전기로 제강 기술 개발
전기로 제강 기술 개발
제강 기술의 개발은 여러 요구 사항을 충족하기 위해 발생합니다. 이러한 요구 사항은 아래와 같이 4가지 그룹으로 분류할 수 있습니다.
- 기술은 요구되는 품질의 다양한 강철 등급을 생산하는 데 필요한 공정 요구 사항을 충족해야 합니다.
- 생산된 철강 제품이 경쟁력을 가질 수 있도록 생산 원가를 제어하는 데 필요한 경제적 요구 사항을 충족시키는 기술입니다.
- 기술은 규제 기관에서 설정한 배출 수준을 충족하는 것입니다.
- 기술은 작업자가 위험, 스트레스 및 얼룩 없이 해당 지역에서 작업할 수 있도록 건강 및 안전 요구 사항을 충족하는 것입니다.
전기로(EAF)를 이해하기 위해서는 전기아크가 무엇인지 이해할 필요가 있다. 전기 아크는 작은 간격(일반적으로 일반 공기)으로 분리된 두 전극 사이의 방전 형태입니다. 이것의 가장 잘 알려진 예는 번개입니다. 아크 용접을 해본 사람이라면 전기 아크도 잘 알 것입니다. DC 전원의 음극에 공작물을 연결하고 양극에 전극을 연결하면 전극에 순간적으로 접촉하여 공작물에서 약간 떨어져 당기면 전극과 전극 사이에 안정적인 전기 아크가 형성됩니다. 이 아크의 열은 전극을 녹이고 공작물을 함께 용접하기에 충분합니다. 동일한 아이디어가 전기로에서 더 큰 규모로 사용됩니다.
전기로(EAF) 제강의 역사는 그리 오래되지 않았습니다. 전력을 이용하여 강철을 녹이는 최초의 용광로가 가동된 것은 불과 한 세기가 조금 넘습니다. 기술의 초기 개발은 이 장치를 통해 쉽게 최고 온도에 도달할 수 있었고 고품질 합금강 등급 및 합금 생산을 위한 최상의 조건을 보장했기 때문입니다. 그 이후로 용광로 장비, EAF 기술, 용해 방식, 원자재 및 철강 제품에서 큰 발전이 이루어졌습니다. EAF 기술의 발전으로 EAF는 제강의 BOF(Basic Oxygen Furnace) 기술을 사용하는 통합 공장과 보다 성공적으로 경쟁할 수 있었습니다. 오늘날 EAF 제강은 세계 철강 생산에 상당한 기여를 하고 있지만 BOF의 지배적인 제강 기술에 의한 철강 생산 기여도에는 여전히 한참 뒤떨어져 있습니다.
초기 개발
19세기에 철을 녹이기 위해 전기 아크를 사용하려는 여러 시도가 있었습니다. Humphry Davy 경은 1810년에 실험적 시연을 수행했으며, 1815년에는 Pepys가 용접을 조사했으며, Pinchon은 1853년에 전기로를 만들려고 시도했으며, 1878~79년에는 Carl Wilhelm Siemens가 아크 유형의 전기로에 대한 특허를 취득했습니다.
De Laval은 1892년에 철의 용융 및 정제를 위한 전기로에 대한 특허를 냈고 Paul Heroult는 1888년과 1892년 사이에 철 합금의 전기 아크 용융을 시연했습니다. 새로운 기술은 20세기 초에 널리 사용되기 시작했습니다. 상대적으로 저렴한 전기 에너지의 생성이 그 때 시작되었습니다. 1906년에는 미국 최초의 전기 아크 용해로가 Halcomb 공장에 설치되었습니다. 이 'Old No. 1' Heroult 전기 아크로는 현재 펜실베니아 주 피츠버그의 스테이션 스퀘어에 지정된 ASM(American Society for Materials) 역사적 기념물로 지정되어 있습니다(그림 1).
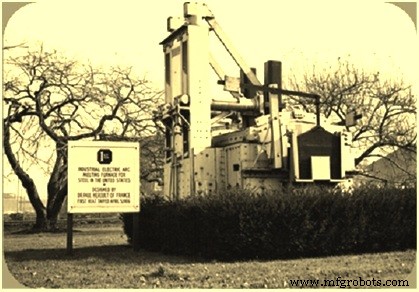
그림 1 최초의 Heroult 전기로
처음에 EAF 제강은 스크랩 및 철 합금과 같은 고체 형태의 사료를 사용하여 특수 등급의 강을 생산하기 위해 개발되었습니다. 고체 재료는 먼저 직접 아크 용융을 통해 용융되고 적절한 플럭스를 추가하여 정제되고 추가 처리를 위해 탭핑됩니다. 전기 아크로는 또한 탄화물 덩어리에 사용하기 위한 탄화칼슘을 준비하는 데 사용되었습니다. EAF 제강 기술은 이제 느린 공정에서 BOF의 생산성 수준에 근접하는 수준에서 수행되는 급속 용해 공정으로 발전했습니다.
Heroult 아크 정제로를 통한 개략적인 단면이 그림 2에 나와 있습니다. 이 그림에서 E는 전극(하나만 표시됨)이며 랙 및 피니언 드라이브 R 및 S에 의해 상승 및 하강됩니다. 내부는 내화 벽돌로 늘어서 있습니다. H, K는 하단 라이닝을 나타냅니다. A의 문을 통해 내부로 들어갈 수 있습니다. 용광로 쉘은 로커에 달려있어 탭핑을 위해 기울일 수 있습니다.
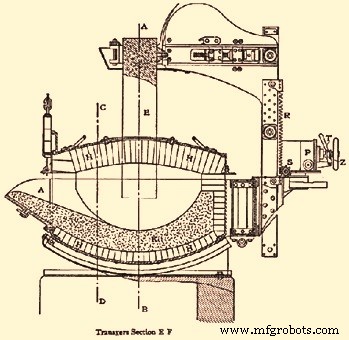
그림 2 Heroult 아크 정제로
EAF 제강 기술의 진화
철강 제조를 위한 최초의 산업용 EAF가 가동된 이후 개발이 빠르게 진행되어 1910년에서 1920년 사이에 생산량이 10배 증가했으며 1920년에는 EAF에서 500,000톤 이상의 철강을 생산했습니다. 당시의 철강 생산량 1세대 용광로는 1톤에서 15톤 사이의 용량을 가졌습니다. EAF는 초기에 강력한 경쟁자로 Bessemer/Thomas 전로와 Siemens Martin(개방형 난로) 용광로를 가지고 있었습니다. 그러나 틈새 시장은 고온, 철 합금 용융 및 긴 정련 시간이 필요한 특수강 생산이었습니다.
EAF는 강철을 만드는 과정에서 기본 단계입니다. 수년에 걸쳐 EAF는 역동적으로 진화했으며 프로세스에서 효율적이고 경쟁력 있고 지속 가능한 방법을 채택했으며 EAF의 철강 생산량은 전 세계적으로 증가하고 있습니다. 기존 방식(BF-BOF 방식)으로 제철을 할 수 없는 많은 국가들이 EAF 방식의 제강 방식을 채택하고 있다. 이들 국가가 EAF 제강 루트를 채택한 주된 이유 중 하나는 점결탄이 없고 값싼 연료에 대한 접근성으로 인해 저렴한 전력을 쉽게 이용할 수 있기 때문입니다. 철강 생산을 위해 EAF 기술을 사용하는 철강 공장은 미니 밀로 알려져 있으며 이 산업은 철강 스크랩의 최대 재활용 업체입니다.
EAF는 제2차 세계 대전에서 합금강 생산에 널리 사용되었지만 전기 제강이 확장되기 시작한 것은 그 이후였습니다. 미니 공장의 낮은 자본 비용으로 인해 전쟁으로 황폐해진 글로벌 시나리오에서 공장을 신속하게 설립할 수 있었고 또한 저비용 탄소강 '봉형 제품'(구조용 강철, 봉강 및 봉, 및 선재) 시장에서.
현재 미국 최대 철강 생산업체 중 하나인 Nucor는 1969년에 봉형강 제품 시장에 진출하기로 결정했을 때 EAF를 제강로로 하는 소형 압연기를 시작하기로 결정했고 곧 다른 제조업체들도 뒤를 이었습니다. Nucor가 미국 동부에서 빠르게 확장하는 동안, 미니 밀 작업으로 이어진 조직은 봉형 제품의 현지 시장에 집중했습니다. 여기서 EAF를 사용하면 공장에서 현지 수요에 따라 생산을 변경할 수 있습니다. EAF 철강 생산은 주로 봉형강 제품에 사용되는 반면, 통합 공장은 BF – BOF 생산 경로를 사용하여 '평판 제품'(강판, 스트립, 더 무거운 강판 등) 시장에 집중하여 이 패턴을 전 세계적으로 따랐습니다. .). 1987년, Nucor는 여전히 EAF 생산 방식을 사용하여 판재 시장으로 확장하기로 결정했습니다.
전 세계적으로 EAF 생산 및 기술의 발전은 다음과 같은 이유 때문입니다.
- 경쟁 제강 공정으로서의 노상 공정 중단
- 대규모 일관제강과 관련된 대규모 자본 및 운영 비용에서 벗어나 더 작고 자본 집약적인 소형 철강 공장으로 이동하려는 욕구
- 전기 기술의 매우 빠른 발전으로 대규모 전기 장비의 비용을 낮추고 전기 장치의 제어를 크게 개선할 수 있습니다.
- 금속 재활용에 대한 강력한 사회적 압력과 결합된 많은 국가에서 스크랩을 쉽게 구할 수 있습니다.
- 특히 개발도상국의 대체 철 공급원의 가용성 증가
- 전기 아크로에서 뜨거운 금속 및 산소 연료 사용
- EAF 기반 제강 기술의 작동, 제어, 효율성 및 제품 품질이 크게 향상되었습니다.
EAF 제강의 성장은 전력 요구 사항의 큰 감소와 철강 용해 공장의 에너지 효율, 용광로 생산성 및 작업 환경의 개선을 가능하게 하는 몇 가지 기술 개선을 동반했습니다. 이러한 기술 향상은 안정적인 전기 아크 작동, 낮은 에너지 소비, 낮은 전극 소비, 전극 파손 감소, 전극 및 전극 베어링 암에 가해지는 힘 감소, 네트워크 장애 감소 등 EAF 작업에 여러 이점을 제공했습니다.
EAF 제강 공정은 EAF 생산성 향상을 통한 변환 비용 절감을 위해 화학 에너지가 보충으로 전환될 때까지 전력에 전적으로 의존했습니다. 그러나 전기 및 화학 에너지의 효율적인 관리는 전기 아크의 효율적인 동적 제어와 산소 및 탄소의 균형 잡힌 주입을 결합하여 EAF 생산성을 높이는 것입니다. EAF 공장은 종종 직접 환원철(DRI)/열간 연탄(HBI)/열간 DRI와 재활용 철강 공급물 및 탄소 기반 재료를 슬래그 발포제 및 침탄제로 혼합하여 사용합니다. 에너지 소비 및 온실 가스 배출 감소에 대한 요구 사항에 따라 기존의 무연탄 및 야금 코크스는 탄소 기반 재료로 대체되었으며 이제는 수명이 다한 고무 타이어 및 재활용 플라스틱과 같은 대체 탄소 소스도 기존 탄소 재료를 부분적으로 대체하고 있습니다.
EAF 설계 개선
탭-투-탭 시간을 줄이기 위해 EAF 설계의 많은 기술적 개선이 이루어졌습니다. 이러한 개선 사항에는 다음이 포함됩니다.
- 높은 2차 전압과 더 긴 아크를 사용하는 초고출력(UHP) 설계의 전기로. 이 혁신은 탭 간 시간을 급격히 단축하고 시간당 EAF 생산성을 높이는 데 결정적인 역할을 했습니다. 최초의 UHP 용광로는 1963년 미국에 설치되었습니다. 135톤 용광로는 70-80MVA 변압기를 장착했으며 이는 520-600kVA/ton에 달하는 비전력을 의미합니다. 성공적인 운영으로 인해 UHP 용광로는 빠르게 대중화되었으며 비출력도 1000kVA/ton으로 증가했습니다.
- 동박 상자 디자인의 고전류 전도성 전극 암
- 최첨단 전극 제어 시스템
- 대체 에너지원의 광범위한 사용을 위한 용광로의 다양한 개구부
- 매우 빠른 움직임과 안전한 작업을 가능하게 하는 힘든 작업 조건을 견딜 수 있는 견고한 구조 설계.
- 유지보수의 용이성과 유지보수 시간의 단축을 위한 EAF의 분할 쉘 디자인.
- 고속 냉각수가 흐르는 구리 또는 콤비 냉각 패널.
- DRI/HBI/hot DRI를 위한 연속 공급 시스템으로 용광로 장입 시간이 단축됩니다.
- EBT 버너 시스템의 특수 설계로 인해 저온 EBT(편심 바닥 태핑) 영역에서 더 많은 열 입력.
- 폐쇄 슬래그 도어 적용으로 용해로 작동의 높은 유연성 및 효율성
- 지붕 리프팅 시스템, 화로 잠금 시스템과 같은 특수 설계로 유지 보수 작업이 용이합니다.
- 전력을 대체하는 탄소, 연료, 산소를 기반으로 하는 추가적인 화학에너지 투입
- 전극용 규제 설계 – 일반적으로 전극/암/마스트/케이블 어셈블리의 무게는 20톤 범위입니다. 이것은 마스트에 통합된 유압 실린더에 의해 제어 목적으로 수직으로 이동됩니다. 아크 길이는 무엇보다도 전극 아래의 끊임없이 변화하는 스크랩 또는 액체 수준에 따라 달라지므로 전극 위치(조절 시스템)를 자동으로 제어해야 합니다. 규제 시스템은 에너지 입력, 평균 전류, 아크 안정성, 스크랩 용융 패턴, 수냉식 패널에 대한 에너지 손실, 에너지, 전극 및 내화물 소비와 같은 용해로 성능의 많은 중요한 측면에 영향을 미칩니다. 이러한 모든 매개변수는 복잡한 방식으로 상호 연관되어 있으며 '최적' 제어 전략에 대해 많은 의견 차이가 있습니다.
- 다중 주입으로 인해 퍼니스 내부의 더 나은 에너지 및 열 균형을 달성합니다.
EAF 기술의 주요 발전
지난 40년 동안의 주요 기술 개선 사항 중 일부는 다음과 같습니다.
- 거품 슬래그 작업 – EAF 제강에서 스크랩의 점진적인 용융은 아크에서 노의 측벽으로의 복사 열 전달을 증가시킵니다. 아크를 슬래그 층으로 덮음으로써 아크가 차폐되고 더 많은 에너지가 수조로 전달됩니다. 이 기간 동안 발포 슬래그가 유리합니다. 슬래그 발포의 효과는 슬래그 염기도, 슬래그의 FeO 함량, 슬래그 온도 및 슬래그의 산소 또는 FeO와 반응하는 탄소의 가용성에 따라 달라집니다. 발포 슬래그는 내화 손상 및 아크 영역의 열 손실을 줄입니다. 순 에너지 절약은 철강 톤당 6-8kWh로 추산됩니다.
- 용탕에 산소를 불어넣으면 용강에 산소를 불어넣으면 열이 방출되는데, 이는 용강에 있는 탄소, 규소, 철과 산소의 반응이 발열하여 열을 발생시키기 때문입니다. 이러한 조건에서 용융 시간이 단축되고 생산성이 향상됩니다. 열 방출로 인해 내화물 소비와 함께 전기 소비가 감소하고 전극 소비가 감소합니다. 과거에는 철강 1톤당 10 cu m 미만의 산소 소비량이 일반적이었을 때 소모성 파이프 랜스를 사용하여 수동으로 랜싱 작업을 수행했습니다. 대부분의 현대식 작업은 이제 자동 랜스를 사용하고 대부분의 시설에서는 강철에 산소를 주입하기 위해 비소모성 수냉식 랜스를 사용합니다. 이러한 랜스 중 다수는 탄소를 주입할 수도 있습니다.
- 핫 힐 작업 – 핫 힐 작업에서 약 15% ~ 20%의 금속과 일정량의 슬래그가 각 태핑 후 노 바닥에 남습니다. 나머지 슬래그는 창틀 위의 용광로에서 제거됩니다. 이는 용광로에 들어가는 신선한 고형 공급물의 용융을 돕고 실질적으로 슬래그가 없는 태핑을 허용합니다. 핫 힐 작동은 합금철을 절약하고 에너지 효율성을 높입니다.
- 편심 바닥 태핑 - 편심 바닥 태핑(EBT)은 탭 시간, 온도 손실 및 슬래그 이월을 줄여줍니다. 이 기술을 사용하면 철강 톤당 12-15kWh의 전력 절감이 예상됩니다. EBT 슬래그 프리 태핑은 합금 첨가제의 높은 수율과 높은 레이들 내화 수명을 가져옵니다.
- 연소 후 실습 – 탈탄 중에 생성된 일산화탄소(CO) 가스는 로 내부의 랜스에서 주입된 산소와 함께 연소됩니다. 방출된 에너지는 수조를 직접 가열하거나 유입되는 공급 재료를 예열하는 데 사용됩니다. 멕시코와 미국의 두 공장에 설치된 특정 연소 후 제어 시스템은 전기 소비량을 각각 2%와 4%, 천연 가스 소비량을 8%와 16%, 산소 사용을 5%와 16% 줄였습니다. 18% 및 18%의 탄소 충전 및 주입
- 탄소 주입 – 탄소 주입은 다음과 같은 이점을 제공합니다. 연소 후 열 에너지를 생성하는 CO 가스. 탄소 주입은 탄소 산화를 시작하기 위해 산소 주입이 필요합니다.
- 연도 가스 모니터링 및 제어 – 사전 설정된 값을 사용하는 대신 배기 가스의 실시간 CO 및 CO2 판독값을 기반으로 사후 연소를 위한 산소 주입 수준을 조정하여 배기 가스의 화학 에너지 회수율을 50%까지 높일 수 있습니다. 이 기술을 사용하면 철강 톤당 12-15kWh의 전기를 절약할 수 있을 것으로 추정됩니다.
- 산소 연료 버너 – 산소 및 탄화수소 연료로 전기를 대체하여 전기 소비를 줄이기 위해 EAF에 산소 연료 버너/랜스를 설치할 수 있습니다. 이 기술은 용융 속도를 개선하고 용광로 전체에 더 균일한 열 분포를 제공하기 위해 도입되었습니다. 가열 시간 단축으로 총 에너지 소비량을 줄이고 정제 기간 동안 열전달을 증가시키며 슬래그 발포를 촉진하여 산소 사용 효율과 탄소 주입 효율을 높입니다. 순산소 버너를 올바르게 사용하려면 주의를 기울여야 합니다. 그렇지 않으면 총 에너지 소비 및 온실 가스 발생이 증가할 위험이 있습니다. 가열 시간이 1분 단축될 때마다 2~3kWh/톤의 에너지를 절약할 수 있습니다. 철강 톤당 18N cum의 일반적인 산소 주입률로 철강 톤당 35-40kWh의 전기를 절약할 수 있습니다.
- 스크랩 예열 – 배기 가스와 관련된 열을 활용하는 많은 스크랩 예열 시스템이 개발되었으며 일부는 배치 버킷 시스템을 기반으로 하고 다른 일부는 연속 샤프트 시스템을 기반으로 합니다. 단일 샤프트 시스템으로 최대 77kWh/톤의 전기 에너지를 절약할 수 있습니다. 핑거 샤프트 시스템을 통해 강철 톤당 최대 110kWh를 절약할 수 있으며 이는 전기 입력의 약 25%입니다.
- 충전 스크랩의 방사선원 제거 – 생산된 철강이 방사선에 취약해지는 것을 방지하기 위해 구매한 스크랩은 방사선 감지를 받아야 합니다. 시설로 들어오는 모든 스크랩은 'Exploranium' 감지 장비를 통과해야 합니다. 고위험으로 표시된 스크랩은 손 탐지기에서 추가 검사를 받습니다. 'Exploranium' 감지 장비를 사용한 두 번째 스캔은 용융 공장 납품 전에 수행되고 최종 스캔은 충전 버킷이 채워질 때 각 자석 부하에 대해 수행됩니다. EAF 백 하우스 감지기는 방사성 물질이 녹았을 경우 이를 정의합니다.
- 고온 DRI 충전 - 저온 DRI가 아닌 최대 600℃의 온도에서 고온 DRI를 충전하면 철강 톤당 150kWh의 용융 에너지가 감소합니다. 기타 이점은 생산성 증가, 트램프 요소 함량 감소, 슬래그 발포 개선 및 장입물 내 탄소 함량 증가입니다.
- 열선 충전 – 산소 주입과 함께 EAF에 열선을 충전하면 화학 에너지를 이용하여 전기 에너지 소비를 줄입니다. 이렇게 하면 탭하여 탭하는 시간, 탄소 소비 및 전기 소비가 줄어듭니다.
- 초고전력 변압기 – 전력이 MW 증가할 때마다 전기 절약은 강철 톤당 1.1kWh로 추정됩니다. 작동 전압이 한 용광로에서 600V에서 660V로, 다른 용광로에서 400V에서 538V로 증가했을 때 전력 소비는 2개의 용광로 라인에 대해 각각 11kWh/t 및 22kWh/t 감소했습니다.
- 전기로 – 작동 전압이 더 높은 전원 공급 장치의 개발로 인해 제어 및 에너지 효율성이 크게 향상되었습니다.
- 로 제어 - 이 기술은 전력 소비를 14% 감소시킵니다. 또한 천연 가스 소비량을 6% 감소시킬 수 있습니다.
- 개선된 공정 제어(신경망) – 향상된 공정 제어(신경망)는 기존 제어 시스템을 통해 달성한 것 이상으로 전력 소비를 줄이는 데 도움이 될 수 있습니다. 예를 들어 신경망 또는 '퍼지 논리' 시스템은 데이터를 분석하고 최고의 컨트롤러를 에뮬레이트합니다. EAF의 경우, 욕조의 전극을 제어하기 위해 전류 역률과 전력 사용을 사용하여 최초의 '퍼지 논리' 제어 시스템이 개발되었습니다. 철강 톤당 30kWh의 전기를 절약할 수 있을 것으로 예상되며 스크랩 및 용광로 특성에 따라 값이 변경될 수 있습니다.
- 하부 교반/교반 가스 주입 – 기존의 아크로에서는 수조 내에 자연적인 전기 난류가 거의 없습니다. 저어주지 않으면 큰 조각의 스크랩이 녹는 데 오랜 시간이 걸리고 산소 랜싱이 필요할 수 있습니다. 아르곤 또는 질소 교반은 온도 및 농도 구배를 제거하고 탭투탭 시간을 단축하며 내화물, 전극 및 전력 소비를 줄이고 철 및 합금의 수율을 향상시킵니다. 욕조에 교반 기술을 도입하여 전기를 절약할 수 있습니다. 이러한 전기 절감 효과는 철강 톤당 12~24kWh입니다.
- 직류 아크로 – 직류(DC) 아크로는 아크로 설계에서 다른 개념을 나타냅니다. 대부분의 DC 용광로는 탄소 전극에서 용광로 바닥에 장착된 양극으로 전류가 흐르는 단일 전극이 있습니다. 50%에서 60% 정도 감소된 전극 소비는 기존의 3상 아크로에 비해 DC로의 주요 이점입니다. DC 용광로의 소음 수준은 더 낮습니다. 더 낮은 유지 보수 비용이 청구되고 내화물 비용은 측벽의 경우 더 적지만 노 바닥의 경우 더 많습니다. DC 아크로에는 하단 전극(양극), DC 리액터 및 사이리스터가 추가되어야 하며 이 모든 것이 DC로에 비용을 추가합니다. 낮은 에너지 및 전극 소비를 제외하고 DC 퍼니스는 액체강의 우수한 열 및 야금 균질화를 보장합니다. 또한 이 과정을 지원하는 직류 아크의 증가된 교반 효과가 있습니다. AC 전기로와 비교하여 DC로는 네트워크 장애를 덜 유발하므로 약한 전기 그리드에도 연결할 수 있습니다. 구형 AC 용광로에 비해 순 에너지 절감은 강철 톤당 85-90kWh로 추정됩니다. 새로운 AC 용광로와 비교할 때 절감 효과는 철강 톤당 10 -20kWh로 제한됩니다.
- EAF의 폐열 회수 – 탭-투-탭 시간이 49분이고 전원이 켜진 시간이 40분인 DRI의 충전량당 150t을 녹이는 EAF의 경우 강철 톤당 약 130kWh의 에너지를 회수할 수 있습니다( 효율성 30%). 회수된 에너지를 포화 증기로 발전에 사용하면 연간 2.8MWh의 전기를 생산할 수 있습니다. 회수된 에너지를 과열증기 발전에 사용하면 연간 15.1MWh의 에너지를 생산할 수 있습니다.
- 가변 주파수 드라이브 또는 가변 속도 드라이브 – 총 팬 에너지 소비를 67%까지 줄일 수 있습니다. 전기 절약은 철강 톤당 16.5kWh로 추산됩니다.
- 트윈 쉘 DC 아크로 – 철강 톤당 15-20kWh의 전기를 절약할 수 있습니다.
- CONARC 퍼니스- 이 퍼니스는 전기 아크로의 기술적 장점과 기존의 블로잉 공정의 장점을 결합합니다. CONARC는 CONverter와 ARCing의 조합을 반영합니다. 프로세스는 두 단계로 나뉩니다. 탈탄을 위해 상단 랜스를 통해 용융물에 산소를 불어넣는 전로 단계와 전력이 공급되어 고체 물질을 용융시키고 수조를 태핑 온도로 과열시키는 전기로 단계입니다.
- 폴리머 주입 기술 – EAF 제강에서 발포 슬래그를 생성하기 위한 대체 탄소 주입제로서 고무(중고 타이어)를 포함한 폴리머로 코크스 사용을 부분적으로 대체하는 흥미롭고 새로운 특허 공정입니다. 이점은 (i) 약 3%의 비전기 에너지 소비 감소, (ii) 약 12%의 탄소 주입량 감소, (iii) 4%의 노 생산성(분당 톤) 증가, (iv) 슬래그 FeO 수준이 유지되는 것을 포함합니다. 필요한 범위 내에서 (v) NOx, CO 및 SO2에 대한 배출 수준 감소
고무 타이어와 플라스틱이 있는 EAF
One Steel의 Sydney Steel Mill이 UNSW와 공동으로 발포 슬래그 최적화를 위한 EAF 제강의 고무 타이어 사용에 대한 실험실 테스트에서 EAF가 수명이 다한 타이어에서 고무 혼합물을 주입하기 위한 공장 시험을 통해 엔지니어링 시스템을 개발하고 상용화했습니다. 및 코크스를 슬래그 발포제로서 EAF로. 이 방법은 슬래그의 부피 및 거품 증가와 같은 이점으로 더 긴 아크로 인한 개선된 전기 에너지 효율 및 아크에서 강철로의 개선된 열 전달, 슬래그 및 측벽을 통한 감소된 열 손실을 포함합니다. 반면 PIT(Polymer Injection Technology)를 사용하는 EAF 철강업체는 수율 개선, 주입 산소 소비, 내화물 및 전극 소비, 주입 시스템 마모도 기대할 수 있습니다. 고무 주입 기술(RIT)은 One Steel의 Sydney 및 Laverton EAF Steel Mills에서 표준 공정이 되었으며 고무 주입으로 도청된 40,720개의 열, 대체로 인한 코크스 13,721톤 감소 및 주입 감소로 중요한 이정표를 달성했습니다. FeO 제어 및 일관된 크기, 1,128,486개의 동급 승용차 타이어 사용. 오래된 고무 타이어와 플라스틱으로 만들어진 녹색 강철은 폐기물이나 유독 가스를 생성하지 않습니다.