현대 핫 스트립 밀의 주요 특징
현대식 열간 스트립 공장의 주요 기능
핫 스트립 밀(HSM)의 목적은 두꺼운 슬래브를 재가열하고 다양한 두께의 얇은 스트립으로 압연하는 것입니다. 거대한 크기와 많은 투자로 인해 열간 스트립 밀은 수십 년의 수명이 필요합니다. 압연기는 다양한 강종, 특히 냉간 성형성이 우수하고 스트립 특성이 우수한 고강도 및 고급 고강도강(AHSS)에 대한 시장 요구를 충족할 수 있어야 합니다. 공장은 다음 요구 사항을 충족할 수 있어야 합니다.
- 높은 생산성과 높은 수율과 결합된 높은 공장 가용성.
- 낮은 유지보수 필요성 충족
- 낮은 에너지 소비 요구 충족
- 강력한 제어 및 조정을 통해 현대 고객이 필요로 하는 정밀한 두께 및 프로파일 허용 오차를 충족하여 제품 품질을 개선했습니다. 이러한 허용 오차는 다양한 국제 표준에 명시된 것보다 훨씬 더 가까울 수 있습니다.
- 더 유연한 롤링 일정을 통해 짧은 배송 시간과 더 작은 로트 크기의 경제적 롤링을 보장합니다.
이러한 까다로운 요구 사항을 달성하기 위해 많은 중요한 기능이 현대의 기존 열간 스트립 밀에 통합되었습니다. 이들 중 일부는 아래에 설명되어 있습니다.
- 재가열로 – 현대식 열간 스트립 공장에는 일반적으로 컴퓨터로 제어되는 에너지 효율적인 보행 빔로가 장착되어 있습니다. 이 재가열로는 필요한 생산 속도로 슬래브를 목표 온도로 균일하게 가열하고 스키드 마크와 콜드 스팟이 없습니다. 이 용광로는 용광로의 장입물로 차거나 뜨거운 석판을 수용할 수 있습니다.
- 디스케일러 – 디스케일러는 우수한 표면 품질을 얻기 위해 열간 스트립 밀에서 필수품입니다. 현재의 디스케일러는 고압수(최대 400바)를 매우 효과적으로 적용하는 최첨단 노즐 기술을 사용합니다. 디스케일러는 일반적으로 물이 새는 것을 방지하기 위해 폐쇄형으로 설계되었습니다.
- 슬래브 사이징 프레스 – 황삭기 분야의 슬래브 사이징 프레스는 기존 에저에 비해 기술적인 이점이 있습니다. 폭이 크게 감소(최대 350mm)하는 것 외에도 슬래브를 중앙에 바로 형성하여 훨씬 더 나은 결과를 얻을 수 있습니다. 슬래브 사이징 프레스는 더 평평한 개 뼈를 생성하여 재확산을 줄이고 사이징 효율성을 높입니다. 슬래브 헤드와 테일의 특수 짧은 스트로크 작동 모드는 작물 손실을 줄이고 수확량을 높입니다. 슬래브 사이징 프레스를 사용하면 연속 주조기의 다양한 주조 크기를 몇 가지 표준 너비로 줄일 수 있으므로 생산 유연성이 향상됩니다. 슬래브 사이징 프레스는 전체 스트립을 따라 폭 공차를 개선합니다.
- 유압 에저 조정 시스템 – 스트립의 헤드에서 테일까지의 너비는 이 시스템에 의해 제어됩니다. 이 시스템의 빠른 동적 응답은 자르기 손실을 줄이고 스트립 길이에 걸쳐 너비를 제어하기 위해 재료 헤드와 테일에서 빠른 수정 움직임을 가능하게 합니다. 최신 세대 에저는 추가 전기 기계 조정 시스템이 없는 완전한 유압 설비입니다.
- 코일박스 – 황삭밀과 정삭밀 사이에 설치하여 이송봉의 코일을 형성하여 소재이자 축열기 역할을 한다. Uncoiling하는 동안 Transfer Bar의 Tail End는 Finishing Mill에 들어갈 때 Transfer Bar의 Head End가 됩니다. 코일박스는 황삭밀과 정삭밀 사이의 거리를 짧게 할 수 있습니다. 또한 마무리 밀로 들어가는 트랜스퍼 바의 온도 강하를 최소화합니다. 코일 상자는 맨드릴이 있거나 맨드릴이 적을 수 있습니다. 맨드릴이 없는 코일 박스는 맨드릴 유형의 코일 박스에 비해 코일 내부 랩의 온도 강하를 줄이는 데 더 기여합니다. 맨드릴이 없는 코일 상자는 또한 스트립 가장자리에서 온도 강하를 줄이는 데 기여하는 측면 열 차폐를 설치할 공간을 만듭니다. 코일 박스는 그림 1에 나와 있습니다.
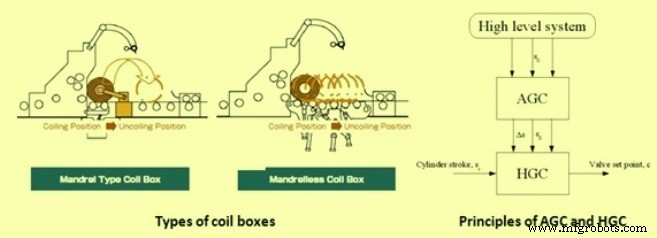
그림 1 코일 박스의 종류와 AGC와 HGC의 원리
- 자동 게이지 제어(AGC) 및 유압 갭 제어(HGC) – 작업 롤 사이의 갭, 즉 스트립 두께의 제어는 2개의 제어 모듈을 사용하여 2단계로 이루어집니다(그림 1). 첫 번째 모듈은 AGC라고 하고 두 번째 모듈은 HGC라고 합니다. AGC는 더 높은 수준의 시스템에서 두께 설정점을 받습니다. 롤 마모, 롤의 열 팽창, 스트랜드의 늘어남 및 간격에 영향을 미치는 기타 측량할 수 없는 양과 같은 것을 계산하고 보정합니다. AGC에서 사용하는 패스 중에 두께 측정이 이루어집니다. 두께 피드백은 PI 컨트롤러를 통해 전달되고 총 갭 편차에 추가됩니다. 모델 오차 보상으로 볼 수 있습니다. 이 보상은 HGC에서 실린더 위치 기준을 변경합니다. HGC에는 두께 피드백 제어가 없습니다. HGC는 두 작업 롤 사이의 간격을 제어합니다. HGC는 더 높은 수준의 설정점을 롤 갭 참조 값으로 사용합니다. 실린더의 위치 변환기로부터의 측정과 전류 보상은 롤 갭을 계산하는 데 사용됩니다. HGC는 위치 제어되며 참조 및 실제 간격을 사용하여 스트립 두께를 제어합니다.
- 자동 폭 제어(AWC) – 스트립의 헤드 엔드에서 테일 엔드까지 수직 에저에 유압 AWC 시스템을 제공하여 탁월한 폭 정확도를 달성합니다. 유압 실린더 작동 폭 제어 시스템이 사용됩니다. 이 시스템은 스트립의 헤드 엔드와 테일 엔드에 대한 짧은 스트로크 컨트롤과 스트립의 나머지 부분에 대한 AWC 시스템으로 작동합니다. 전기 기계식 서보 밸브는 유압 실린더 위치를 정밀하게 제어합니다.
- 작업 롤 굽힘 – 열간 스트립 밀에서 백업 롤은 작업 롤을 지지하고 굽힘을 방지하기 위해 큰 직경을 가지고 있습니다. 그러나 실제로는 베어링 하우징에 가해지는 힘이 더 커지면 백업 롤도 구부러집니다. 이로 인해 작업 롤에 가해지는 힘이 베어링 하우징에 가까울수록 높고 롤 중앙에서 더 작아집니다. 반면에 스트립은 반력으로 작동합니다. 이것은 롤의 중앙에 작용합니다. 이것은 차례로 작업 롤을 구부리고 스트립 프로파일에 영향을 미칩니다(그림 2). 작업 롤 벤딩 시스템은 작업 롤 베어링 하우징에 반작용력을 가하여 스트립의 프로파일 성형을 가능하게 합니다. 큰 굽힘력을 가하면 스트립이 더 평평해집니다. 굽힘력은 지속적으로 변하고 기준력은 롤링력의 함수로 계산됩니다. 양쪽에 있는 4개의 유압 실린더가 힘을 생성합니다.
- 연속 가변 크라운(CVC) – 스트립 프로파일을 변경하는 또 다른 방법은 프로파일이 있는 롤을 사용하는 것입니다. 롤 사이의 간격은 롤의 축 방향 이동으로 변경할 수 있습니다(그림 2). CVC 기술은 롤 시프팅 기술이라고도 합니다. CVC 기술은 작업 롤 벤딩보다 역학은 느리지만 범위가 더 넓습니다. CVC와 작업 롤 벤딩은 서로를 보완하기 때문에 두 기술 모두 일반적으로 현대식 열간 스트립 밀에서 사용됩니다.
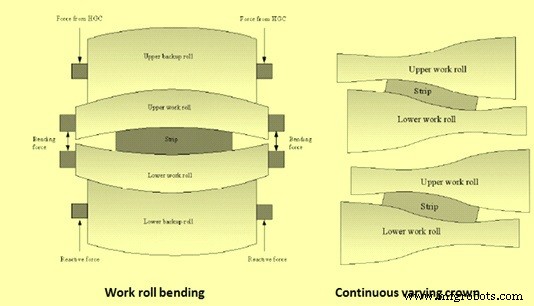
그림 2 작업 롤 벤딩 및 연속 가변 크라운
- 롤 편심 보상 – 압연기의 백업 롤 구조에 의해 발생하는 주기적인 외란으로 제품 두께 정확도에 영향을 줍니다. 센서로 직접 측정할 수 없으므로 측정된 두께 또는 측정된 롤 포스로 식별해야 합니다. 상부 백업 롤과 하부 백업 롤의 직경 차이가 크면 롤 힘이나 두께의 피드백 신호를 이용한 롤 편심 제어 성능이 좋지 않습니다. 또한 압연 시 압연 편심도를 파악해야 하므로 맨 앞단에서 제어를 적용하기 어려웠다. 롤 편심 보정 제어는 롤 포스의 하나의 신호에서 상하 롤 편심을 각각 식별하여 헤드 엔드에서 제어를 시작합니다.
- 작업 롤 윤활 – 작업 롤의 배럴을 윤활하여 표면 결함을 방지하고 롤 마모를 줄입니다. 작업 롤에 윤활 매체를 적용하는 이점에는 최소한의 롤링 오일로 작업 롤 표면의 스케일 축적 및 박리 방지, 스트립 품질 개선, 운영 비용 감소, 밀 사용 시간 연장, 밀 제한 연장 및 에너지 소비 감소가 포함됩니다.
- 강력 냉각 시스템 및 에지 마스킹 – 스트립 냉각 시스템은 마무리 압연기에 의해 압연된 스트립을 냉각시키며 마무리 압연기와 다운 코일러 사이의 런아웃 테이블에 위치합니다. 냉각 시스템은 라인 사이드 헤드 탱크 시스템을 통합하여 상단과 하단 모두에서 층류 시스템으로 설계되었습니다. 냉각 구역은 필요한 냉각 뱅크로 구분되어 빠른 냉각을 위한 집중 냉각 뱅크, 일반 냉각을 위한 일반 냉각 뱅크, 원하는 냉각 패턴 및 이중 위상 코일링 온도를 달성하기 위한 미세 온도 제어를 위한 냉각 뱅크로 구성됩니다. 그리고 여행 강철. 층류 냉각 및 에지 마스킹 시스템의 조합은 스트립 에지의 과도한 냉각을 방지하여 스트립 폭 전체에 걸친 응력 차이를 최소화합니다.
- 고급 다운 코일러 – 런 아웃롤러 테이블의 끝단에 유압식으로 조정 가능한 진입 가이드가 제공되어 스트리오가 다운코일러에 들어가기 전에 중앙에 배치됩니다. 마무리 압연 속도로 진행되는 스트립은 핀치 롤 장치에 의해 안정적으로 압착되어 코일 맨드릴로 향하게 됩니다. 다운 코일러의 기능에는 유압으로 작동되는 래퍼 롤, 맨드릴의 제어된 유압 퍼짐, 간격 및 맨드릴 롤의 자동 보정 및 정확한 유압 조정, 스트립 치수 및 재료 및 스트립의 함수로 래퍼 롤 힘의 제어된 제한이 포함됩니다. 2~3회 감고 나면 스트립 헤드에 장력이 형성됩니다.