다.
“선반에 물건을 둘 시간이 없다면 소매업에서 일할 때 하던 또 다른 일은 저였습니다. 모든 상자를 가져 와서 줄을 서겠습니다. 하나하나 열어서 뭐가 들어있는지 보세요. 거기에서 각 상자에 미니 스타킹 더미를 만드십시오. 결국 어디에 보관될지 알고 가까운 곳에 있는 품목을 함께 배치하면 창고 바닥의 올바른 위치로 가져와 신속하게 비축할 수 있습니다.” – Breena Fain, 창고 관리 시스템을 최적화하는 6가지 방법 , 스티치랩스; 트위터:@StitchLabs
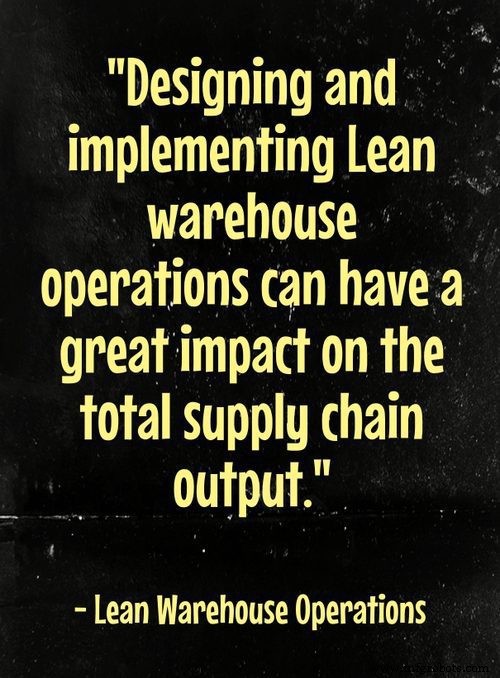
14. 린 창고 운영 방식을 구현합니다. “린(Lean) 창고 운영을 설계하고 구현하면 전체 공급망 산출물에 큰 영향을 미칠 수 있습니다. 린 솔루션으로 위에서 언급한 폐기물 집중 영역에 접근함으로써 창고 보관의 리드 타임을 단축할 수 있는 몇 가지 기회는 다음과 같습니다.
- 주문 피킹, 폐기, 팔레타이징 및 배송 시 자재 처리 시간 단축
- 나머지 공급망을 조정하기 위한 정보의 신뢰성
- 트럭 및 컨테이너 적재 및 하역 시간 감소
- 재고 확인 및 검색에 소요되는 시간 감소
- 변화하는 시장 상황과 고객 사양에 적응할 수 있는 유연성 향상." – 린 창고 운영 , 네 가지 원칙
15. 인바운드 및 아웃바운드 화물을 제어하여 이 비용 영역을 줄입니다. “가상 라이브러리는 이 비용 영역을 줄이거나 늦추는 방법에 대한 기사로 가득 차 있습니다. 이익 침식을 방지하기 위해 지속적으로 최우선적으로 집중해야 합니다. 경쟁력 있는 입찰에 도움이 되도록 컨설턴트를 활용하십시오. 운송업체 계약은 독점적이지만 숙련된 컨설턴트는 서비스 수준을 해치지 않으면서 감소를 협상할 영역을 식별하는 데 여전히 도움이 될 수 있습니다." – Curt Barry, 창고 효율성을 높이고 비용을 줄이는 10가지 방법 , 다중 채널 판매자; 트위터:@mcmmerchant
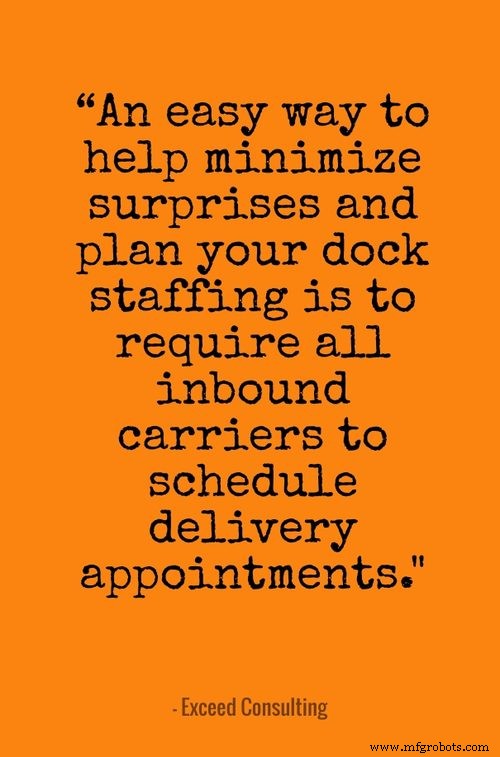
16. 공급업체가 약속을 받아야 합니다. “놀라움을 최소화하고 부두 직원 배치를 계획하는 데 도움이 되는 쉬운 방법은 모든 인바운드 운송업체가 배송 약속을 예약하도록 하는 것입니다. 일정을 잡는 방법에는 두 가지가 있으며 동시에 사용할 수 있습니다. 첫 번째 방법은 단순히 각 운송업체 또는 배송을 특정 시간 또는 배송 창구에 지정하는 것입니다. 두 번째는 특정 또는 반복되는 매일, 매주 또는 매월 일정을 지정하여 도착하도록 지정하는 것입니다. 이를 통해 직원을 적절하게 예약하고 도크를 최대한 활용할 수 있습니다. 동일한 지역에서 인바운드 및 아웃바운드 둘 다를 선적하거나 선적을 공유하는 경우 공급업체 수신 약속은 절대적으로 중요합니다. 배송이 이루어지기 전에 사전 서류나 데이터를 제공해야 합니다. 약속과 들어오는 부하에 대한 정보를 요구함으로써 놀라움을 최소화할 수 있습니다.” – 기본으로 돌아가기, 1부:받기 , 초과 컨설팅
17. 가치별로 인벤토리를 분류하는 데 도움이 되는 ABC 분석을 수행합니다. “ABC는 가장 가치 있는 항목의 계층 구조입니다(달러 가치 기준). 이를 재고 분류 방법이라고도 합니다. 전체 주식의 가치를 동등하게 평가할 수 없기 때문에 이 컨트롤을 사용하면 가장 많은 돈을 버는 아이템에 시간과 자원을 집중할 수 있습니다.
“A- 아이템은 고가 또는 우선주입니다. 이러한 상품은 가장 큰 수익 및 비용 기여자이기 때문에 보다 엄격한 통제와 모니터링이 필요합니다. 비용으로 인해 더 적은 양을 손에 들고 다닐 가능성이 큽니다. 이러한 품목은 수요가 많기 때문에 "잠금 및 열쇠" 아래에 보관해야 합니다. 보안 외에도 A-list 제품은 재고 검토 및 재주문 빈도를 높여야 합니다. 이렇게 하면 적절한 공급이 보장됩니다.
“반대로 C 항목은 값이 더 낮지만 많은 양을 휴대할 수 있습니다. 예를 들어 철물점을 소유한 경우 대량의 못은 C 품목으로 간주될 수 있습니다. B 품목은 가치, 수량, 재고 검토 및 재주문 빈도의 중간에 있습니다.” – Colleen Rodericks, 재고 관리 기술 및 모범 사례 , 유입; 트위터:@inFlowInventory
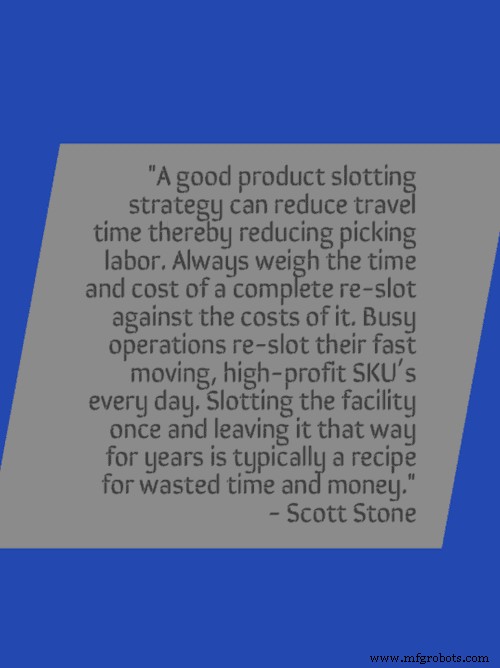
18. 필요할 때마다 선택 위치를 다시 지정하십시오. “피커의 일일 활동 중 최대 60%가 이동 시간(보행 또는 지게차 또는 무전기)과 관련될 수 있으므로 이러한 시간 소비를 줄이는 것은 훌륭한 아이디어입니다. 좋은 제품 슬롯 전략은 이동 시간을 줄여 피킹 노동력을 줄일 수 있습니다. 비용 대비 완전한 재슬롯의 시간과 비용을 항상 저울질하십시오. 바쁜 운영은 빠르게 움직이는 고수익 SKU를 매일 다시 할당합니다. 시설을 한 번 슬롯에 넣고 몇 년 동안 그대로 두는 것은 일반적으로 시간과 돈을 낭비하는 방법입니다.” – Scott Stone, 창고 생산성을 위한 13가지 모범 사례, 시스코-이글; 트위터:@CiscoEagle
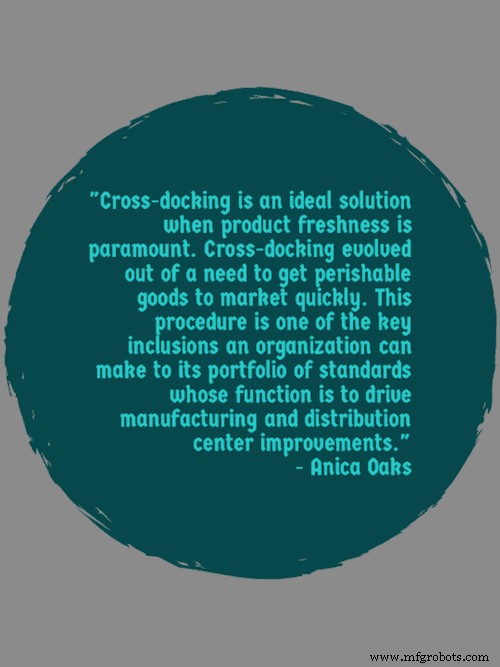
19. 가능한 한 교차 도킹을 활용합니다. “우수한 물류 계획에는 가능한 한 교차 도킹이 포함됩니다. 교차 도킹은 입고 차량에서 자재를 하역하고 최소한의 또는 0의 창고 간격으로 이러한 동일한 자재를 아웃바운드 차량에 직접 적재하는 관행입니다. 이것을 "Just-in-Time" 배송이라고 생각하십시오. 교차 도킹은 제품 신선도가 가장 중요한 경우 이상적인 솔루션입니다. 교차 도킹은 부패하기 쉬운 제품을 빠르게 시장에 출시해야 하는 필요성에서 발전했습니다. 이 절차는 조직이 제조 및 유통 센터 개선을 주도하는 기능을 가진 표준 포트폴리오에 포함할 수 있는 핵심 요소 중 하나입니다.” – Anica Oaks, 5 Lean Best Practices for the Warehouse, Apriso 제조 혁신 블로그; 트위터:@Apriso
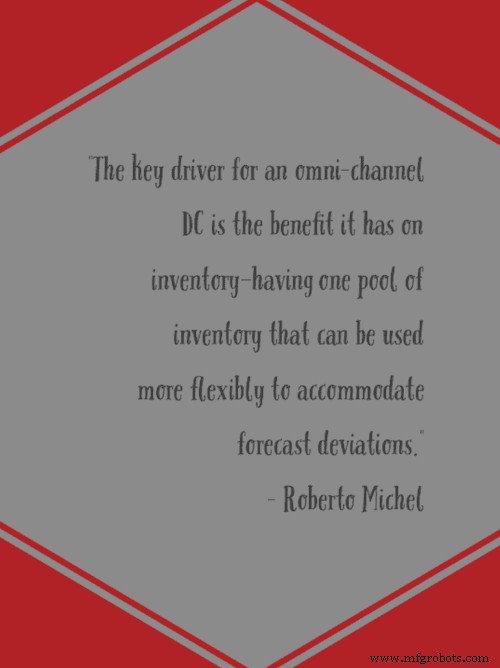
20. 여러 채널의 주문을 처리하는 DC를 만듭니다. Commonwealth Supply Chain Advisors의 설립자이자 전무 이사인 Ian Hobkirk는 "옴니채널 처리 효율성을 원하는 일부 회사의 경우 단일 채널 전용 DC에서 벗어나 여러 채널의 주문을 처리하는 DC를 사용하는 추세였습니다. .
“'10년 전 전자 상거래가 아직 상당히 생소했을 때 회사에서 DC를 설정하고 운영하는 방식에서 많은 채널 분리가 있었고 전자 상거래 이행은 많은 경우에 아웃소싱되었습니다. 3PL'이라고 Hobkirk는 말합니다. '현재 소매업체에서 보고 있는 트렌드 중 하나는 모든 채널의 재고 및 주문 처리가 동일한 지붕 아래 있는 다중 채널 주문 처리 센터를 보유하는 것입니다.'
“옴니채널 DC의 핵심 동인은 인벤토리에 대한 이점 - 예측 편차를 수용하기 위해 보다 유연하게 사용할 수 있는 하나의 인벤토리 풀이 있습니다. Hobkirk는 '공동 인력 풀을 사용할 수 있어 비용이 절감되는 것과 같이 옴니채널 주문 처리 센터를 구동하는 다른 요인이 있지만 이러한 추세를 진정으로 주도하는 것은 재고 요인입니다.'라고 Hobkirk는 말합니다.
“증가 옴니채널 이행의 증가는 재고 관리를 더욱 복잡하게 만들고, 이는 창고 관리 시스템(WMS), 전사적 자원 관리(ERP), 수요 관리 및 교차 관리를 포함하여 실행, 예측 협업 및 관리 보고를 위한 더 나은 시스템의 필요성을 높입니다. - 공급망 자문 회사인 St. Onge Company의 수석 컨설턴트인 Don Derewecki는 학문 분야의 협력이 필요하다고 말합니다.” – Roberto Michel, 창고/DC 관리:더 나은 재고 관리를 위한 6가지 모범 사례 , 물류 관리; 트위터:@LogisticsMgmt
창고 운영의 안전 및 위험 관리
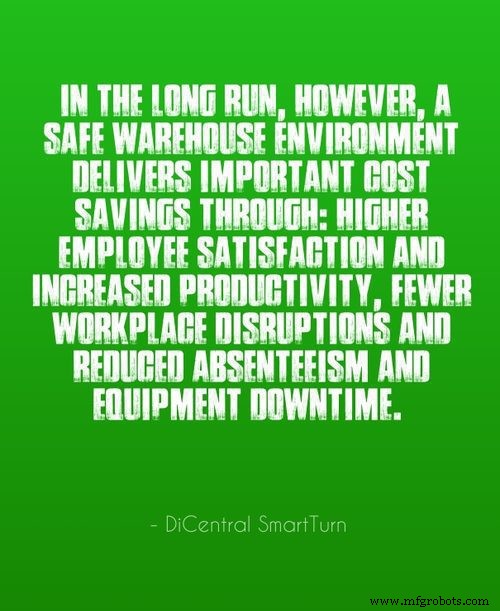
21. 창고 안전을 최우선으로 생각하십시오. “창고 안전에는 소방 법규 및 OSHA 규정 준수보다 더 많은 것이 있습니다. 불행히도 너무 많은 창고와 3PL은 안전을 법률이나 양심이 요구하는 최소 수준을 충족하는 것으로 간주합니다. 종종 어느 쪽도 충분하지 않습니다. 이 장에서 우리는 창고 안전을 위한 모범 사례를 살펴보고 창고에서 안전 문화를 조성하고 그렇게 하지 않을 때 직원, 관리자 및 고용주 모두에게 미치는 이점과 위험에 대해 논의할 것입니다. 안전을 도모하지 못하는 기업의 경우 시간 부족, 자원 부족, 코너 커팅을 통해 비용을 절감할 수 있는 기회가 원인인 경우가 많습니다. 그러나 장기적으로 안전한 창고 환경은 직원 만족도 향상, 생산성 향상, 작업 중단 감소, 결근 및 장비 가동 중지 시간 감소를 통해 중요한 비용 절감 효과를 제공합니다. 보관 및 자재 취급 장비와 같은 창고 인프라의 수명을 연장하고 재고 손상을 줄일 수 있습니다. 가장 중요한 것은 안전한 작업장에 입이 떡 벌어지는 가격표가 붙어 있다고 가정하지 마십시오.” – 재고 및 창고 관리 모범 사례 , 디센트럴 스마트턴; 트위터:@DiCentral_EDI
22. 안전 위원회를 구성하십시오. "특별히 심각하지는 않지만 창고 사고는 수없이 많습니다. 미국 노동 통계국에 따르면 창고 및 보관 산업에서 매년 거의 15,000건의 부상과 질병이 발생합니다.
"사고를 방지하기 위해 창고 운영자는 다음과 같이 강조해야 합니다. 일리노이주 오크 브룩에 소재한 창고 관리 및 공급망에서의 역할을 전담하는 조직인 창고 교육 및 연구 위원회(WERC)의 전무이사인 Bob Shaunnessey는 작업자 교육을 실시하고 안전 모범 사례를 확립한다고 말합니다.
“대부분의 창고에서 안전 위원회를 구성하는 것은 강화된 안전 절차를 구현하기 위한 첫 번째 단계입니다.
“안전 위원회의 구성원은 일반적으로 창고 작업자, 교대 감독자 및 부서 관리자를 포함한 특정 조직 그룹에서 선택됩니다. 이 접근 방식은 모든 사람에게 발언권을 주지만 위원회의 규모는 유효 참가자 수로 유지합니다.” – John Edwards, 창고 안전:사고가 아닙니다 , 인바운드 물류; 트위터:@ILMagazine
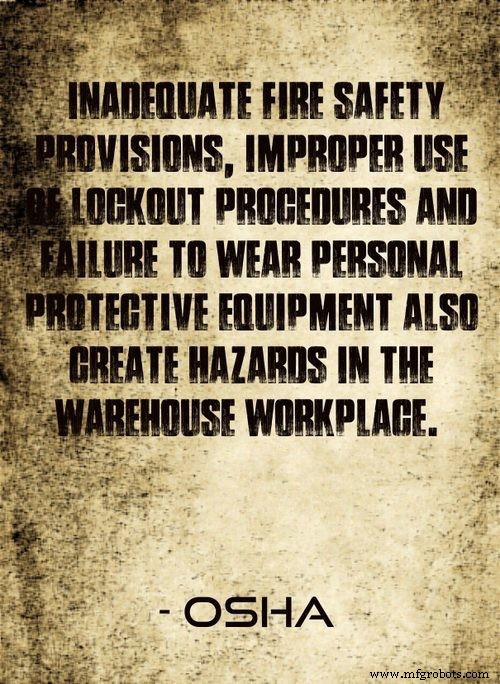
23. 비상 대응 계획을 마련하십시오. “부적절한 화재 안전 규정, 잠금 절차의 부적절한 사용, 개인 보호 장비 미착용도 창고 작업장에서 위험을 초래합니다. 고용주는 다음을 포함하여 비상 사태 발생 시 직원에게 예상되는 사항을 설명하는 비상 계획을 세워야 합니다.
• 비상구 위치 및 대피 절차 제공
• 모든 직원 및 방문자 계산 절차
• 소화기 및 기타 비상 장비의 위치 및 사용." – OSHA 포켓 가이드, 근로자 안전 시리즈:창고 , OSHA.gov; 트위터:@usdol
24. 하역장과 대기 장소에서 흔히 발생하는 사고를 피하세요. “하역장이나 대기 장소는 창고의 공통 영역으로 부상과 제품 손상이 발생합니다. 일반적인 위험은 다음과 같습니다.
• 직원의 머리, 발, 팔, 다리에 제품이 떨어지는 경우
• 혼잡을 초래하는 약한 청소 프로그램
• 직원이 건물에서 뛰어내리는 경우 높은 고도에서 낮은 고도로;
• 도크 플레이트를 들어 올리고 지속적으로 조정합니다. 및
• 부두에서 굴러가는 지게차 또는 팔레트 잭.
“통제에는 다음이 포함됩니다:
• 도크 플레이트가 넘어지지 않도록 고정합니다.
• 적재물 및 임시 보관 장치에 대한 일일 검사 수행
배치,
• 절대 안 함 지게차 또는 팔레트 잭이 도크의 가장자리로 돌아갈 수 있도록 허용합니다.
• 직원이 더 높은 도크에서
낮은 지면으로 이동하는 것에 대한 안전 규칙을 시행합니다. 및
• 지정된 안전 검사 양식 모니터링 West Bend; 트위터:@WBsilverlining
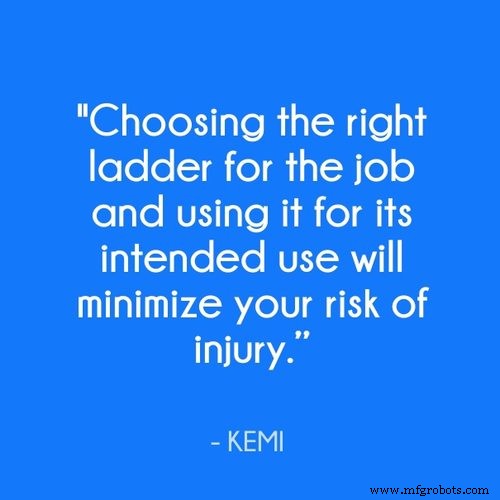
25. 창고 내 다양한 작업에 적합한 사다리를 제공하고 작업자가 작업에 가장 적합한 사다리를 쉽게 식별할 수 있도록 교육을 제공합니다. “자재 취급만이 창고 내에서 부상을 입을 수 있는 유일한 원인은 아닙니다. 공간을 보다 효율적으로 사용하려면 항목을 쌓아야 할 수 있습니다. 사다리를 사용하여 선반이나 선반의 상단에 도달할 수 있습니다. 작업에 적합한 사다리를 선택하고 용도에 맞게 사용하면 부상 위험을 최소화할 수 있습니다.” – 창고 안전 , KEMI
26. 엎질러진 것을 가능한 한 빨리 청소하고 직원이 잠시 동안 해당 지역을 비워야 하는 경우 통로에서 재고 및 공급품을 제거합니다. “창고는 물건이 많은 곳입니다. 좁은 통로, 높은 상품 더미, 열악한 조명은 가시성을 손상시킬 수 있는 정확한 요소입니다. 창고가 적절한 조명을 유지하고 어두운 구석에 쉽게 켜고 끌 수 있는 특수 조명을 장비하면 자재 또는 엎질러진 액체에 미끄러지거나 걸려 넘어지는 일반적인 사고를 피할 수 있습니다. 불필요한 계단이나 능선을 제거하고 직원이 화물, 상자 및 물건을 바닥에 방치하지 않도록 권장합니다.
“창고 작업자가 일시적으로 바닥을 떠나야 하는 경우 자재를 옮기는 것이 중요합니다. 불이 켜진 상태에서 통로 중앙에서 무언가를 엎지른 경우 직원은 적절한 조치를 취하여 눈에 띄는 표지판이 있는 구역을 폐쇄하고 가능한 한 빨리 청소해야 합니다.” – Tom Reddon, 가장 일반적인 창고 사고를 피하는 4가지 방법 , 직장에서의 지식
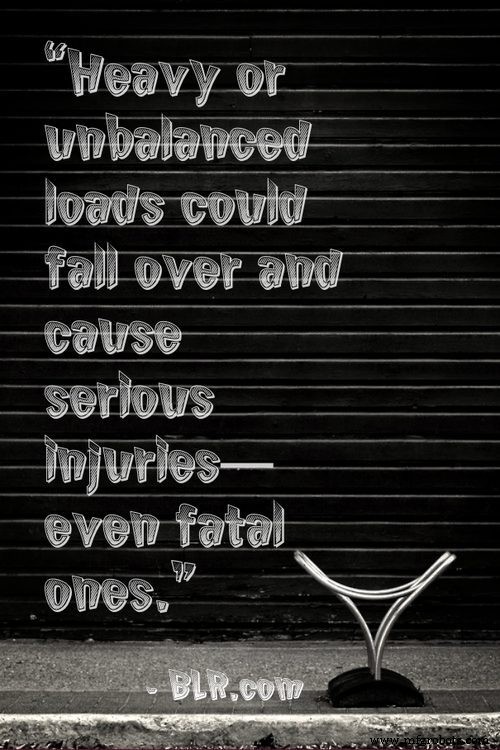
27. 훈련을 받은 작업자만 지게차, 크레인, 호이스트와 같은 장비를 사용해야 합니다. "지게차와 핸드 트럭이 위험할 수 있는 유일한 창고 장비는 아닙니다. 움직이는 컨베이어 부품과 접촉하면 심각한 부상을 입을 수 있습니다. 그렇기 때문에 경비원을 제자리에 유지하는 것이 매우 중요합니다. 크레인, 호이스트 및 데릭은 하중이 매달린 상태에서 사람 위로 하중을 휘두르거나 제어 장치에서 손이나 발을 떼는 것을 충분히 알고 있는 숙련된 작업자만 조작할 수 있습니다. 또한 주변에서 일하는 사람은 크레인의 움직임에 주의해야 합니다. 크레인 아래에서 일하거나 서 있으면 문제가 발생합니다. 이 장비가 적재되는 방식에서도 위험 요소를 발견할 수 있습니다. 무겁거나 불균형한 하중이 넘어져 심각한 부상을 입힐 수 있습니다. 심지어 치명적인 부상을 입힐 수도 있습니다.” BLR.com; 트위터:@BLR_INC
28. 화재 위험을 최소화하려면 건전한 보관 방법을 사용하십시오. “저장 방법은 동일한 재료에 대한 화재 확산 속도와 심각성에 영향을 줄 수 있습니다. 예를 들어, 수직으로 보관된 종이 릴은 스택 효과를 일으킬 수 있습니다. 실내 보관의 경우 권장되는 최대 말뚝 높이는 4.5m입니다. 말뚝 꼭대기에서 지붕 부재, 전기 설비 또는 화재 감지기의 가장 낮은 지점까지의 거리는 최소 1m이어야 합니다. 재료를 쌓을 수 있는 최대 높이를 나타내기 위해 벽에 색 띠를 칠해야 합니다.” – N.V. Subba Rao 및 K. Ramish Ramalingham, 창고의 위험 관리 , Cholarisk.com
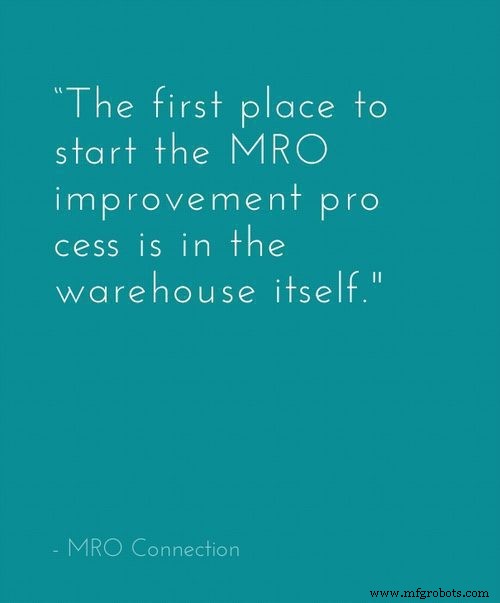
29. 항상 안전 장비를 사용해야 합니다. “창고에서는 지게차나 유압식 돌리를 사용하여 너무 무거운 품목을 들어 올리는 것이 중요합니다. Appropriate eyewear and hard hats should also be worn when required. Employees should be aware of emergency exits and the sprinklers installed in the roof should not be blocked at any time. Safety equipment is implemented in order to minimize workplace injury, so although it may be time consuming to initiate its use, it does pay off in the long run.” – Warehouse Safety Principles:6 key guidelines to keep your workplace safe. , AdaptALift; Twitter:@aalhyster
30. Post safety expectations in highly visible locations and key areas. “Warehouse supervisors should ensure all safety expectations are posted clearly in close proximity to all equipment—forklifts, hydraulic dollies, hand jacks, etc. Doing so assures that employees have constant visual reminders of the inherent dangers of using such equipment, and the safety precautions they should take to avoid injury.” – Warehouse Safety Checklist:8 Things Every Manager Should Review , Legacy Supply Chain Services; Twitter:@legacyscs
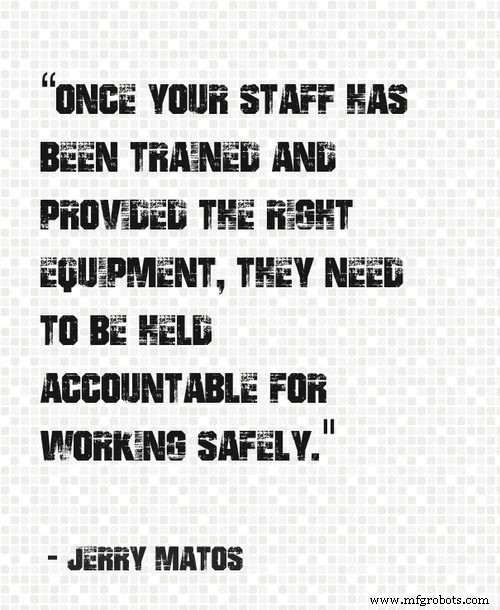
31. Establish accountability and give staff a sense of ownership over warehouse safety practices. “Once your staff has been trained and provided the right equipment, they need to be held accountable for working safely. This must apply to everyone in your warehouse. You cannot overlook bad habits of supervisors while reprimanding a dockworker. How you handle safety infractions is up to you, but your employees must own their actions. You will see better results if you offer suggestions for safer operation at the same time you express criticism.
“You do need to document lapses in safety. Without proper records, you may not have the backup you need to take action against an employee that continues to ignore your requirements. Documentation will also help protect you if an employee is injured performing an action after they have been instructed otherwise.” – Jerry Matos, Product Specialist, Cherry’s Industrial Equipment, 6 Ways To Encourage Warehouse Safety , Industrial Distribution; Twitter:@indistwebsite
32. Consider enlisting an outside expert to identify warehouse hazards. “To help improve the safety in the workplace, consider bringing in an outsider. The outsider does not necessarily need to be a consultant or OSHA representative, but may be a business associate, or peer. The point is to have a fresh pair of eyes evaluate the warehouse. Sometimes what is seen in plain sight every day may be an overlooked hazard.” – Best Practices for Warehouse Safety , Labor Law Center
Optimizing Warehouse Operations Workflows

33. Clear aisles make for an efficient flow of inventory. “The movement of inventory throughout the warehouse should be done by experienced materials handlers with certifications or licenses to operate forklifts and boom lifts. These materials handlers should be able to move from one section of the warehouse to another with ease due to aisles that are not full of unstored inventory. Inventory that has not been placed in its proper bin or warehouse location can cause problems with inventory systems, especially under a FIFO, or First In, First Out, inventory system. A FIFO system ensures that the inventory that was received yesterday is moved to the shipping dock before the inventory that was received today. This inventory system reduces the chance of obsolete inventory sitting in warehouse bins.” – Justin Johnson, Best Practices in Warehouse Operations , Chron.com
34. Store the most frequently picked items close to the shipping area. “When considering the level of effort involved in warehouse operations, the greatest expenditure of effort is in the picking process. To gain efficiencies in picking the labor time to pick orders needs to be reduced and this can achieved in a number of ways. Companies with the most efficient warehouses have the most frequently picked items closest to the shipping areas to minimize picking time. These companies achieve their competitive advantage by constantly reviewing their sales data to ensure that the items are stored close to the shipping area are still the most frequently picked.” – Martin Murray, Supply Chain/Logistics Expert, Warehouse Best Practices , About.com
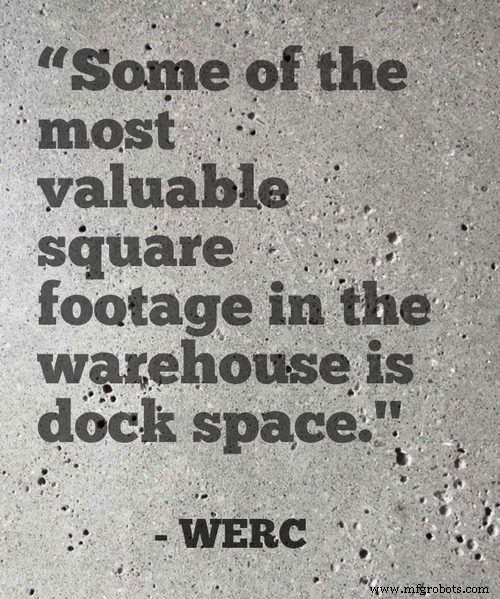
35. Implement efficient dock management practices. “Some of the most valuable square footage in the warehouse is dock space. All material must flow in and out of your docks, and these are limited in number (and not readily added to). Space on the inside and outside of the docks is some of the busiest in your warehouse. Dock best practice depends on the type of inbound you receive and for many companies balancing available dock doors, equipment, and labor is difficult, so the receiving dock becomes a choke point in the supply chain. Docks in today’s warehouses must be more flexible and must support a variety of receipts that are coming in at a faster rate and in greater frequency and with just in-time and VMI programs, smaller quantities and mixed pallets.” – Warehousing &Fulfillment Process Benchmark &Best Practice Guide , Warehouse Education and Research Council (WERC); Twitter:@WERC
36. Calculate resource and space requirements based on expected receipts and current backloads. “Put-away is the process of moving material from the dock and transporting it to a warehouse’s storage, replenishment, or pick area. Best-practice companies manage the put-away area by calculating resource and space requirements based on expected receipts and current backlogs. Best practice is to put away product the same day it’s received, because not doing so affects space, causes congestion, increases transaction errors, and makes product more susceptible to damage. In a busy warehouse, it is easy to let product put-away fall behind other tasks such as picking, replenishment, shipping, and loading. But pulling away resources from put-away tasks can affect fill rates by not having product in pick racks. This can bring about congestion in staging areas that overflow into aisles. Delaying put-away may also result in product damage as the merchandise is moved, again and again, to make way for higher priority receipts. Proper staffing of the put-away team will support down stream processes of picking and shipping, and in the long run lead to better customer order fill rates.” – Kate Vitasek, Best Practices in Material Handling and Put-away , Multi-Channel Merchant; Twitter:@mcmerchant
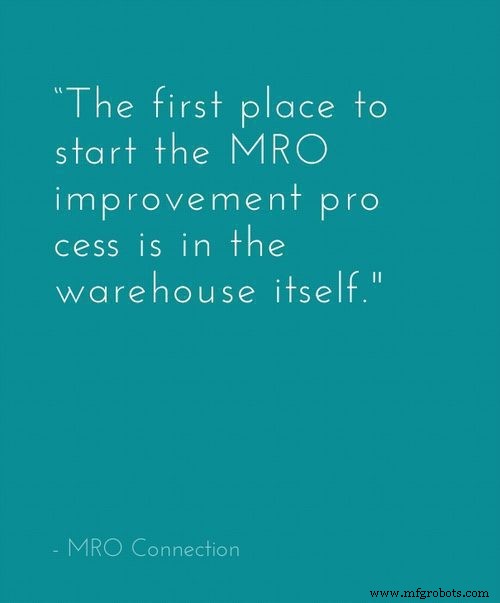
37. Establish stable warehouse operations within the warehouse first, then work to improve pre-planning efforts. “The first place to start the MRO improvement process is in the warehouse itself. Once stable warehouse operations have been established, maintenance and operations can work to improve their pre-planning efforts. At first glance, this appears to be a daunting task. Trying to organize, store, identify and properly manage thousands of disparate inventory items, with different and seemingly unpredictable demand patterns, creates an environment in which it is difficult to succeed. Creating an implementation strategy that is simple, straight forward and thorough, is critical to a successful MRO Warehouse Operation.” – Creating the “Perfect Warehouse,” MRO Connection
38. Maximize vertical space. “On the production floor, where space can be limited, it’s important to take advantage of every inch of available space (floor to ceiling). As noted in an Occupational Health &Safety article, solutions such as pallet racking can lead to safer working conditions as well as increased efficiency in the warehouse. Pallet racking, the most common way of storing pallet loads in the world, is an easy-to-use storage solution; it’s used in the vast majority of warehouses, manufacturing facilities, commercial warehouse operations, and even retail stores.” – Jennie Dannecker, 10 Ideas for More Efficient &Productive Warehouse Operations , Cerasis; Twitter:@Cerasis
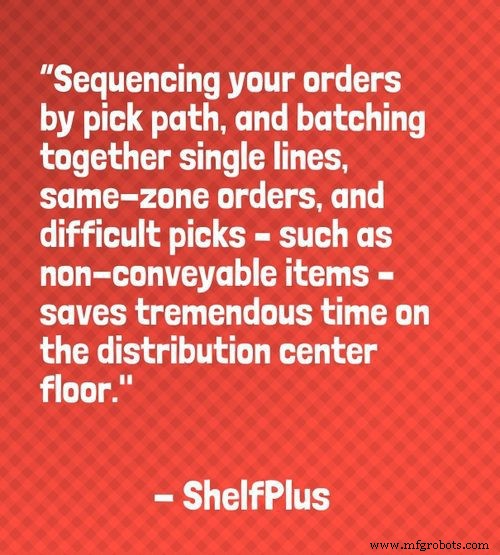
39. Use your WMS software to sequence orders and organize the workflow. “Sequencing your orders by pick path, and batching together single lines, same-zone orders, and difficult picks – such as non-conveyable items – saves tremendous time on the distribution center floor. Again, your WMS software should be able to organize the workflow and optimize sequence performance.” – 10 Ideas for a More Efficient Warehouse Operation , ShelfPlus
40. Communicate effectively — and often. “Clearly communicating to workers your organizational goals and the processes to achieve them is one key to effective warehousing operations. When managers fail to create an environment of open and clear communication, employee productivity suffers, resulting in high turnover and wasted resources.” – Increasing Warehouse Productivity , Inbound Logistics; Twitter:@ILmagazine
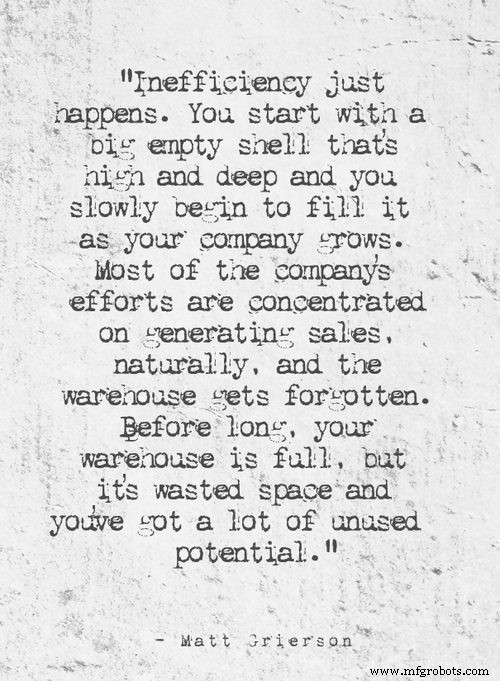
41. Make smart use of floor space. “Matt Grierson is managing director at Dexion, which provides industrial and commercial storage solutions across Europe. He says that only a small fraction of the companies that approach him believing they need to move into larger premises really do need to. The rest have enough space already, they’re just using it badly.
“Grierson says:‘Inefficiency just happens. You start with a big empty shell that’s high and deep and you slowly begin to fill it as your company grows. Most of the company’s efforts are concentrated on generating sales, naturally, and the warehouse gets forgotten. Before long, your warehouse is full, but it’s wasted space and you’ve got a lot of unused potential.’
“By using your space efficiently, your staff can get jobs done quicker and can complete more jobs in a day, you save on purchase or rent by not expanding unnecessarily, and you can go longer before the huge burden of relocating into bigger premises.
“Grierson adds:‘There are a lot of shelving options. Two-tier or mezzanine, fixed or mobile. If you can squeeze your rows of shelving together, and only open them up when access is required, you can save 50% of your floor space.'” – Tim Aldred, How to manage an effective warehouse , The Guardian; Twitter:@tim_aldred
42. Design storage systems to meet the needs of the current and planned mix of storage types. “The layout of a warehouse that supports an adjoining manufacturing facility will have different requirements than a facility supporting product distribution to stores or a facility that supports end-user fulfillment. Some operations place emphasis on replenishment of product to the point of use, others on product picking or order fulfillment.
“Regardless of the ultimate mission of the warehouse, best-practice companies have designed storage systems to meet the needs of the current and planned mix of storage types. They have optimized storage locations and layouts to fit product without the need to restack or repalletize it once received. The warehouse management system will track storage location profiles and properly assign product to the best storage location. As a result, best-practice companies have excellent cube-fill rates.
“In addition to optimizing the cubic fill of storage locations, best practice is to minimize travel time. If a product is in high demand it should be placed closer to its next point of use. In this case demand should be based on the number times the product is required, not on the number of units required. The difficulty of retrieval should also be considered in travel time. Higher-demand product should be placed on the most easily accessed storage space, typically floor level for racking and between waist and shoulder level in pick racks.” – Kate Vitasek, Storage and Inventory Control Best Practices , Multi-Channel Merchant; Twitter:@mcmerchant
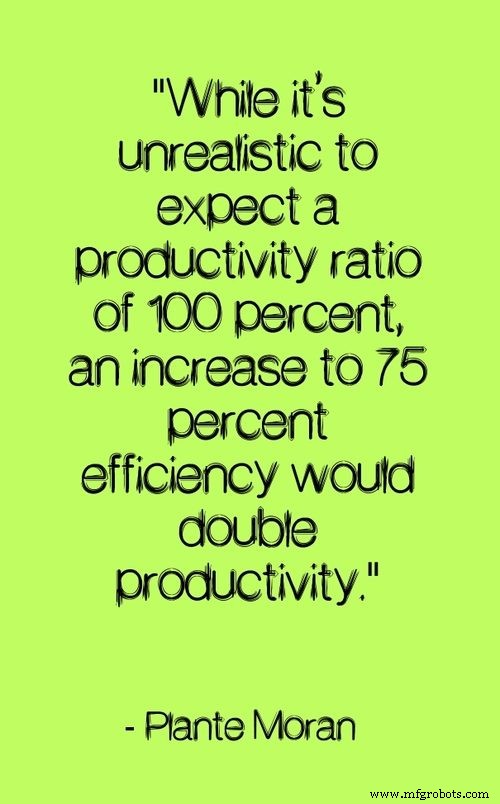
43. Reduce order processing cycle time. “In one analysis of a distribution operation, data revealed that the overall order processing cycle time was extremely inefficient. Of the total order cycle time, it was actually being worked on only 37.9 percent of the time. Six percent of the time was wasted while people dealt with problems such as waiting for lift equipment, computer issues, interruptions, and blocked aisles, and the remaining 56.1 percent of the time orders sat idle. This is a low productivity ratio by any standard. While it’s unrealistic to expect a productivity ratio of 100 percent, an increase to 75 percent efficiency would double productivity. How can this opportunity be captured? ” – Are Your Warehouse Operations Lean? , Plante Moran; Twitter:@PlanteMoran
44. Implement and maintain operational standards in all functional areas. “Maintain and use standards in all major functional areas. This will assist management in identifying systemic bottlenecks such as aisle congestion or other workflow problems.” – Warehouse Workflow Handbook , WERC; Twitter:@WERC
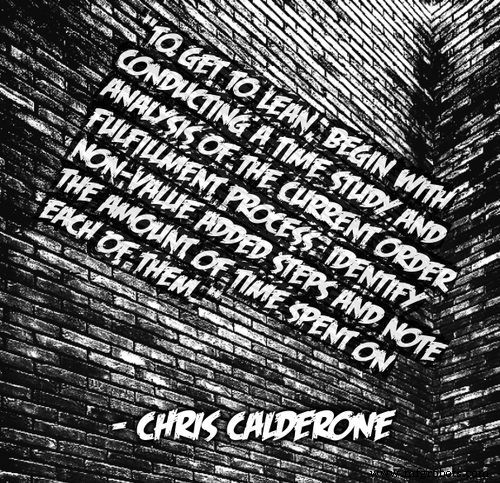
45. Improve cycle time utilization through lean applications. “Lean applications can help improve cycle time utilization, reduce costs, increase productivity, and increase customer satisfaction. To get to lean, begin with conducting a time study and analysis of the current order fulfillment process. Identify non-value added steps and note the amount of time spent on each of them. Then, assess overall workflow in an attempt to reveal inefficient product pick paths, wasted motion, excessive delays, excessive footsteps, aisle and work area congestion, and equipment availability.” – Chris Calderone, Creating a Lean HME Warehouse Operation , Lean Homecare; Twitter:@LeanHomecare
Best Practices for Improving Inventory Management
46. Reduce inventory inefficiencies. “Warehouse management systems are critical to tracking the various stages of the manufacturing process. From production to delivery, officials need to be able to monitor inventory as it makes its way through the supply chain. This is especially relevant during periods of growth, as a sudden influx of inventory may overwhelm employees on the floor, leading to costly errors. Without a robust inventory control system, managers may have difficulties locating materials or finished products, causing them to dedicate more manpower and resources to this process. Officials with Land Rover dealt with this issue on a regular basis, according to Zebra Technologies. When vehicles rolled off the assembly line, they were subject to a number of finalization processes, including testing, setting configurations and addressing any existing errors. Managers had a great deal of difficulty identifying where individual items were located along the supply chain, resulting in a high degree of uncertainty and risk.” – Nancy Master, Identifying Warehouse Management Best Practices , RFgen; Twitter:@RFgenSoftware
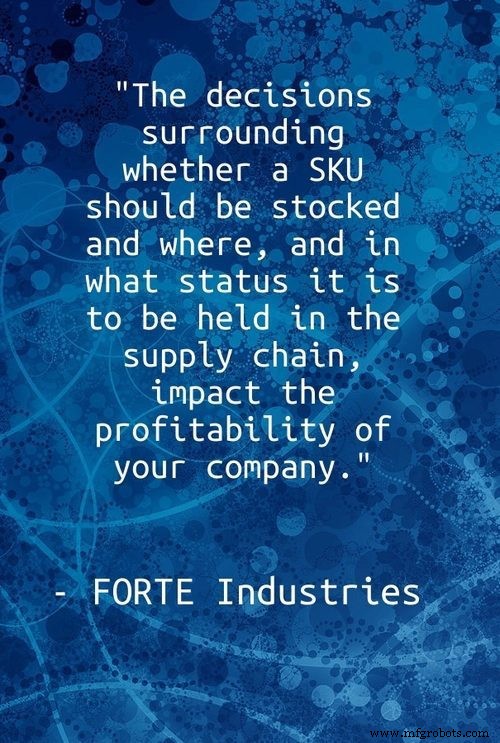
47. SKU profiling can facilitate profitability. “Understanding how every SKU carried in your distribution center (DC) can – and should – contribute to your company’s bottom line – is the best way to design and run DC operations. Here’s why:Each SKU has a potential cost impact that goes well beyond its actual purchase price. The decisions surrounding whether a SKU should be stocked and where, and in what status it is to be held in the supply chain, impact the profitability of your company. And from a selfish standpoint, these same decisions, made without sufficient evaluation, can rob your distribution center of capacity and efficiency.” FORTE Industries
48. Establish minimum holding stocks to cover lead times. “It has been established that the role of inventory management is to ensure that stock is available to meet the needs of the beneficiaries as and when required.
“Inventory represents a large cost to the humanitarian supply chain. This is made up of the cost of the inventory itself, plus the cost of transporting the goods, cost of managing the goods (labor, fumigation, repackaging, etc) and keeping the goods in warehouses. The inventory manager’s job is to make inventory available at the lowest possible cost.
“In order to achieve this, the inventory manager must ensure a balance between supply and demand by establishing minimum holding stocks to cover lead-times. To achieve this, the inventory manager must constantly liaise with the programs to keep abreast of changing needs and priorities. The warehouse must always have sufficient stocks to cover the lead-time for replacement stocks to avoid stock-outs.” – Warehousing and Inventory Management , Logistics Cluster; Twitter:@logcluster
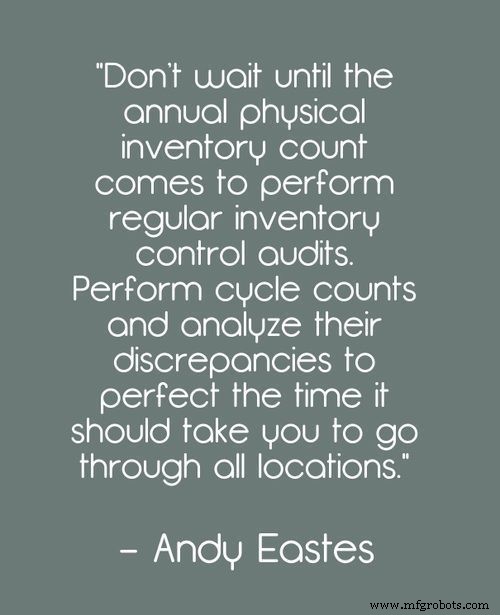
49. Perform cycle counts and analyze discrepancies. “Don’t wait until the annual physical inventory count comes to perform regular inventory control audits. Perform cycle counts and analyze their discrepancies to perfect the time it should take you to go through all locations. It’s good to have cycle counts go through all locations every quarter so that you have a more accurate back-office system.” – Andy Eastes, CEO of Agile Harbor, 10 Ways to improve warehouse efficiency and inventory management without software , SKUVault; Twitter:@skuvault
50. Develop an approved stock list for each location. “When you stock an item you are making a commitment—a commitment that the product will be available in reasonable quantities for immediate shipment or delivery to customers. Most distributors’ warehouses are filled with two things:‘stock’ and ‘stuff.’ Stock is the material you intend to be in the warehouse. That is, the items necessary to meet or exceed customers’ expectations of product availability. Stuff is everything else. You must separate the stock from the stuff in each of your warehouses. Our goal is to liquidate the stuff and arrange the stock items in such a way to minimize the cost of filling customer orders.” – John Schreibfeder, President of Effective Inventory Management, Inc., The First Step to Achieving Effective Inventory Control , via Lanham Associates; Twitter:@LanhamAssoc
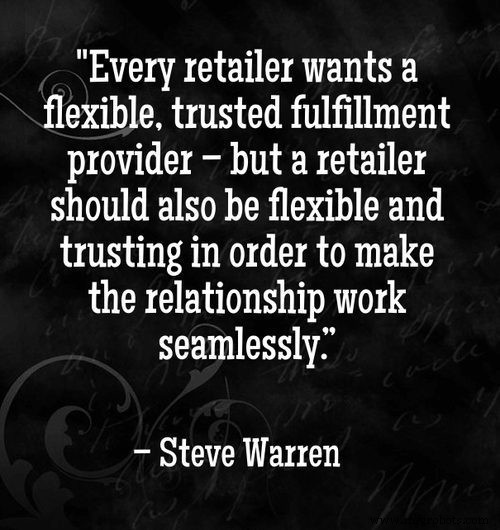
51. Maintain constant, consistent communication with vendors. “A good relationship with your vendors is crucial to your company’s success – especially if you outsource any part of your retail operations. Your fulfillment provider becomes your brand in the eyes of the customer, so it’s important that they understand your plans for your inventory as well as you do.
“This means constant communication of your promotional plans, product information, and upcoming releases. Every retailer wants a flexible, trusted fulfillment provider – but a retailer should also be flexible and trusting in order to make the relationship work seamlessly.” – Steve Warren, 4 Tips for Effective Inventory Management , Multi-Channel Merchant; Twitter:@mcmerchant
52. Achieve inventory analysis efficiency. “With solid inventory analysis, you can ensure that you are investing in the right amount of the right products to remain competitive. By developing and using a comprehensive set of tools to closely monitor the performance of your inventory, you can achieve more of your goals more efficiently.” – Bill Knapp, Socius, Beyond Software:6 Effective Inventory Management Practices , featured on the ERP Software Blog; Twitter:@erpsoftwareblog and @mssocius
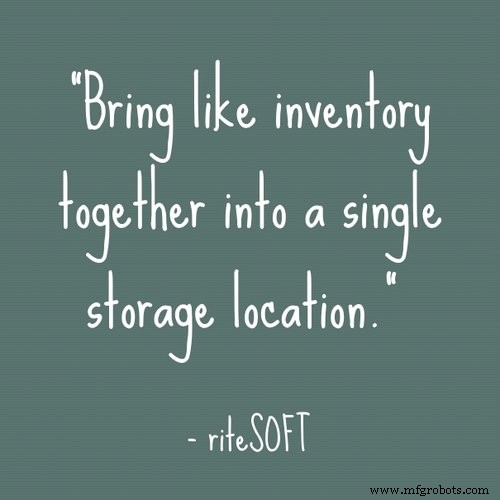
53. Understand the warning signals. “The easiest way to identify that you have too much—or the wrong inventory—is the amount of dust settled on the product in storage. If you see more than ½ inch of dust, then that’s likely a sign of obsolete inventory. However, there are other, more specific indicators that inventory management issues need to be addressed.
“If there are significant discrepancies between the book inventory and physical inventory, this is a direct indicator that there is a problem with inventory management. Another distinct indicator is when your warehouse staff is having trouble locating inventory on a timely basis—an issue that’s particularly critical when FIFO, batch/lot number or serial number controls are involved.
“The issue of locating specific inventory is typically tied to inventory discrepancies. And, of course, if you’ve seen a trend in the increased use of outside storage space, then this can indicate another ongoing inventory management issue.” – Norm Saenz and Don Derewecki of St. Onge, Inventory Management 101:Time to revisit the principles , Logistics Management; Twitter:@LogisticsMgmt
54. Use both fixed and moveable tracking options. “When companies think of warehouse tracking, they think primarily of movable tracking options, tracking the units and pallets that actually get moved around the warehouse and sent up the supply chain. This is only one part of the warehouse management process – do not forget the benefits that come with used fixed trackers, too! By tracking fixed warehouse assets, you are able to assign and manage destinations much more easily, and arrange strategy protocols as needed without mass confusion. It is better to think of warehouse tracking in two different parts, one fixed and one movable.” – Justin Velthoen, 7 Tips for Warehouse Inventory Management , QStock Inventory; Twitter:@QStockInventory
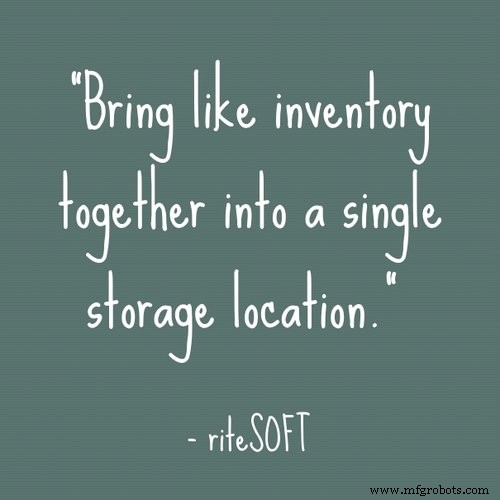
55. For physical count inventory, keep like inventory together in a single location. “Bring like inventory together into a single storage location. The same part shouldn’t be in several storage areas unless physical size dictates a limitation. In that case, keep available quantities to a minimum and move remainder to a location that isn’t part of the easily accessible storage (overstock location).” – Warehouse Management Tips for Physical Count Inventory , riteSOFT; Twitter:@ritesoft
Asset Tracking Solutions from Camcode:
- Inventory Control
- Inventory Management
- Custom Foil Labels
- Warehouse Signs
- Aisle Signs
- Stainless Steel Tags
- Floor Labels
- Security Labels
- Magnetic Labels
- Asset Tags