제약 식물 신뢰성 사례 연구
유지보수 및 신뢰성 전문가는 변화를 만들 수 있습니다. 대부분의 제조 공장에서 이는 작업에서 더 많은 완제품(청량 음료, 오토바이, 전구, 자동차, 컵케이크, 온수기 등)을 생산할 수 있도록 집중 작업을 의미합니다.
인디애나폴리스에 있는 Eli Lilly의 생합성 인간 인슐린(BHI) 공장에서는 차이를 만드는 것이 더욱 중요합니다.
Eli Lilly BHI 공장의 신뢰성 엔지니어링 그룹에는 (왼쪽부터) 선임 신뢰성 엔지니어 Vadim Redchanskiy, 신뢰성 엔지니어링 기술자 Mary Ann Dust, 유지보수 및 신뢰성 팀 리더 Ken Swank, 선임 신뢰성 엔지니어 Mark Lafever
미국에서 거의 2,100만 명, 전 세계적으로 2억 명이 당뇨병을 앓고 있습니다. 미국에서만 매년 거의 100만 건의 새로운 사례가 진단됩니다. 당뇨병이 있는 많은 사람들은 혈당(포도당)을 조절하기 위해 인슐린이 필요하며 BHI 식물은 이러한 필요를 채우는 데 도움이 됩니다. 1992년에 생산을 위해 개장한 이 공장은 전 세계 의약용 인슐린의 상당 부분을 생산합니다. 생산성을 높이는 유지보수 및 신뢰성 작업을 통해 회사는 고품질의 생명 유지 의약품을 필요한 사람들에게 제공할 수 있습니다.
Eli Lilly는 80년 이상 약용 인슐린을 생산해 왔습니다.
컴퓨터 칩을 만드는 회사에서 일하든 감자 칩을 만드는 회사에서 일하든 이해 관계자나 경제에 가치를 더할 때 어떤 식으로든 경시할 수 없습니다.”라고 공장의 유지 관리 및 신뢰성 팀 리더인 Ken Swank가 말했습니다. “당신이 무엇을 하든 상관없어요. 중요합니다. 그러나 한 가지 뚜렷한 차이점이 있습니다. 저는 산업용 코팅 회사에서 일했습니다. 우리의 코팅은 골프공에서 우주 왕복선, 수술 기구에 이르기까지 모든 것에 사용되었습니다. 최종 제품을 봤을 때 내가 그 일부라는 것을 알았습니다. 하지만 제약 회사에서 일할 때 . . . 그것은 개인적인 차원에서 많은 것을 의미합니다.
나는 주말에 어린 아들이 있는 부부를 만났습니다. 우리는 이야기를 나누었고 나는 그 소년이 당뇨병에 걸렸다는 것을 알게 되었습니다. 나는 1형인지 2형인지 물었다. 아버지는 당뇨병에 대해 어떻게 그렇게 많이 아느냐고 물었다. 그 소년은 그가 1형이라고 말했다. 나는 그를 바라보며 '내가 무엇을 하고 생계를 유지하는지 알아? 나는 인슐린을 만든다. 일라이릴리에서 휴물린을 만들고 있다”고 말했다. 그는 “고맙다. 나는 내 약을 정말 좋아한다. 기분이 훨씬 좋아집니다.'
“저희 부서는 이 건물이 매번 만들어야 하는 약을 만들고 있는지 확인하는 일을 담당하고 있습니다. 매일 수백만 명의 사람들이 의존하고 있습니다.”
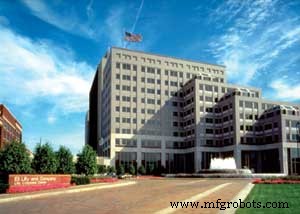
회사의 인디애나폴리스 캠퍼스에는
제조 현장과 기업 사무실이 있습니다.강한>
수요 증가
BHI 공장은 규모가 크고 기술적으로 복잡합니다. 여기에는 17,000개 이상의 장비, 13,000개의 입력/출력 지점 및 600개의 작동 장치가 있습니다. BHI 분자를 생성하는 처리 방법에는 여러 원심분리 단계, 소수의 반응, 많은 정제 단계 및 다양한 용매 교환 단계가 포함됩니다. 결과적으로 운영 단위의 약 1/3이 고위험 또는 안전이 중요한 작업으로 분류됩니다.
몇 년 전 유지보수 및 신뢰성 리더는 부서의 시간, 기술, 자원 및 플랜트에 대한 잠재적 영향을 최대화하기 위해 상당한 변경을 시행할 필요가 있다고 결정했습니다. BHI는 원래 설계 용량의 두 배 이상으로 운영되고 있었고 비즈니스 수요는 계속 증가했습니다. 기술자들은 너무 많은 노력을 기울였고, 수정 노력은 그 순간의 요구 사항을 해결하기 위해 자주 다시 우선 순위가 지정되었으며 중요한 시스템은 상당한 관심을 받지 못했습니다.
Eli Lilly는 전 세계 인슐린 공급량의 25%를 생산합니다.
우리는 적격 상태에서 작동하는 장비에 대해 걱정한 적이 없습니다.”라고 Swank는 말합니다. "하지만 그 당시 다른 제약 산업과 마찬가지로 우리는 장비에 특별히 중점을 두지 않았습니다. 다만 우리는 항상 최고의 약을 만들기 위해 최대한의 가동 시간을 원했습니다. 그러나 가능한 한 많은 킬로그램을 외부로 내보내는 것을 보면 '시설을 계속 추가하고 있습니까, 아니면 비즈니스 관점에서 현명하게 수행하고 신뢰성에 중점을 두는 것입니까?'라는 질문에 이르렀습니다.”
그것은 1990년대 후반에 많은 Eli Lilly 시설이 숙고했던 것입니다. 예를 들어, BHI 엔지니어링 관리자인 Ron Reimer는 회사의 Clinton(Ind.) Laboratories 사이트에서 사전 작업 및 가동 시간을 늘리고 유지 관리 비용을 줄이기 위한 노력을 주도했습니다. 프로액티브 자산 관리(Proactive Asset Management)로 명명되고 체계화된 해당 프로젝트의 일환으로 그는 회사의 첫 번째 안정성 엔지니어를 고용했습니다.
공장 신뢰성에 대한 모든 주요 이해 관계자의 직접 참여
(생산, HSE, 품질 관리, 재무, 엔지니어링 및
관리)는 안정성 우선 순위 지정 이니셔티브의 성공을 보장합니다. BHI의 개선 노력은 1999년에 신뢰성 엔지니어를 추가하고 RCM(Reliability-Centered Maintenance) 및 RCFA(Root Cause Fault Analysis) 프로젝트를 도입하면서 시작되었습니다. 이러한 노력은 식품의약국과 환경보호청과 같은 규제 기관이 제약 산업의 유지 관리를 면밀히 조사하기 시작하면서 더욱 커졌습니다. 기관의 메시지는 간단합니다. 유지 보수는 플랜트 신뢰성과 동일합니다. 플랜트 신뢰성은 제품 신뢰성과 동일합니다. 전반적인 신뢰성은 규정 준수와 동일합니다. "신뢰할 수 없는" 회사는 운영 중단을 포함한 처벌을 받을 수 있습니다.
커뮤니케이션의 중요성
유지보수 및 신뢰성 팀 리더인 Ken Swank에 따르면 BHI 공장의 신뢰성 우선순위 지정 이니셔티브의 성공에 커뮤니케이션이 중요한 역할을 한다고 합니다.
"커뮤니케이션은 제 직업에서 가장 중요한 부분 중 하나입니다."라고 그는 말합니다. “저는 프로덕션 리더와 자주 만나 앞으로 어떤 일이 일어날지 설명합니다. 나는 그들의 약속을 이해하고 그것이 추가하는 가치를 이해하도록 돕습니다. 그들은 또한 약간의 자원을 모아야 합니다. 적절한 분석은 분명히 우리 부서만이 아닙니다. 여기에는 엔지니어링, 유지 관리, 신뢰성, 운영, 기술 서비스, 자동화가 포함됩니다. 우리는 그들이 가치를 이해하는지 확인하기 위해 많은 시간을 할애합니다.
나는 그들이 이해하도록 돕기 위해 상당한 양의 춤과 노래를 해야 합니다. 그러나 모든 계정에서 바이인이 잘 되었습니다."
"그때부터 신뢰성이 오늘날 초점을 맞추기 시작했다고 생각합니다."라고 Swank는 말합니다. "진정으로 신뢰할 수 있는 공장이 되기 위한 여정에서 비전은 생산이 장비는 자격을 갖춘 상태이며 필요할 때 사용할 수 있으며 미리 결정된 성능 수준에서 실행될 것입니다. 우리는 분명히 그 부분에서 큰 역할을 합니다. 우리가 조합한 유지 관리 전략은 해당 장비를 또한 유지 관리 전략의 깊이는 필요한 활용도 또는 가동 시간을 다룹니다. 시설에 다른 작업보다 더 많이 실행되고, 다른 작업보다 중복성이 적거나, 다른 작업보다 더 필수적인 작업이 있습니다. 이러한 작업에는 더 많은 주의와 더 자세한 조사가 필요합니다. .”
2004년 초에 시작된 우선 순위 지정 이니셔티브는 가장 주의를 기울여야 하는 운영 단위에 가동 시간과 안정성을 제공하기 위한 이 전략의 핵심이었습니다.
Eli Lilly가 신뢰성 역할을 정의하는 방법
Eli Lilly BHI 유지보수 및 신뢰성 리더에 따르면 신뢰성 엔지니어의 직무 및 책임은 다음과 같습니다.
<올>
RCFA, FMEA, RCM 분석, 납 편차 조사 등을 통해 장비 고장 최소화
신뢰성 노력과 자원을 최적화하기 위한 지표를 개발합니다.
신규 및 기존 장비에 대한 자체 유지 관리 계획(검토/생성/승인).
흐름 전반에 영향을 미치는 안정성 중심 프로젝트를 제공합니다.
장비 가용성을 높이기 위해 유지 관리 및 안정성에 대한 비즈니스 관행에 중점을 둡니다.
멘토 신뢰성 기술자.
통제실 팀과 통합하여 비즈니스를 효과적으로 지원하십시오.
장비 성능과 가용성을 향상시키기 위한 새로운 기술을 찾고 구현합니다.
신뢰성 기술자의 직무 및 책임은 다음과 같습니다.
<올>
사이트 이니셔티브를 지원합니다.
CMMS 데이터 입력 양식을 작성하고 처리합니다.
RCFA, 데이터 마이닝, FMEA, RCM, 편차, 변경 제어, 현장 검증, CMMS 데이터 개선 등을 통해 신뢰성 엔지니어를 지원합니다. 글꼴>
특별 프로젝트 – 신뢰성 노력 지원 등
최우선 과제
Swank는 결국 신뢰성 개선으로 이어질 행군 명령에 대해 이야기합니다.
“당시 내 상사는 '우리가 BHI 시설을 더 안정적으로 만들 방법을 생각해보십시오. 이 문제를 해결해야 합니다.'”라고 Swank는 말합니다. “그가 정말로 말하고자 했던 것은 '당신과 당신의 팀은 시설의 비즈니스 요구를 이해하고, 올바르게 우선 순위가 지정된 안정성 격차를 해결하기 위한 경로를 설정하는 방법을 결정하고, 비즈니스에 판매하고, 실행하고, 지속 가능합니다.”
충분히 쉽게 들리거나 그렇게 생각했습니다.
"우리는 2004년 2월에 시작했고 3월이나 4월에 끝날 것이라고 생각했습니다."라고 그는 말합니다. “우리는 이것이 우리가 예상했던 것보다 더 복잡하고 복잡하다는 것을 빨리 깨달았습니다. 게다가 우리는 제대로 하고 싶었습니다.”
게임 계획은 기존 데이터를 사용하여 부서의 일상적인 지원 노력 외에 지속적인 개선 노력으로 시스템 개선의 우선 순위를 지정하는 분석을 개발하는 것입니다. 분석 요구 사항은 다음과 같습니다.
<울>
식별된 시스템을 사용하여 데이터를 기반으로 비즈니스 영향에 따라 순위를 매깁니다.
모든 이해 관계자가 대표됩니다.
1주(40시간) 이내에 분석을 실행할 수 있습니다.
이 과제는 해당 부서의 신뢰성 엔지니어링 부분에 맡겨졌습니다. 이 그룹에는 수석 신뢰성 엔지니어 Mark Lafever, Vadim Redchanskiy 및 Rod Matasovsky(현재 은퇴)와 신뢰성 엔지니어링 기술자 David Doyle, Mary Ann Dust 및 Matt O'Dell이 포함되어 있습니다. 그들은 분석 내용을 전략화하기 시작했습니다.
“그들은 똑똑한 사람들입니다. 저는 경영진에서 현장에 있는 직원들까지의 번역가였습니다.”라고 Swank는 말합니다. "그들은 데이터 시스템을 이해하고 무엇이 타당하고 무엇이 그렇지 않은지를 이해했습니다."
이 그룹은 이 이니셔티브에 대한 지원을 얻으려면 분석이 사실을 기반으로 해야 하며 공장 신뢰성 – 생산; 건강, 안전 및 환경(HSE); 품질 관리(QC); 재원; 공학; 및 관리. 이것은 놀라운 균형 잡힌 행동이 될 것이었습니다.
"누구나 나가서 많은 데이터를 가져올 수 있습니다."라고 Lafever는 말합니다. "데이터를 가져올 위치, 가져오는 방법을 결정하고 올바른 결정을 내리는 데 필요한 정보를 데이터가 알려줄지 여부를 파악해야 했습니다."
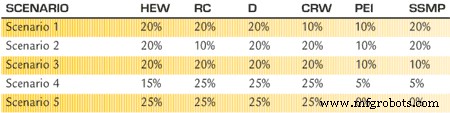
표 1. 5가지 시나리오에 대한 가중치 요약
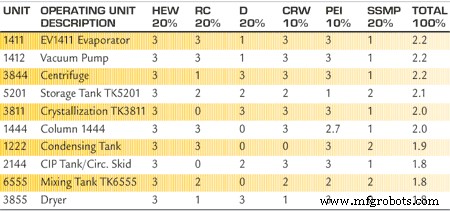
표 2. 첫 번째 시나리오 민감도 분석의 예
Lafever는 몇 번의 반복과 "많은 고민" 끝에 지난 12개월 동안의 기존 데이터를 사용하여 이해 관계자를 고려한 분석을 완료했습니다. 이 데이터에는 다음이 포함됩니다.
1) 생산을 만족시키기 위한 장비 가동 중지 시간과 동일한 긴급 작업 시간. 이것은 각 운영 단위에 부과된 모든 시간을 추적하는 공장의 전산화된 유지 관리 시스템에서 수집되었습니다. 비상근무는 '기다릴 수 없는 일'로 정의했다. 시스템 가동 중지 시간에 대한 전통적인 측정은 아니지만, 이는 시스템이 제대로 작동하지 않을 때 느끼는 중단 생산의 양과 직접적인 관련이 있습니다.
2) HSE를 만족시키기 위한 Lilly의 GIPSM(Globally Integrated Process Safety Management)에 따른 위험 분류. 분류 시스템에는 4가지 가능성이 있습니다. 상당한 환경, 건강 및 화재 위험을 수반하는 고위험; 산업 안전 보건국에서 정의한 기계적 무결성; 위험이 없거나 "위에 해당하지 않음"
3) QC를 만족하지 못하는 장비 고장으로 인한 공정 편차의 수. 이는 작업자 오류나 기타 비장비 문제가 아니라 장비 신뢰성 문제의 결과인 편차를 표적으로 삼았습니다. 제품 품질에 대한 편차의 영향을 정확히 지적한 수준(1, 2 또는 3)과 함께 편차 수를 고려했습니다.
4) 재정을 만족시키기 위한 사후적 작업의 비용. 이것은 운영 단위에 대한 모든 예산 비용을 추적하는 CMMS에서 다시 가져왔습니다. 이 비용에는 시스템에서 수행된 사후 대응 작업과 관련된 모든 부품 및 인건비가 포함되었습니다.
5) Process Engineer 엔지니어링을 만족시키기 위한 입력. 각 시스템을 담당하는 프로세스 엔지니어는 시스템 수명, 시스템 장애로 인한 잠재적 가동 중지 시간 및 규제 영향과 같은 주제에 대해 설문 조사를 받았습니다.
6) 엔지니어링을 만족시키기 위한 시스템 유지 관리 계획의 상태. 이것은 네 가지 수준을 포함하도록 제작되었습니다. 수준 1, 일상적인 유지 관리가 수행되지 않음, 가장 심각한 것으로 간주됨 레벨 2, 시스템에 예방적 유지보수가 존재합니다. 레벨 3, 시스템이 일정한 자격 상태에 있고 사용하기에 적합한지 확인하기 위해 고안된 정기 자격 평가(PQE)가 실행됩니다. 그리고 레벨 4, RCM 기반 분석이 시스템에서 사용되어 유지 관리 계획을 생성했습니다.
이 데이터는 420개의 운영 단위를 살펴보고 생산을 중단하거나 OSHA 또는 EPA 보고 대상 사고를 일으킬 가능성이 있는 운영 단위를 식별하는 "중요 장비" 평가를 생성했습니다.
Lafever는 "CMMS에서 구조를 설정하는 방식과 사고 데이터베이스를 제어하는 방식, 운영 단위가 가장 좋은 방법이었습니다."라고 말합니다. “때때로 작동 장치는 하나의 장비입니다. 대부분의 경우 장비의 주요 부분이자 훨씬 더 많은 부분입니다."
예를 들어, Redchanskiy는 작동 장치 EV1411(증발 공정)에 "밸브, 열교환기 및 펌프와 같은 장비 및 기기 50~60개"가 포함되어 있다고 말합니다.
평가 결과 초기 목록이 420개에서 135개로 70% 감소했습니다.
사실은 거짓말을 하지 않습니다
특정 운영 단위의 중요성을 결정할 때 사실에 대해 논하기는 어렵습니다.
“이 분석을 수행하기 전에 생산에 대해 언급한 것은 원심 분리기뿐이었습니다. 프런트 엔드”라고 Eli Lilly 유지 관리 및 안정성 팀 리더인 Ken Swank는 말합니다. “분석하고 우리가 생각해 낸 것을 보여준 후 원심분리기가 63위(135개 작동 장치 목록에서)임을 지적했습니다. 그들은 그것에 대해 별로 묻지 않습니다.
“이는 또한 생산 장비의 정의를 벗어나게 합니다. 분석 전에 사람들은 폐기물 탱크, 공기 처리기 등을 포함하는 것을 잊었습니다. 그들은 모든 바닥 배수구가 가는 제어실 2의 탱크 1099에 대해 생각하지 않았습니다. 플러시는 배수구를 통해 탱크로 들어갑니다. 탱크가 작동하지 않으면 정화 단계를 중단해야 합니다."
도량형
나머지 135개 단위의 적절한 우선 순위를 보장하기 위해 그룹은 각 데이터 소스에 가중치를 적용하기로 결정하고 소수의 민감도 분석을 수행했습니다.
스웽크는 "6가지 기준이 동등하게 가중치가 부여된다고 생각하지 않았다"고 말했다. "예를 들어 비상 유형의 작업에 지출하는 비용보다 안전과 품질이 더 큰 영향을 미친다고 느꼈습니다."
각 데이터 세트에 대해 점수 시스템(0에서 3까지, 0은 영향과 심각도가 가장 낮고 3은 가장 영향과 심각도가 높음)을 개발하여 각 운영 단위에 적용했습니다. 분석 결과는 다음과 같습니다.
긴급 근무 시간(HEW) :15시간 미만(0점), 15~25시간 미만(1), 25~40시간 미만(2), 40시간 이상(3)
위험 분류(RC) :HSE 위험 없음(0), 기계적 무결성 시스템(1), 고위험 프로세스(2) 및 안전이 중요한 작업(3).
편차(D) :편차의 정도와 수를 고려하여 4개의 그룹화를 하였다. 수준 2 편차는 수준 1 편차의 3배, 수준 3 편차는 수준 2 편차의 2배인 것으로 결정되었습니다. 이를 통해 수준 1 편차는 1점, 수준 2 편차는 3점, 수준 3 편차는 6점이 되었습니다. 이것은 모든 편차에 적용되었습니다. 그 결과 값은 2 이하(0), 2 초과 ~ 5(1), 5 초과 8(2), 8 초과(3)였습니다.
반응 작업 비용(CRW) :$5,000 미만(제로), $5,000 ~ $7,499 미만(1개), $7,500 ~ $14,999(2개) 및 $15,000 이상(3개).
프로세스 엔지니어 입력(PEI) :최소 영향 시스템(0) 및 최대 영향 시스템(3)까지 확대합니다.
시스템 유지 관리 계획(SSMP) 현황 :시스템에서 수행된 RCM 분석(0), 일상적인 PQE 실행(1), PM 수행(2) 및 일상적인 유지보수 수행 없음(3).
점수는 135개 운영 단위에 적용되었습니다. 그런 다음 정보를 스프레드시트에 로드하고 다양한 데이터 세트의 중요성을 강조하기 위해 다양한 가중치를 적용했습니다. 민감도 분석 프로젝트에는 단일 데이터 포인트가 시스템의 우선 순위를 결정하지 않도록 5가지 가중치 시나리오가 포함되었습니다.
시나리오는 상당히 균등한 가중치 분포(HEW, HSE, D 및 SSMP, 각각 20%; CRW 및 PEI, 각각 10%)에서 두 가지 범주(HEW, HSE, D 및 CRW, 각각 20%, PEI) 제거에 이르기까지 다양했습니다. 및 SSMP, 0%). 후자의 시나리오에서 나머지 데이터 세트는 시스템이 입증한 신뢰성 수준에 따라 변경된 "실제 데이터"였습니다. 시나리오는 표 1에 나와 있습니다.
민감도 분석의 각 시나리오는 위험 요소를 취해 특정 시나리오의 가중치를 곱했습니다. 각 범주의 제품은 각 운영 단위에 대해 합산되었습니다. 표 2는 첫 번째 시나리오의 예를 보여줍니다.
5가지 시나리오가 모두 완료되면 운영 단위에 대한 최종 점수를 그래프로 작성하고 신뢰성 팀에서 검토했습니다. 최종 순위 및 개선 계획을 결정하기 전에 추가 요소를 고려했습니다. 해당 장치가 최근에 교체되었거나 자본 계획에서 교체되었습니까? 이 장치에 대한 개선 계획을 다른 장치에 적용할 수 있습니까? 이 문제 해결을 위해 어떤 기능 그룹이 필요하며 사용할 수 있습니까? 과거에 어떤 개선 활동이 이루어졌습니까?
Swank는 "예를 들어, 원심분리기 중 하나가 목록의 맨 위에 있었지만 다른 사이트에서 매우 유사한 시스템에서 RCM을 수행하고 있다는 것을 알고 있었습니다."라고 말합니다. "우리는 노력을 복제할 필요가 없었습니다."
제안된 개선 활동의 최종 목록은 운영 단위에 따라 심층적인 RCM 분석에서 시스템을 전혀 개선하지 않는 것까지 다양했습니다.
그 시점에서 팀은 포괄적인 계획이 있다는 것을 알았습니다.
Lafever는 말합니다. “30번 정도 계획을 세웠고 '이 정도면 충분하지 않습니다.' '품질 관리팀은 이에 대해 어떻게 생각할까요?' '공정 엔지니어링은 이에 대해 어떻게 생각할까요?' 매우 당황했다. 우리는 모든 측면과 잠재적인 질문을 모두 해결했는지 확인해야 했습니다."
Swank는 다음과 같이 덧붙였습니다. “처음 찔렀을 때 '와, 이것도 가깝지 않군요'였습니다. 왜 이전에는 하지 않았는지 분명해졌습니다. 많은 작업입니다. 이런 식으로 계속해서 당신을 찢는 일상적인 것들도 있습니다. 하지만 우리는 그것을 고수하고 끝내겠다고 스스로에게 말했습니다.”
서면
2004년 9월 21일 Swank는 현장 책임자와 모든 기능 관리자를 포함하는 공장의 리드 팀에 우선 순위 모델을 공식적으로 발표했습니다. 7개월간의 고된 작업이 결실을 맺었습니다.
그는 “물물교환이나 토론이 왔다갔다 하지 않았다”고 말했다. "그들은 '대단하다. 진행하세요.'”
물론 고개를 끄덕이고 손을 흔드는 것은 여기까지만. 그래서 Swank는 Lafever에게 평가 프로세스를 요약하고 중요한 장비 분석이 매년 수행되는 방식을 자세히 설명하는 보고서를 만들도록 했습니다. 보고서는 향후 평가를 위한 템플릿 역할을 합니다.
Swank는 "나는 리드 팀 구성원들에게 서명하라고 말했습니다. "그들은했다. 서면으로 가지고 있습니다. 망설임이 없었다. 이는 우리가 수행한 분석이 정말 강력하다는 것을 보여줍니다.”
2005년 2월 28일, 주요 장비 분석이 공식화되고 리드 팀의 승인을 받았으며 플랜트의 가장 중요한 운영 단위에 대한 개선 활동이 플랜트의 2005년 및 2006년 사업 계획에 포함되었습니다.
템플릿은 후속 평가를 거의 매끄럽게 만들었습니다.
Lafever는 "작년에는 분석을 하는 것이 쉬웠습니다."라고 말합니다.
2006년 계획은 5월에 완료되었습니다.
구제 결과
이 Eli Lilly 공장의 유지보수 및 신뢰성 부서 리더는 현재 신뢰성 우선 순위 지정 이니셔티브의 수익, 달러 및 센트 효과를 수량화할 수 없다고 말합니다.
Lafever는 "불행한 부분은 해마다 작업 결과를 항상 확인하지 못한다는 것입니다."라고 말합니다. "시스템을 통해 작업하는 데 시간이 걸리기 때문에 1년 지연될 수 있습니다."
하지만 혜택과 결과가 없었던 것은 아닙니다.
Redchanskiy와 Doyle은 주어진 자산에 대해 유지 관리가 수행되는 방식을 재평가하는 것만으로도 불가피한 비용 절감이 가능하다고 말합니다.
Redchanskiy는 "분석에서 우리는 반응 작업이 전혀 없는 몇 가지 시스템에 상당한 금액을 지출하고 있음을 발견했습니다."라고 말합니다. “우리는 예방 유지 관리에 많은 돈을 썼습니다. 우리는 PM에 그것을 과장했습니다. 이러한 시스템의 유지 관리 방식을 변경했습니다.”
Doyle는 "이로부터 가장 큰 변화는 일부 시스템의 경우 사람들이 이제 실제로 실패해도 괜찮다고 말할 수 있다는 것입니다."라고 말합니다. “그게 특정 시스템에 대한 우리의 진단 및 계획이라면 괜찮습니다. 그것은 우리에게 완전히 다른 철학입니다.”
Swank는 공장의 생산성 수준에서 긍정적인 효과를 얻을 수 있다고 말합니다.
"재고 수준을 충족했다는 사실과 비즈니스 모델이 생산성 향상을 향해 나아가고 있다는 사실은 우리가 이미 첫 번째 주요 이정표에 도달했음을 보여줍니다."라고 그는 말합니다.
Lafever는 개선 프로젝트에 참여함으로써 기술 지식과 가동 시간이 증가했다고 믿습니다.
"대부분의 유지 관리 및 운영 인력이 RCM 분석에서 나오면 해당 시스템의 전문가로 분류될 수 있습니다."라고 그는 말합니다. “모두가 그룹의 개별 기능과 장비를 수리하거나 장비에 문제가 있을 때 식별하는 역할을 함께 수행하는 방법을 더 잘 이해하고 있습니다. 제 생각에는 그 상호작용 자체가 발생하는 긴급 작업의 양을 줄여줍니다.”
최고의 성공 지표는?
Doyle는 "그것은 우리 고위 경영진을 행복하게 만듭니다."라고 말합니다.
Swank는 "그게 저를 행복하게 합니다."라고 말합니다.
이러한 모든 개선 사항은 BHI가 2005년 의약품 제조상을 수상한 이유를 설명할 수 있습니다. 이 상을 "비즈니스 요구 사항을 가장 잘 충족하고 회사의 제조 방식을 구현하는" Eli Lilly 공장에 수여됩니다.
다른 Lilly 공장은 우선 순위 결정에 주목하고 채택 가능성을 검토하고 있습니다. 이를 통해 유지 관리 및 안정성에 대한 전사적 가시성이 향상되었습니다.
Reimer는 "좋은 부분은 유지 관리가 추가하는 가치에 대한 기업의 이해와 인식입니다."라고 말합니다. "이것은 우리가 확실히 활용하고 싶은 것입니다."
이 팀은 유지 관리 및 신뢰성 전문가가 변화를 만들 수 있고 실제로 할 수 있음을 매일 보여줍니다.