현대 선재 압연기의 주요 특징
현대 선재 압연기의 주요 기능
WRM(선재 압연기)의 목적은 강철 빌렛을 재가열하여 선재로 압연하는 것입니다. 선재 공장의 선재 생산은 끊임없이 변화합니다. 선재의 품질과 선재 공장의 유연성 및 비용 효율성에 대한 요구가 증가함에 따라 새롭고 혁신적인 기술과 공정의 개발이 필요했습니다. 현대식 선재 압연기는 높은 생산 속도로 더 작은 치수를 압연하는 동시에 투자 및 운영 비용을 합리적인 수준으로 유지할 수 있는 고속 압연기입니다. 일반적으로 선재 압연기는 연간 생산량이 300,000 t에서 800,000 t 이상(2가닥 압연기)으로 설계됩니다. 압연기는 초당 50미터에서 초당 120미터 범위의 속도로 압연할 수 있습니다. 일반적인 제품 크기는 5.0mm ~ 20mm 범위입니다. 재료 범위는 저탄소강에서 고탄소강, 냉간압연강, 와이어 인발강, 합금강, 스프링강, 볼베어링강, 전극 품질강, 보강봉 및 공구강으로 구성됩니다. 현대식 선재 공장은 다음 요구 사항을 충족해야 합니다.
- 높은 생산성과 높은 수율과 결합된 높은 공장 가용성.
- 낮은 유지보수 필요성 충족
- 낮은 에너지 소비 요구 충족
- +/- 0.10mm 범위의 선재 치수 공차 및 약 0.2mm 범위의 타원형.
- 0.5%~0.6% 정도의 선재 손실이 적습니다.
- 음수 허용 오차(단면 중량).
- 로드 전체에 걸쳐 치수의 변화가 없습니다.
- 균일한 물리적 특성.
- 중간과 백엔드 사이의 공칭 편차가 있는 균일한 무게
이러한 까다로운 요구 사항을 달성하기 위해 많은 중요한 기능이 현대식 선재 압연기에 통합되었습니다. 그 중 일부는 아래에 설명되어 있습니다.
- 재가열로 – 현대의 선재 공장에는 일반적으로 컴퓨터로 제어되는 에너지 효율적인 보행로 또는 보행로가 장착되어 있습니다. 이 재가열로는 요구되는 생산 속도로 그리고 스키드 마크와 콜드 스팟 없이 목표 온도로 빌렛을 균일하게 가열합니다. 이 용광로는 용광로의 장입물로 차갑거나 뜨거운 빌렛을 수용할 수 있습니다.
- 하우징 없는 롤 스탠드 – 하우징이 없는(HL) 롤 스탠드는 일반적으로 현대 선재 압연기의 황삭 및 중간 그룹 스탠드에 사용됩니다. 모듈식 설계로 수평, 수직, 기울이기 및 범용 구성과 같은 가능한 모든 구성에서 HL 스탠드 카세트를 사용할 수 있습니다. 스탠드 크기는 롤 및 롤 저널의 필요한 치수, 패스 일정, 패스 형태, 기어박스 및 모터 특성에 따라 다릅니다. HL 스탠드의 주요 특징은 구성 요소의 소형화 및 강성, 낮은 롤 굽힘 계수, 하중을 받는 상태에서 자체 정렬 초크가 있는 내구성 있는 다중 열 롤러 베어링, 초크의 백래시 없는 균형 조정, 가이드 및 가드 등의 간단하고 정확한 조정을 위해 설계된 롤러 빔입니다. 이 스탠드의 장점은 (i) 기초의 깊이와 크기 절약 (ii) 압연 제품이 요구되는 형태와 치수 허용 오차를 충족한다는 것, (iii) 롤 교체가 외부에서 이루어지기 때문에 스탠드 교체에 대한 시간 절약이 있다는 것입니다. 롤링 라인, (iv) 더 적은 수의 구성 요소와 더 쉬운 접근성으로 인해 유지보수 시간이 크게 단축됩니다. (v) 자동 롤 간격 조정 및 (vi) 동일한 스탠드 장치를 모든 위치에서 사용할 수 있으므로 작동 유연성 .
- 캔틸레버 롤 스탠드 – 캔틸레버(CL) 롤 스탠드는 다양한 용도로 다양한 크기로 사용되는 소형 스탠드입니다. 이러한 응용 분야에는 (i) 수평 및 수직 배열의 단일 스트랜드 밀, (ii) 2개 이상의 스트랜드 밀의 분할 중간 트레인 및 선재 전달 섹션의 프리피니셔 스탠드가 포함됩니다. 이러한 스탠드의 장점은 다음과 같습니다. (i) 더 작은 기초; (ii) 동일한 스탠드 유형의 카세트는 수평 및 수직 스탠드 사이에서도 교체 가능, (iii) 작은 직경에도 높은 하중 지지 강도로 인해 고속 선재 블록에 이상적으로 적합, (iv) 최적의 접근성, (v) 빠름 롤 앤 스탠드 변경.
- 냉각 및 균등화 루프 – 무연 블록에 들어가는 재료는 저온에서의 최종 압연을 위해 집중적으로 냉각되어야 합니다. 그 다음에 야금학적 특성이 완성된 선재의 단면에 걸쳐 균일하게 달성될 수 있도록 충분히 긴 균등화 섹션이 뒤따라야 합니다. 이퀄라이제이션 섹션이 없으면 표면과 코어 사이의 온도 차이가 너무 커서 후속 성형 공정에서 다른 미세 구조가 생성될 수 있습니다. 반면에 가능한 한 열간 압연되어야 하고 긴 이퀄라이징 구간으로 인해 품질이 저하되는 강종도 있습니다. 루프 기술을 사용하면 이 두 가지 요구 사항을 완벽하게 조정할 수 있습니다. 중간 열차의 재료는 짧은 직접 경로 또는 추가 워터 박스 및 긴 이퀄라이징 섹션이 있는 루프를 통한 경로를 사용하여 꼬이지 않는 블록으로 굴러갈 수 있습니다.
- 트위스트 블록 없음 – 비틀림 없음 밀이라고도 합니다. 선재 공장에서는 핵심 요소 중 하나를 나타냅니다. 이 개발을 통해서만 120m/sec 이상의 속도로 가는 선재를 안전하게 압연할 수 있게 되었습니다. 비틀림 방지 블록은 비틀림 없는 롤링을 위한 4, 6, 8 및 10 롤 스탠드일 수 있습니다. 기본 기어박스는 두 개의 공통 샤프트를 통해 롤 장치를 구동합니다. 두 가지 크기의 롤 유닛이 있는 트위스트 블록은 사용할 수 없습니다. 170/150mm 롤 및 ? 223/200mm 롤. 모든 롤 유닛은 동일하고 상호 교환 가능합니다. 압연되는 강종에 따라 패스당 10%에서 25%까지 다양한 감소율을 갖는 트위스트 블록을 사용할 수 없습니다. 블록은 이제 150m/s의 속도로 설계되었습니다. 트위스트 블록 없음은 최종 제품의 표면이 매우 마감 처리된 600 t ~ 700 t의 통과 수명을 갖는 텅스텐 카바이드 링을 사용합니다. 비틀림 방지 블록의 장점은 (i) 초고하중 하우징, (ii) 낮은 링 교체 시간, (iii) 무시할 수 있는 스프링 동작, (iv) 유지 보수 감소, (v) 더 간단한 섹션 제어, 부하 시 원격 조정 및 (vi) 다양한 등급의 선재 압연의 유연성
- Flexible reduction sizing (FRS) 블록 – 이 블록은 SMS Meer가 더 높은 등급의 압연과 동시에 압연 제품의 야금 특성을 개선하기 위해 개발했습니다. 변속 기어 박스가 있는 4가닥 블록입니다. 노 트위스트 선재 블록의 다운 라인에 설치됩니다. FRS 블록에서 모든 치수는 한 제품군 롤링의 이점으로 마무리 롤링될 수 있습니다. 즉, 전체 크기 범위에서 각 스탠드에 하나의 패스 크기만 사용됩니다. 비틀림 방지 블록과 FRS 블록 사이의 냉각 섹션으로 인해 열 기계적 압연이 가능합니다. 이 블록에는 좋은 디자인 기능이 많이 있습니다.
- 환원 압연기(RSM) – 수요가 많은 다용도 압연 기술입니다. RSM은 변형 중 퍼짐이 적고 변형 효율이 높은 3-롤 기술의 특수성을 활용합니다. 선재 축소 사이징 밀의 장점은 많습니다. 기존의 마무리 블록 뒤에 통합할 수 있어 작은 크기의 밀 생산성을 최대 60%까지 높일 수 있습니다. 그 극도의 정밀도는 많은 실제 응용 분야에서 입증되었습니다. 패스 디자인은 특허를 받았으며 재가열로 이후의 첫 번째 스탠드에서 환원 사이징 밀 앞 블록의 마지막 스탠드까지 진정한 단일 제품군 압연을 가능하게 합니다. 기존의 로드 마감 블록 뒤에 추가된 특허 받은 RSM 장치는 더 작은 크기에서 마감 속도를 크게 높일 수 있습니다.
- 열기계적 압연 – 저온 압연이라고도 하며 기본적으로 압연 공정 중 최종 재료 특성을 온라인으로 제어하는 방법입니다. 이는 부분 재결정화 또는 재결정화 억제에 해당하는 온도 범위 내에서 압연기의 마지막 패스에서 적용된 재료 변형을 포함합니다. 재결정이 억제되는 즉시 결정립 미세화 현상이 발생하여 최종 선재 제품의 기술적 특성이 향상됩니다. 또한, 로드 표면 품질이 상당히 향상됩니다. 열 기계 압연의 장점은 미세 입자 크기, 오프라인 정상화 방지, 저온 인성 개선, 경화강의 열처리 후 특성 개선, 스프링 강의 짧은 어닐링 시간, 최종 부품의 피로 강도 개선, 더 높은 인장력입니다. 2개의 블록(보통 6개의 스탠드와 4개의 스탠드)을 사용하면 모든 치수의 선재를 열기계적으로 저렴하게 압연할 수 있습니다. 높은 생산율. 노 트위스트 블록을 분할하여 최대 4패스로 마무리 롤이 가능합니다. 충분한 냉각 및 단면에 대한 양호한 온도 균등화로 높은 생산 속도로 열기계적 압연이 가능합니다. 비틀림 방지 블록 이전의 냉각 및 이퀄라이징 루프는 열 기계적 압연 중에 중요한 역할을 합니다. 이것은 첫 번째 꼬임 방지 블록으로 들어오는 온도를 750°C로 낮추고 온도 프로파일이 50°C 미만인 것을 허용합니다. 섹션에 대한 두 번째 꼬임 방지 블록 전에 다시 750°C에 도달하는 이 전제 조건 10개의 패스로 압연이 가능해짐에 따라 작은 치수에서도 열기계적 압연이 가능합니다.
- 비틀림 방지 블록 구동 – 일반적으로 비틀림 방지 블록의 모든 스탠드에는 마모 및 유지 보수가 필요한 복잡한 기어 박스 구성이 있습니다. 이들은 1차 기어박스와 2개의 공통 샤프트를 통해 직렬 배열로 된 하나 이상의 거대한 모터(최대 7000kW)에 의해 공동으로 구동됩니다. 트위스트 블록은 고정된 롤 링 직경이 필요한 고정된 감속비로 롤링할 수 있으므로 제한이 없습니다. SMS Meer는 스탠드가 노트위스트 블록과 같은 기능을 하고 보다 정밀하게 제어될 수 있도록 무트위스트 블록의 모터를 서로 제어하는 전자 기어박스를 개발했습니다. 이 드라이브는 MEERdrive로 명명되었으며 이로 인해 스탠드 간의 고정 감속비가 제거되었습니다. 이는 동일한 스탠드에서 다양한 영역 축소를 롤링할 수 있으므로 롤 크기 조정에 도움이 됩니다. 롤링 관리도 간소화되고 필요한 패스 수도 줄일 수 있습니다.
- 루프 부설 헤드 – 높은 압연 속도에서도 루프 부설 헤드를 사용하여 균일한 루프에 다양한 크기의 선재를 부설하는 것이 중요한 기준입니다. 또한 여러 등급의 열 기계적 압연으로 인해 특정 등급의 부설 온도는 야금학적 이유로 인해 크게 감소합니다. 이로 인해 부설 헤드, 특히 부설 튜브에 대한 요구가 높아졌으며 특수 재료로 만들어야 합니다.
- 제어 냉각 컨베이어 – 제어 냉각 컨베이어 시스템은 다양한 강종에 대해 원하는 선재 특성을 달성하기 위한 선재 압연기의 중요한 부품 중 하나입니다. 속도, 팬 전원 및 컨베이어의 덮개 위치를 최적으로 조합하여 단일 시스템 내에서 빠른 냉각 모드와 느린 냉각 모드를 모두 포함하여 다양한 조건에서 처리할 수 있습니다. 이 기능을 통해 선재 공장은 광범위한 일반 탄소강 및 합금강은 물론 스테인리스강 및 기타 특수 등급을 생산할 수 있습니다. 강제냉각시에는 최대한의 인력으로 풀린 권선에 공기를 불어넣고 커버를 열어 최대한 빨리 선재를 냉각시켜 층상 펄라이트를 구현합니다. '지연 냉각' 동안 선재 루프는 가능한 오랫동안 주어진 범위의 온도를 유지하기 위해 덮개를 닫고 낮은 컨베이어 속도로 팬 없이 운송됩니다. 이것은 선재의 페라이트/펄라이트 미세구조의 달성을 가능하게 한다. 결과는 압연 막대 특성으로 개선됩니다. 이를 통해 직접 사용 가능한 조건에서 더 많은 등급을 생산할 수 있으므로 구상화 어닐링과 같은 다운스트림 프로세스를 줄이거나 없앨 수 있습니다.
- 리폼 링 분배기 – 리폼 링 분배기는 최적의 배치를 위해 회전 블레이드를 사용하여 리폼 욕조의 높은 곳에서 링을 수집합니다. 이 시스템은 코일 패키지를 줄여 운송 및 보관 공간 문제를 용이하게 하여 비용을 절감합니다. 또한 수집 기능이 향상되어 결과적으로 코일 모양이 개선되어 결과적으로 엉킴과 걸림이 줄어듭니다.
독일 뒤스부르크에 있는 Arcelor Mittal의 현대식 선재 공장의 레이아웃은 그림 1에 나와 있습니다. 공장은 2012년에 시운전되었습니다.
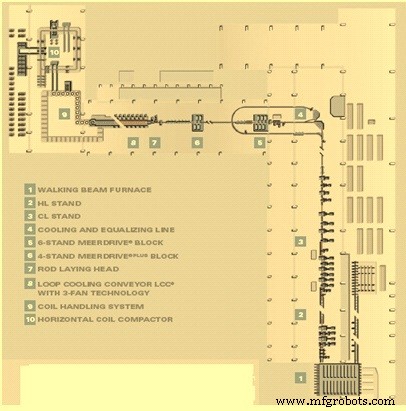
그림 1 현대 선재 압연기의 레이아웃