하이브리드 금속-열가소성 복합 구조의 자동 결합
산업적 규모의 하이브리드 결합 활성화
FlexHyJoin은 프로젝트의 사용 사례인 Fiat Panda와 같이 금속 본체에 조립하기 위해 금속 브래킷이 용접된 열가소성 복합 지붕 보강재를 생산하기 위한 대량 생산 공정을 보여줍니다. 도시 자동차. 출처 | IVW
하이브리드 금속 복합 구조는 "올바른 위치에 올바른 재료"를 배치하여 무게를 줄이고 성능을 개선함으로써 자동차 및 항공우주 응용 분야에서 계속해서 관심을 받고 있습니다. 열가소성 복합 재료(TPC)는 용접 및 열성형 기능을 포함하여 신속한 처리로 인해 이러한 다중 재료 구조에 매력적입니다. 그러나 지금까지 복합 재료를 금속에 결합하는 것은 하중 지지 섬유를 손상시키는 드릴 구멍이 필요한 기계적 패스너에 주로 의존해 왔습니다. 접착 결합도 사용되었지만 많은 열가소성 수지가 이러한 방식으로 결합하기 어렵습니다. 또한 접착제는 재료와 무게를 추가합니다. 예를 들어, BMW i3 CFRP(탄소 섬유 강화 플라스틱) 섀시와 플라스틱 바디 패널을 사용하는 은 16kg의 접착제를 사용하여 복합 재료의 잠재적인 중량 감소를 부분적으로 상쇄합니다.
FlexHyJoin은 2015년 10월부터 2018년 12월까지 유럽 연합의 Horizon 2020 연구 및 혁신 프로그램의 자금 지원을 받아 TPC와 금속 부품을 결합하는 문제를 해결하기 위한 프로젝트입니다. 독일 라인란트-팔츠 주의 비영리 연구 기관인 IVW(Institut für Verbundwerkstoffe)와 독일 카이저슬라우테른 공과 대학(Technical University of Kaiserslautern)이 공동으로 운영하는 FlexHyJoin은 유럽 전역의 10개 파트너와 함께 TPC 자동차 루프를 구현하는 자동화 프로세스를 개발했습니다. 금속 바디 인 화이트(BIW)로 조립되는 구조. 이 전략은 금속 브래킷을 레이저로 전처리하고 유도 및 레이저 접합을 통해 지붕 보강재에 부착하여 접착제나 패스너 없이 중량 중립적인 고강도 접합부를 생산하는 것이었습니다. 이는 통합 공정 제어 및 인라인 비파괴 검사(NDT)가 있는 자동화된 단일 생산 셀에서 달성되었습니다.
140초의 하이브리드 데모
프로젝트 파트너인 Centro Ricerche Fiat(Pomigliano d'Arco/Naples, Italy)는 Fiat Panda용 지붕 보강재인 데모 부품의 사양을 제공했습니다. 현재 강철로 제작된 도시 자동차. FlexHyJoin의 경우, 부품은 Bond-Laminates(Brilon, 독일). 이 TPC 지붕 보강재를 Panda에 결합하려면 의 스틸 BIW, 0.7mm 두께의 DC04 스틸로 만든 측면 브래킷 세트(왼쪽 및 오른쪽)가 끝 부분에 레이저로 결합되었습니다. 인덕션 접합을 사용하여 동일한 재료로 만든 센터 브래킷을 부착했습니다. FlexHyJoin은 두 가지 접합 방법이 산업용 하이브리드 구조물 생산에 사용될 수 있음을 보여주었습니다.
그림. 1 하이브리드 접합을 위한 표면 구조화
FlexHyJoin은 스탬프가 찍힌 GF/PA6 지붕 보강재(상단)에 강철 브래킷의 레이저 및 유도 접합을 보여줍니다. ). 이러한 하이브리드 조인트는 금속 브래킷의 표면 처리에 의존하여 언더컷을 생성하며, 언더컷은 접합 프로세스 단계(하단)에서 녹은 플라스틱으로 채워집니다. ).
출처 | IVW
단순히 PA6 매트릭스를 강철 브래킷에 녹이면 구조적 요구 사항을 충족하기에 충분한 강도의 접합부가 생성되지 않습니다. 따라서 접합 전에 레이저 표면 처리가 필요했습니다. 자동화 생산 셀의 조립 및 통합을 맡은 Fill Gesellschaft(오스트리아 구르텐)의 프로젝트 관리자인 Johannes Voithofer는 "브라켓 표면은 레이저로 구조화되어 언더컷을 생성했습니다."라고 설명합니다. “처리된 브래킷은 합성 부품에 배치됩니다. 그런 다음 접합하는 동안 열과 압력이 가해져 복합 재료의 PA6 매트릭스가 레이저 유도 언더컷으로 흐르게 됩니다[그림 1 참조].” 구조화 프로세스는 또 다른 파트너인 Fraunhofer Institute for Laser Technology(ILT, Aachen, Germany)에서 개발했으며, 그 결과 재료 접착력과 기계적 잠금을 결합한 금속 복합 결합이 되었습니다.
그런 다음 결합된 부품은 NDT 스테이션으로 전송되어 일종의 열화상 촬영을 사용하여 결함이 있는지 스캔됩니다. "할로겐 스포트라이트는 합성 표면의 변조 가열에 사용됩니다."라고 IVW 연구원이자 FlexHyJoin NDT 및 공정 제어 개발 책임자인 Vitalij Popow가 설명합니다. “이는 복합 구조 내에서 진동하는 온도 필드로 이어집니다. 우리는 시간 경과에 따른 표면의 열 반응을 분석하고 접합부의 결함을 식별합니다.” 완전 자동화된 테스트는 제조된 각 구성 요소의 생산 셀 내에서 완료됩니다. 공정 검증은 약 400개의 조인트에서 수행되었습니다.
현재 구성된 FlexHyJoin 자동화 생산 셀은 스테이션 간 부품 로봇 전송 시간을 제외하고 각각 81초, 98~108초 및 100초의 사이클 시간과 병렬로 레이저 구조화, 결합 및 NDT를 실행합니다. Voithofer는 완성된 하이브리드 부품당 사이클 시간이 대략 140초라고 말합니다.
그림. 2 산업 규모의 하이브리드 조인 활성화
FlexHyJoin 파일럿 생산 셀에는 표면 구조화, 결합 및 NDT를 위한 3개의 모듈식 스테이션이 있습니다. 셀의 단일 핸들링 로봇은 로딩 드로어에서 이러한 각 스테이션으로 구성품을 옮기고 완성된 하이브리드 부품을 인접한 드로어에 둡니다. 출처 | IVW 및 채우기
레이저 구조화
레이저 구조화 공정은 금속 브래킷의 결합 표면에 언더컷 형상의 라인을 생성합니다. FlexHyJoin의 경우 언더컷은 너비 75마이크로미터, 깊이 215마이크로미터로 측정되었습니다. 이러한 측정은 라인 수와 전체 라인 패턴을 모두 맞춤화할 수 있으며, 이상적으로는 부품 및 주기 시간 요구 사항을 충족하도록 일치됩니다.
IVW 연구원이자 FlexHyJoin 유도 접합 장치의 개발 팀 리더인 Stefan Weidmann은 "접합 표면의 미세 구조 수와 위치를 구성 요소의 하중에 맞게 조정할 수 있습니다."라고 설명합니다. "미세 구조 사이의 거리는 접합 표면의 부하가 높은 영역에서 줄어들고 부하가 적은 영역에서 증가하여 효율적인 미세 구조 프로세스를 가능하게 합니다."
IPG Photonics(Burbach, Germany)에서 제공하는 고출력 단일 모드 파이버 레이저를 사용하여 금속 브래킷 표면을 제거하여 구조화를 수행합니다. 이 YLR-1000-WC 레이저는 1,070나노미터의 방출 파장에서 1,000와트의 최대 출력을 제공합니다. Fraunhofer ILT의 폴리머 처리 팀 리더인 Christoph Engelmann은 "우리는 초점 크기가 약 40마이크로미터로 유지되는 높은 초점성 때문에 미세 구조화 공정에 단일 모드 파이버 레이저를 사용했습니다."라고 설명합니다.
레이저는 ABB 1200 로봇 팔에 장착된 광학 헤드에 들어 있습니다. "광학 헤드 내부에는 240mm x 240mm 작업 필드에서 빔을 편향시키는 두 개의 검류계 미러가 있습니다."라고 Engelmann은 설명합니다. “게다가 z-높이를 추적하는 이동식 렌즈(z-shifter)가 하나 있습니다. 우리는 로봇을 사용하여 금속 구성 요소 위에 스캔 헤드를 배치한 다음 미러에 의해 빔이 편향되고 미세 구조의 각 단일 라인에 대한 z-위치는 z-시프터에 의해 조정됩니다. 따라서 처리 중 헤드의 움직임이 없습니다. 이러한 방식으로 우리는 2.5D 부품을 처리할 수 있으며 각 개별 라인에 대해 동일한 z-위치를 유지하지만 라인 간에 조정할 수 있습니다.”
Voithofer는 파일럿 생산 셀의 검은색 캐비닛을 언급하면서 "안전상의 이유로 구조화 및 결합 장치가 모두 밀폐되어 있습니다"라고 설명합니다(그림 2). 따라서 자동화된 게이트/도어는 레이저 작업 중에 낮게 유지되어 완성된 부품을 제거하고 새 부품을 삽입할 수 있습니다.
그림. 3 유도 및 레이저 접합 셀
접합 셀에서 유도 접합은 중간 브래킷을 부착하는 데 사용되며 레이저 접합은 합성 지붕 활의 양쪽 끝에 있는 측면 브래킷을 접합하는 데 사용됩니다. 출처 | IVW 및 채우기
유도 및 레이저 접합
구조화 셀에 인접해 있는 결합 셀은 두 가지 별개의 작업으로 구성됩니다. 중앙 브래킷의 유도 결합과 왼쪽 및 오른쪽 브래킷의 레이저 결합입니다. Weidmann은 "중앙 브래킷과 같이 중간 정도의 복잡성을 가진 더 큰 부품의 경우 유도 접합이 더 적합한 접합 방법입니다. “인덕터가 있는 세라믹 통합 도구는 결합 영역에 압력을 가하고 전자기장을 투과하므로 가열을 위해 금속 브래킷에 에너지를 효율적으로 입력할 수 있습니다. 이것은 평평한 모양에 편리하지만 측면 브래킷의 형상과 같은 복잡한 모양에는 더 어렵습니다. 따라서 레이저 접합을 사용하는 것이 더 효과적이었습니다.” Weidmann은 "유도 접합은 대형 부품과 중간 정도의 복잡성에 가장 적합하지만 레이저 접합은 복잡한 부품에 더 적합합니다."라고 덧붙입니다.
합성 지붕 보강재의 드릴 구멍은 열성형 보강재의 곡률과 일치하도록 모양이 지정된 지지 도구 위에 정렬됩니다. 중앙 브래킷의 레이저 절단 구멍은 지붕 보강재에 위치하며 측면 브래킷은 지붕 보강재의 끝 부분과 일치하는 모양으로 정렬됩니다.
“중앙 브래킷은 불연속을 사용하여 결합되었습니다. 유도 결합. Weidmann은 "이것은 본질적으로 준정적 프레스 접합입니다"라고 말합니다. "이는 단순히 한 곳에서 영역 접합을 달성하는 정적 프로세스임을 의미합니다. 그러나 복합 재료의 두께가 (유도) 결합 중에 적용되는 통합 압력에 대해."
유도 결합 장치에는 유도 코일에 교류 전기장을 공급하는 KGR(이탈리아 Brandizzo) 고주파 발전기가 포함되어 있습니다. 헤드는 전기 모터와 스핀들(그림 3)을 통해 이동되어 세라믹 통합 도구가 금속 브래킷을 아래로 누르도록 합니다. 강화 도구의 유도 코일은 금속을 가열하여 복합 매트릭스를 녹이고 접합부를 생성합니다. Weidmann은 "가열 및 냉각 전반에 걸쳐 압력이 가해집니다."라고 말합니다.
측면 브래킷의 레이저 접합은 유도 접합과 동시에 시작됩니다. 지지 도구의 양쪽에 있는 두 개의 클램핑 장치는 측면 브래킷에 4,000뉴턴의 클램핑 힘을 가할 수 있습니다. Voithofer는 "복합재와 금속 구성요소 사이의 간격을 최소화하려면 클램핑이 필요합니다."라고 설명합니다. "이렇게 하면 관절의 공극을 방지할 수 있습니다." 클램핑 힘이 적용된 후 레이저 헤드가 제자리로 이동합니다. Leister Technologies(스위스 Kägiswil)에서 공급한 LineBeam 다이오드 레이저가 장착되어 있습니다. Leister의 Johannes Eckstaedt는 이 레이저가 980나노미터의 방출 파장에서 600와트의 최대 출력을 갖는다고 설명합니다. 빔은 광학 렌즈에 의해 27mm x 1mm 선으로 형성되고 금속 브래킷에 초점이 맞춰집니다. 레이저 헤드는 모양의 브래킷 표면을 따라 이동할 수 있도록 로봇 팔에 장착됩니다. "우리는 브래킷의 각 영역에 대해 서로 다른 속도를 설정하여 균일한 접합 온도를 달성하고 최상의 접합 결과를 위해 열 응력을 줄였습니다."라고 Eckstaedt는 말합니다.
일반적으로 레이저 접합은 투과 접합 또는 열전도 접합을 사용할 수 있습니다. 레이저 투과 접합의 경우 접합되는 합성물은 선택한 레이저 파장에 대해 투명해야 합니다. 그런 다음 레이저가 합성물을 통과하여 브래킷의 금속 표면에 부딪혀 가열됩니다. 그러나 이 방법은 지붕 보강재의 유기 시트 라미네이트가 레이저 투명하지 않았기 때문에 FlexHyJoin 데모에서는 사용되지 않았습니다. 대신에 열전도 접합의 대체 방법이 사용되었습니다. 이것은 단순히 금속 표면에 레이저를 직접 적용하여 금속 모재를 통해 복합재로 열을 전도하여 220-300ºC에서 PA6 매트릭스를 녹이고 접합부를 생성합니다. "강철 브래킷의 높은 열 전도성으로 인해 레이저 열이 빠르게 확산되어 측면 브래킷을 효율적으로 결합합니다."라고 Voithofer는 말합니다.
1단계 TPC 루프 보우 및 금속 브래킷은 FlexHyJoin 셀의 부품 서랍에 수동으로 로드됩니다. 서랍이 닫히고 생산이 시작됩니다.
2단계. 로봇은 금속 브래킷 세트를 집어들고 이를 구조화 셀에 배치합니다. 레이저 보호 도어가 닫힙니다.
3단계. 구조화 셀 내부에서 고출력 파이버 레이저는 복합 지붕 보강재에 결합될 브래킷 표면에 언더컷을 생성합니다.
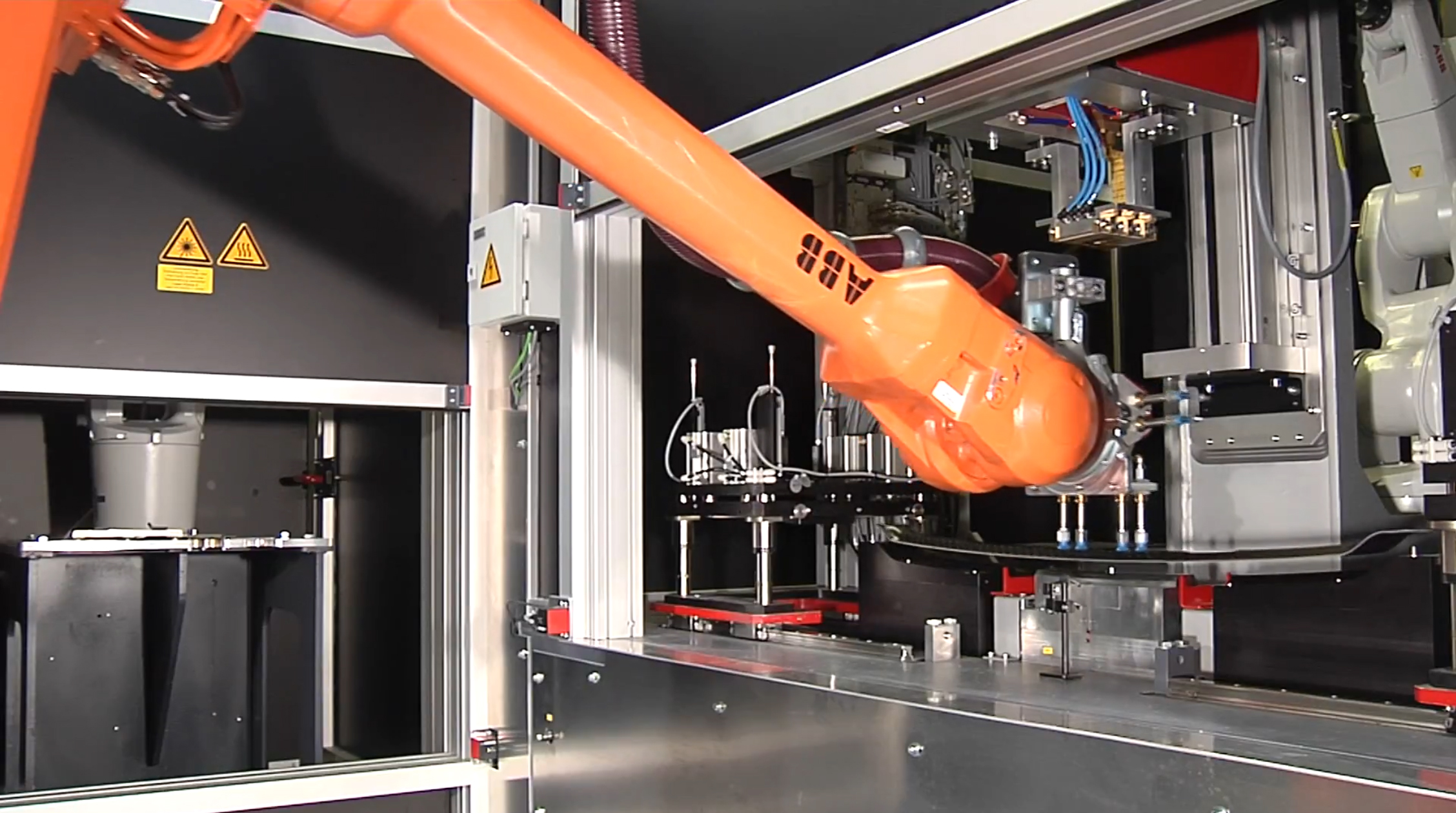
4단계. 브래킷이 레이저 처리되는 동안 로봇은 부품 서랍에서 TPC 루프 활을 집어 구조 셀의 오른쪽에 있는 결합 셀에 넣습니다.
5단계. 로봇은 구조화 셀로 돌아가서 처리된 브래킷을 집어 구조화된 면이 아래로 향하게 하여 TPC 루프 보우에 놓습니다.
6단계. 그런 다음 로봇은 3개의 브래킷에 클램핑 유닛을 배치합니다. 인덕션 결합 장치가 중앙 브래킷으로 내려갑니다. 유도 코일은 금속 브래킷을 가열하여 기본 합성물의 PA6 매트릭스를 녹입니다.
7단계. 인덕션 접합이 완료되면 레이저 접합 유닛을 내려서 왼쪽 브래킷과 오른쪽 브래킷을 접합합니다. 레이저는 금속을 가열하여 밑에 있는 PA6 매트릭스가 언더컷으로 녹아서 고강도 접합을 생성합니다.
8단계 완성된 하이브리드 구조는 NDT 셀에 배치되어 잠금 열화상 촬영이 결함을 감지하는 데 사용됩니다. 할로겐 램프는 합성 표면을 가열하고 IR 카메라는 시간 경과에 따른 반응을 측정합니다. 이 데이터의 분석은 시각적 품질 평가를 제공하기 위해 처리됩니다.
조인 프로세스 제어
두 접합 프로세스를 제어하는 기본 방법은 테스트를 통해 정의된 최적화된 매개변수 집합에 대해 온도와 시간을 측정하는 것입니다. “따라서 우리는 다른 매개변수로 접합 테스트 샘플을 생성하고 특수 테스트 설정을 사용하여 각 매개변수 세트에 대해 기계적 테스트를 수행했습니다. 측면 브라켓은 전단시험과 박리시험을 병행하여 개발하였으며, 센터 브라켓은 겹침 전단시험과 유사한 압력하중시험을 하였으나 당기지 않고 밀어서 전단하중을 구하였다. 결합 영역에서”라고 Popow는 말합니다. 이러한 특수 테스트의 설정은 테스트 결과의 분석도 수행한 EDAG Engineering GmbH(EDAG, Fulda, Germany)와 함께 설계되었습니다. 이 절차에 따라 결합 프로세스에 가장 적합한 매개변수 세트를 식별한 다음 파일럿 생산 셀에서 사용했습니다.
Weidmann은 "유도 접합 프로세스는 미리 보정되었습니다. "약 30초 후에 접합 온도에 도달한다는 것을 알고 있지만 과열을 방지하기 위해 안전상의 이유로 현장 온도도 측정합니다." 표면 복사를 원격으로 측정하는 고온계를 사용하여 유도 접합 영역에서 알려진 핫스팟을 측정했습니다. "그러나 높은 수준의 조사된 빛과 열로 인해 레이저 접합의 정확한 측정을 제공할 수 없습니다."라고 그는 설명합니다. 그러나 접촉 센서는 레이저 접합 영역의 합성면에 사용할 수 있지만 일반적으로 금속으로 만들어지고 유도에 의해 가열되고 측정이 왜곡되기 때문에 유도 접합 공정에는 적용할 수 없습니다.
Weidmann은 "모든 조인트의 가열된 영역도 프레싱 도구와 클램핑 고정구로 덮입니다."라고 말합니다. “그래서 우리는 품질 보증 방법으로 접합 전후에 압력과 열에 의한 부품의 두께 변화를 검증했습니다.” 이 두께 변화는 지붕 보강재용 위치 지정 도구에 통합된 거리 센서에 의해 측정됩니다(그림 3 참조). "부품을 함께 누르면 거리 센서가 움직입니다."라고 그는 설명합니다. “열과 접합 압력을 가하면 용융된 매트릭스 폴리머가 레이저 구조화의 공동으로 흐르고 접합부가 냉각될 때까지 접합 영역에서 약간 압착됩니다. 이것은 거리 센서에 의해 기록되는 두께의 변화로 이어집니다.” Weidmann과 IVW 팀은 이 거리를 부품 품질과 연관시켰습니다. Weidmann은 "두께 변화(즉, 압축)가 0.1mm보다 크면 접합 품질이 좋다는 것을 의미합니다."라고 말합니다.
인라인 NDT
IVW는 품질 보증을 위한 또 다른 방법인 인라인 열화상 검사를 개발했습니다. "품질 보증을 위해 주요 목표는 조인 영역의 속성을 확인하는 것이었습니다."라고 Popow는 설명합니다. "하지만 이것은 매우 어려웠기 때문에 부품이 완성된 후 접합부의 합성 면에 대해 열화상 촬영을 수행했습니다."
IVW는 다른 능동 방법(예:펄스 위상 열화상 측정)보다 더 나은 신호 대 잡음비를 제공하고 더 깊은 결함도 검사할 수 있기 때문에 Lock-In Thermography라고 하는 능동 열화상 기술을 선택했습니다. Popow는 "기본 아이디어는 복합 재료에 열을 가한 다음 결합 영역으로 전도하고 다시 표면으로 전달하는 것입니다."라고 말합니다. "Lock-in Thermography를 사용하면 구성 요소가 여러 미문. 그런 다음 시간이 지남에 따라 이 응답을 분석합니다. 보이드 또는 결함으로 인해 균질하지 않은 복합 표면과 결합 영역 사이의 영역이 있는 경우 열 응답에 표시됩니다."
열 반응은 이미지로 캡처됩니다. 이러한 이미지를 구성하는 점은 그림 요소의 약어인 픽셀입니다. 각 픽셀은 측정 포인트이기도 합니다. 따라서 전체 검사 영역에서 각 픽셀에 대한 온도 신호를 분석합니다. "결과적으로 각 픽셀에 대한 진폭 및 위상 정보를 얻은 다음 소프트웨어가 이를 다시 이미지로 재구성하여 시각적으로 검사할 수 있습니다."라고 그는 덧붙입니다. 그러나 테스트한 126개 부품에 대한 대규모 측정 세트도 제공했습니다. "우리는 이러한 NDT 결과를 EDAG에서 수행한 기계적 테스트 결과와 연관시켰습니다."라고 Popow는 말합니다. 그의 팀은 브래킷을 제거한 후 결합 영역도 테스트했습니다. 즉, 파괴 테스트입니다. "따라서 우리는 세 세트의 테스트 결과를 연관시켰고 이제 열화상 측정 결과의 시각적 분석을 통해 저강도 접합 영역과 고강도 접합 영역을 식별할 수 있습니다."라고 그는 말합니다.
대량 생산을 위한 통합 셀
FlexHyJoin의 가장 큰 성과 중 하나는 각각 다른 프로젝트 파트너가 개발한 모든 기술 장치를 최적화된 자동화된 생산 라인에 통합하는 것이라고 Weidmann은 말합니다. Fill에서 장비를 통합한 Voithofer는 "우리에게 배송된 각 장비 세트는 다른 컨트롤러를 사용했습니다. 다른 모든 프로세스 단위를 제어하기 위해 마스터 PLC를 고안해야 했습니다.” 여기에는 Fill이 공급한 레이저 인클로저와 세포 처리 로봇이 포함됩니다. "또한 이러한 모든 프로세스 단계는 서로 다른 시간이 걸리기 때문에 함께 작동하는 것이 매우 어려웠습니다."라고 덧붙였습니다.
Voithofer는 최상의 흐름을 위해 이들을 배치하는 방법을 고려하여 각 프로세스 장치 및 로봇에 대한 아키텍처를 개발하는 것으로 시작했습니다. "우리의 개념은 3개의 스테이션(구조화, 결합 및 NDT)을 3개의 개별 하우징에 모듈식으로 유지하는 것이었습니다."라고 그는 말합니다. “이런 식으로 우리는 단일 단위를 추출하여 무역 박람회나 기타 시연 프로젝트에서 사용한 다음 반환할 수 있습니다. 따라서 작업 셀은 모듈식이지만 통합되어 있습니다.”
직렬 복합재 생산을 위한 이러한 유형의 시스템 통합 분야에서 수십 년 간의 경험은 Popow가 FlexHyJoin의 가장 큰 업적이라고 생각하는 실험실 규모에서 산업 규모로의 이동을 달성하는 데 도움이 되었습니다. "우리는 금속에 접합된 복합 재료의 대량 생산에 적합한 이와 같은 공정을 실현한 최초의 컨소시엄입니다."라고 그는 말합니다. Voithofer는 "이 프로세스는 스태빌라이저 링크, 범퍼 및 도어와 같은 많은 자동차 부품에 사용할 수 있습니다."라고 말합니다. "가벼운 BIW의 금속 부품에 연결되는 복합 부품이 많이 있습니다."
여러 산업에 대한 적응
그러나 셀이 연속 생산되기 전에 몇 가지 변경이 필요합니다. Voithofer는 "우리는 더 이상 레이저 구조화 및 결합을 별도의 인클로저에 보관하지 않고 하나로 결합할 것입니다."라고 말합니다. "이렇게 하면 이러한 프로세스 간에 인클로저 도어를 열고 닫을 필요가 없어 주기 시간이 단축됩니다." 그는 또한 컨베이어 벨트에서 모든 스테이션을 선형으로 연결했습니다. 따라서 라인은 BIW로 조립할 준비가 된 셀에서 나오기 전에 부품을 픽업하여 각 스테이션의 컨베이어에 다시 배치하면서 계속해서 가동됩니다. 이렇게 하면 사이클 시간이 더욱 단축됩니다. 또한 수백 개의 부품을 공급할 수 있는 확장된 서랍을 통해 재공급 없이 전체 교대조를 통해 라인을 실행할 수 있습니다.
이 파일럿 생산 셀은 자동차 산업을 대상으로 했지만, Popow는 항공 우주, 스포츠/소비재 및 산업 응용 분야에 쉽게 적용할 수 있다고 말합니다. Weidmann은 다음과 같이 말했습니다. 유일한 변경 사항은 유도 결합 다짐 도구, 레이저 결합을 위한 클램핑 고정구 및 지지 도구입니다. 세포의 주요 부분은 동일하게 유지되어야 합니다.” 그는 IVW가 직조 탄소 섬유/폴리페닐렌 설파이드(PPS) 유기 시트 복합 재료에 티타늄과 강철의 하이브리드 결합을 시연했으며 현재 폴리에테르에테르케톤(PEEK) 및 폴리에테르케톤케톤(PEKK) 시연을 개발하고 있다고 언급했습니다. Weidmann은 "이를 위해서는 접합 프로세스를 더 높은 온도에 맞게 조정하고 최적의 프로세스 매개변수를 재정의해야 합니다."라고 말합니다. "셀은 알루미늄과 구리는 물론 폴리프로필렌 및 폴리에틸렌과 같은 기타 열가소성 복합 매트릭스 시스템을 비롯한 다양한 재료에 개방되어 있습니다."
"프로젝트 파트너는 함께 잘 협력했으며 개발을 더욱 발전하게 되어 기쁘게 생각합니다."라고 그는 말합니다. "우리는 이러한 유형의 생산이 매우 유망하다고 생각하며, 지금까지 업계에서 받은 반응은 이 약속을 보는 다양한 회사가 있음을 보여줍니다."