스페인의 Clean Sky 2를 위한 열가소성 복합 재료 및 RTM의 발전
EURECAT Centro Tecnológico de Catalunya(EURECAT Technology Center Catalonia, Barcelona, Spain)는 11개의 시설, 650명의 직원 및 5천만 유로의 연간 수익을 가진 민간 비영리 R&D 조직입니다. EURECAT의 항공 및 우주 시장 프로그램 책임자인 Angel Lagraña Hernandez는 "이는 스페인에서 두 번째로 큰 R&D 센터입니다."라고 설명합니다. 그는 EURECAT 수익의 일부는 카탈루냐 정부에서, 나머지 절반은 민간 기업(대부분 중소기업(SME))에서 가져와야 하고 나머지 절반은 유럽 연합과 같은 공공 기관에서 자금을 조달해야 한다고 설명합니다. 클린 스카이 2 프로그램. "우리는 현재 18개의 Clean Sky 프로젝트를 보유하고 있습니다."라고 Lagraña는 말합니다.
Clean Sky 2의 수많은 목표와 계획된 기술 데모에서 복합 재료가 어떻게 기능하는지에 대한 예는 다음과 같습니다.
<울>
차세대 다기능 동체 시연기 — 더 깨끗한 하늘을 위한 열가소성 수지 활용
순환 경제:지역 항공기용 복합 동체 형태
Clean Sky의 FastCan을 위한 모터 레이싱 전문 지식 활용
Lagraña는 "EURECAT은 고도로 횡단적이며 항공 우주 분야 외에도 자동차, 철도 및 기타 산업 분야에서 일하고 있습니다."라고 말합니다. "또한 데이터 분석 및 블록체인 등과 같은 IT 분야에서 많은 활동을 하고 있습니다. Composites 4.0은 전략적 영역 중 하나입니다." 복합재료 내에서 그는 EURECAT이 주로 OOA(오토클레이브) 기술에서 작동한다고 언급합니다. "우리는 공정 중 수지의 유리 전이 온도(Tg) 모니터링을 포함하여 실시간 공정 모니터링을 포함하여 열가소성 수지 및 액체 압축 성형에 중점을 둡니다." (이 Tg 모니터링에 대해 자세히 알아보려면 이 블로그 끝에 있는 COFRARE 섹션을 계속 읽으십시오.)
Clean Sky 2에서 EURECAT의 가장 최근 합성물 관련 프로젝트는 다음과 같습니다.
<울>
킬베만 열가소성 복합 용골 빔을 시연하기 위해 (이 프로젝트는 GAP 785435 KEELBEMAN에 따라 유럽 연합의 Horizon 연구 및 혁신 프로그램에 따라 Clean Sky 2 Joint Undertaking으로부터 자금을 지원받았습니다);
WINFRAME 4.0 Clean Sky(2008-2017)에서 Green Regional Aircraft(GRA) 시연기를 위한 열가소성 합성물(TPC) 창틀을 만들고 Clean Sky 2(2014-2024)에서 지역 항공기 IADP(Innovative Aircraft Demonstrator Platform)로 확장합니다.
(이 프로젝트는 GAP 821323 WINFRAME 4.0에 의거하여 유럽 연합의 Horizon 연구 및 혁신 프로그램에 따라 Clean Sky 2 Joint Undertaking으로부터 자금을 지원받았습니다.)
COFRARE 2020 TPC 전단 타이가 있는 RTM(Resin Transfer Molding)을 사용하여 만든 열경화성 동체 프레임용.
(이 프로젝트는 GAP 821261 COFRARE 2020에 의거하여 유럽 연합의 Horizon 연구 및 혁신 프로그램에 따라 Clean Sky 2 Joint Undertaking으로부터 자금 지원을 받았습니다.)
열가소성 합성 용골 빔
클린 스카이 2 - JTI-CS2-2017-CFP06-LPA-02-20. 프로젝트 기간:2018년 3월 ~ 2019년 12월
KEELBEMAN 프로젝트의 목적은 A320 유형 항공기를 위한 제조 중심의 용골 빔 구조를 개발하여 열가소성 복합 재료를 통해 높은 항공기 생산 속도를 가능하게 하지만 저렴한 비용으로 개발하는 것입니다. 프로젝트 조정자로서의 EURECAT 외에도 파트너에는 다음이 포함됩니다.
<울>
에어버스 (프랑스 툴루즈) 주제 관리자로
CETMA (이탈리아 브린디시 기술 설계 및 재료를 위한 유럽 연구 센터)
CT 엔지니어링 그룹 (CT Ingenieros, Spain, Madrid), 독일 함부르크 사무소를 통해 동체, 날개 및 후방에 대한 연구와 같은 항공기 개발을 위해 Airbus와 다년간 계약을 체결한 수많은 글로벌 사무소를 보유한 회사; 후방 연구(스페인); 동체 및 발전소 관련 구조물 연구(프랑스 툴루즈) 및 날개 개발(영국 브리스톨)
소피텍 (스페인, 세비야), 항공 구조물 제조 및 조립 전문가로서 복합 재료에 대한 전문 지식과 생산 능력을 갖추고 있습니다.
CT Engineering Group은 툴루즈 사무소를 통해 용골 빔 형상의 전체 모델링을 제공했으며 Sofitec은 비파괴 검사(NDT) 검사를 개발했습니다. Lagraña는 "이러한 폐쇄형 상자 구조에서는 매우 어려운 작업입니다."라고 지적합니다.
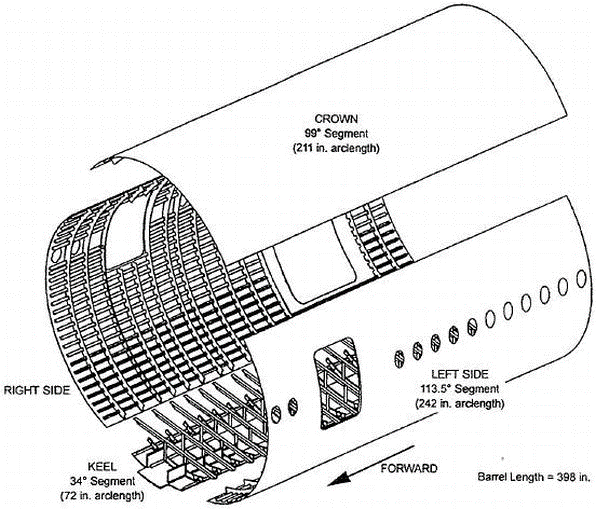
여기에 표시된 것은 Irkut Corporation(러시아 모스크바)에서 금속으로 만든 A320 용골 빔 어셈블리입니다. 이르쿠트는 2004년 에어버스와 계약을 맺어 기수 착륙 장치 베이, 용골 빔, 플랩 트랙 등의 부품을 평균적으로 A320 계열 항공기 3대에 1대씩 설치한 것으로 알려졌다. 출처 | 이르쿠트
용골 빔 구조의 개발
“오늘날 Airbus를 제외한 대부분의 항공기 용골 빔은 금속으로 만들어집니다.
A350은 모놀리식 탄소 섬유 복합재입니다.”라고 Lagraña는 말합니다. "많은 수의 리벳과 조립에 상당한 시간이 필요합니다." 그는 용골 빔이 동체의 중요한 구조라고 설명합니다. “용골 빔이 착륙 중 파손되어 전체 동체에 금이 가고 파손되는 경우가 있었습니다.
Steve Wilhelm의 2011년 기사에 따르면 A350 용골 빔은 70% 합성물이고 길이가 54피트(16.5미터)이고 10,000개의 패스너와 함께 사용되며 무게는 1.2톤이며 항공기의 중추를 형성합니다. Wilhelm은 경쟁력 있는 Boeing 787 항공기가 "그렇게 견고한 용골 구조에 의존하지 않습니다. 왜냐하면 선체 강도의 더 많은 부분이 끝에서 끝까지 함께 고정된 합성 배럴에서 나오기 때문입니다." 그런 다음 기사는 G2 Solutions LLC 항공우주 컨설팅 회사(미국 워싱턴주 커클랜드)의 관리 파트너인 Michel Merluzeau의 말을 인용합니다. 그는 Airbus 설계를 "보다 전통적"이고 "위험이 덜한" 것으로 설명하지만 용골 빔이 "필수"라고 지적합니다. 해당 항공기의 구조적 무결성."
Airbus는 실제로 2001년에 A340용 합성 용골 빔을 개척했습니다. 그러나 위에서 설명한 것처럼 많은 수의 리벳이 필요하며 합성물을 사용하여 가능한 무게 절감에 반대되는 작업이 필요했습니다. 따라서 KEELBEMAN 프로젝트의 주요 목표는 함께 용접되는 열가소성 복합 부품을 사용하여 패스너를 최소화하는 것입니다.
TPC 용골 빔
Lagraña는 "조립을 위해 용접을 사용하는 열가소성 합성 용골 빔의 개발은 Wing of Tomorrow 및 Fuselage of Tomorrow와 같은 프로그램을 포함하는 Airbus의 미래 항공기 개발의 일부입니다."라고 말합니다. "KEELBEMAN 내에서 스트링거가 있는 용골 빔의 250mm x 500mm x 1m 길이 데모 섹션을 생산했으며 가능한 한 많은 자동화로 이 구조를 용접할 가능성을 보여주었습니다."
Lagraña는 CETMA가 개발한 연속 압축 성형(CCM) 공정에서 탄소 섬유/폴리에테르케톤케톤(PEKK) 단방향(UD) 테이프를 사용하여 데모용 벽판과 스트링거를 제작했다고 밝혔습니다("항공우주 등급 압축 성형" 및 "PEEK 대 PEKK 참조). vs. PAEK 및 연속 압축 성형”). "EURECAT의 전통적인 비등온 압축 성형을 사용하여 만든 가로 보강재용 리브도 있습니다."라고 Lagraña가 덧붙입니다.
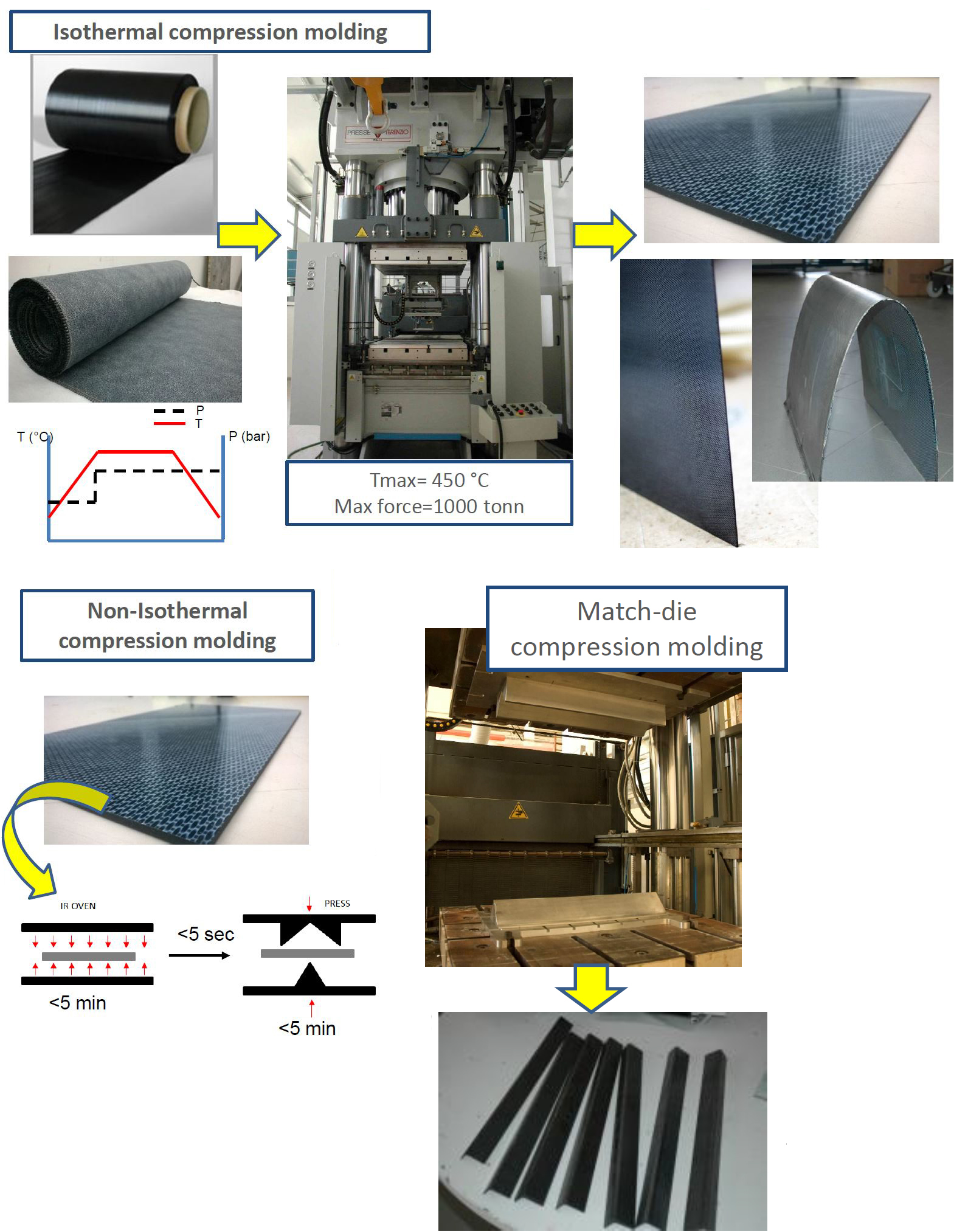
유도 용접을 핵심 요소로
Lagraña는 CETMA가 KEELBEMAN의 부품 생산뿐만 아니라 특허 받은 유도 용접 기계 및 기술을 사용하는 데모 장치의 조립에서도 핵심적인 역할을 했다고 말합니다. 이 용접은 원래 위에 표시된 TPC 구조의 등온 및 비등온 압축 성형과 함께 첫 번째 Clean Sky 프로그램의 ECO FAIRS 프로젝트(2011-2014)에서 개발되었습니다. ECO FAIRS에서 CETMA는 이 모든 기술을 사용하여 Agusta Westland 헬리콥터 꼬리의 기존 상부 패널(스트링거 강화 스킨 패널)과 곡선형 스폰손 페어링 데모를 기반으로 프로토타입 데모를 제작했습니다. 이들은 CETEX(TenCate에서 제공, 현재 Toray Advanced Composites) T300 3K 5HS 탄소 섬유 직물과 양면 PPS(폴리페닐렌 설파이드) 필름을 사용하여 제작했지만 CETMA는 PEEK 및 PEI 복합 재료를 사용한 유도 용접도 입증했습니다.
CETMA는 가장 유망한 열가소성 복합 용접 기술로 유도 용접(IW)을 선택하고 용접 및 전자 엔지니어링 전문가인 SINERGO srl(Valdobbiadene, Treviso, Italy)과 협력하여 새로운 유도 용접 기계를 개발했습니다. SINERGO (아래 이미지 참조)에서 제공하는 갠트리 기반 SICE 1 WIDE 기계 최대 1m x 1m 크기의 항공우주 품질 부품을 연속 용접할 수 있습니다. 여기에는 용접되는 재료 내에서 최적화된 온도 분포가 달성되도록 하는 강력한 제어 시스템이 포함됩니다. 기계에는 통합 압력을 적용하기 위한 냉각 실린더와 유도된 와전류의 흐름이 제한되어 높은 전류 밀도 및 과열을 초래하는 가장자리와 같이 필요한 곳에서 열을 제거하기 위한 공랭 시스템이 장착되어 있습니다. . 기하학적으로 복잡한 형상을 용접하기 위해 6축 로봇 팔에 CETMA 유도 용접 헤드를 설치하는 것도 가능합니다.
CETMA는 또한 시뮬레이션 도구를 사용하여 유도 용접 프로세스를 최적화하고 COMSOL Multiphysics(COMSOL Inc., Burlington, Mass, U.S.) 유한 요소 모델링(FEM) 소프트웨어를 사용하여 수치 해석을 수행하는 능력을 개발했습니다. 많은 물리적 테스트를 통해 이러한 모델을 검증했습니다. CETMA는 전단 강도 값이 문헌에 보고된 최대값에 매우 가까운 용접 쿠폰에 대한 단일 랩 테스트를 통해 최적화된 공정 매개변수를 확인했습니다. 특히, 구조용 접착제를 사용할 때의 최대값보다 훨씬 높았습니다.
CETMA는 직조 및 UD 탄소 섬유는 물론 PEEK, PEI, PEKK, PP, PA6, PA12 및 열가소성 PVB(폴리비닐 부티랄) 하이브리드를 사용한 CF/에폭시 용접을 비롯한 다양한 재료에 대한 용접 능력을 입증했습니다. 용접을 위해 열경화성 기질에서 열가소성 면으로의 전환을 위한 층. (이 섹션의 세부 정보 대부분은 CETMA 역량 프레젠테이션 및 CORDIS 최종 보고서 에코 페어) CETMA는 2014년에 유럽 특허를 신청했고 발명가인 Silvio Pappada와 Andrea Salomi는 2016년에 특허 EP2801472A1을 받았습니다. CETMA는 다음을 포함하여 이 기술에 대한 수많은 논문과 프레젠테이션을 발표했습니다.
<울>
"오토클레이브 외 기술 개발을 지원하는 유한 요소 시뮬레이션", A&D, 2012년 10월 11-12일
"PPS-탄소 복합 재료의 연속 유도 용접을 지원하는 유한 요소 시뮬레이션", SEICO 13, 2013년 3월 11-13일 "파리"
"항공 우주 부문의 열가소성 복합 재료를 위한 새로운 유도 용접 기계 개발", 이탈리아 항공 우주 항공 협회 XXII 회의 나폴리, 2013년 9월 9-12일
"항공 우주 분야의 유도 용접", TPRC, Thermoplastic Composites European Consortium, 웹 회의, 2013년 12월.
"항공우주 부문의 열가소성 부품에 대한 전체 규모 테스트", SEICO 14, 2014년 3월 10-11일 "파리"
"항공우주 부문을 위한 새로운 유도 용접 장비", JEC 잡지, 87호, 2014년 3월, pp. 89-91.
KEELBEMAN 상태 및 앞으로의 경로
에어버스는 지난 12월 CETMA를 방문하여 1m 실증기 구간의 최종 용접을 관람했으며, KEELBEMAN팀도 TRL(Technology Readiness Level)에 대한 최종 검토를 진행했다. "우리는 좋은 결과를 얻고 있으며 TRL 3에서 TRL 4로 기술을 발전시키고 있습니다."라고 Lagraña는 말합니다. 다음 단계에는 TRL 6으로의 추가 개발과 WP 2.3.2 전체 크기 하단 중앙 동체와 같은 Clean Sky 2의 시연기 중 하나에 설치될 전체 규모 용골 빔의 생산이 포함될 수 있지만 이는 아직 완료되지 않았습니다. 결정했습니다.
TPC 창 프레임용 WINFRAME 4.0 프로젝트
EURECAT의 또 다른 열가소성 합성물(TPC) 프로그램은 WINFRAME 4.0으로, 지역 항공기 동체/캐빈 통합 지상 실증기를 위한 24개의 창틀을 개발 및 제조하는 것을 목표로 합니다(지역 항공기 및 Full -규모의 혁신적인 동체 및 객실 시연기 아래에). WINFRAME 4.0 파트너는 다음과 같습니다.
<울>
다국적 항공우주 기업 Leonardo (이탈리아 로마) 주제 관리자로
유어캣
소피텍.
"우리가 사용하는 방법은 10분마다 하나의 창틀을 생성할 수 있습니다."라고 Lagraña는 말합니다. 생산 단계에는 오븐에서 TPC 라미네이트 블랭크 가열, 금형으로 변환, 프레스에서 금형 닫기, 10-20분 동안 열 및 압력 적용 및 완성된 부품 탈형이 포함됩니다. "이 접근 방식은 액체 성형보다 사이클이 짧을 뿐만 아니라 툴링 비용도 훨씬 저렴합니다."라고 그는 덧붙입니다. "공정은 자동차 산업에서 잘 알려져 있으며 부품의 품질을 높이는 고도로 자동화된 구성의 압축 성형이지만 사용되는 항공우주 재료는 다릅니다. 이 경우 탄소 섬유 강화 PPS와 Toray의 탄소 섬유 고급 복합 재료(이전 TenCate). 이 프로젝트가 끝나면 이러한 기술에 대해 TRL 6을 달성할 것입니다.”라고 Lagraña는 말합니다.
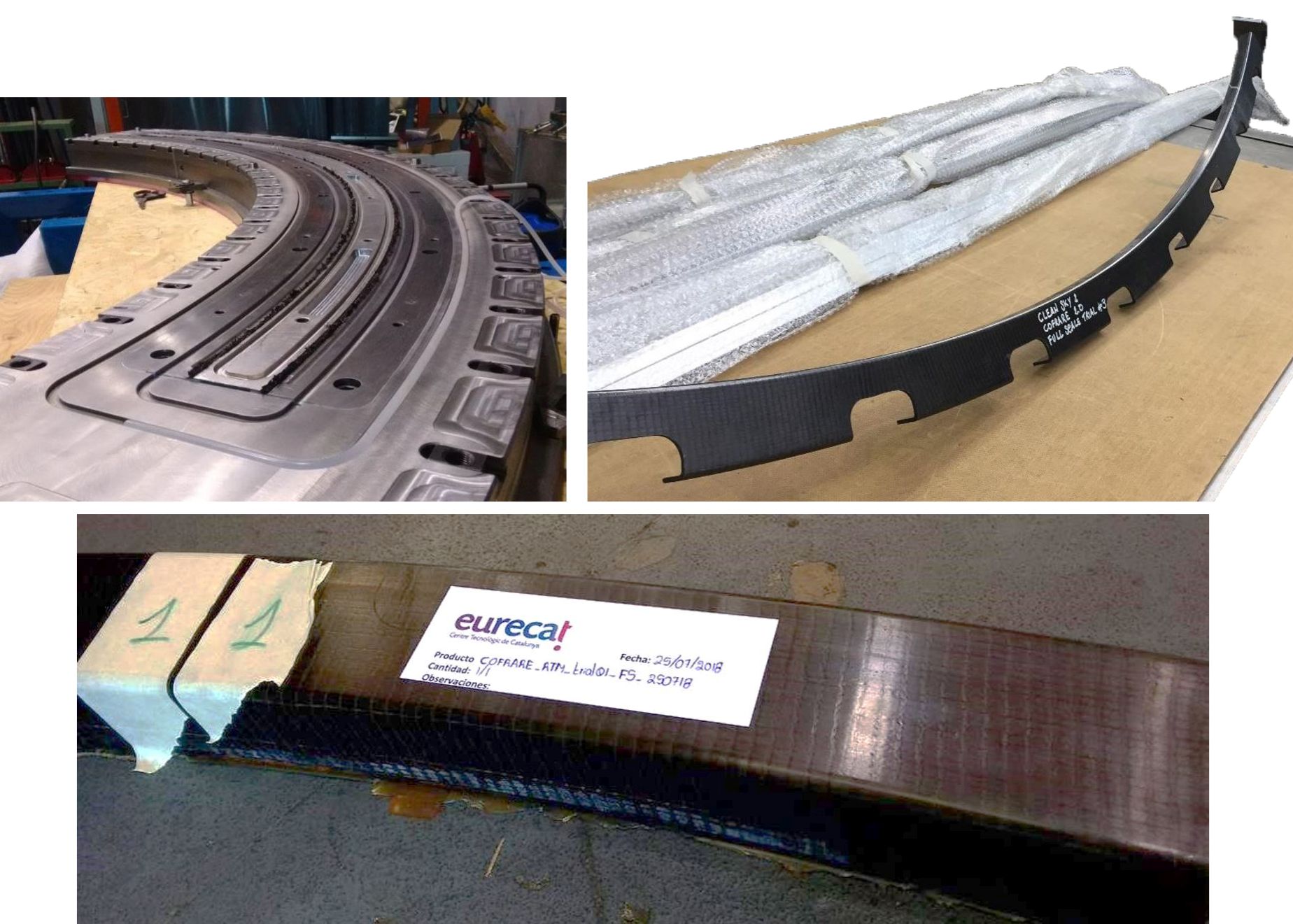
COFRARE 프로젝트:RTM C-프레임 및 열가소성 전단 타이
COFRARE 2020 프로젝트는 초기 COFRARE 2.0 프로젝트의 확장입니다.
클린 스카이 2 - JTI-CS2-2015-CFP02-AIR-02-16. "높은 생산율과 낮은 비용으로 복합 프레임 제조를 위한 공정 개발 " 프로젝트 기간:2016년 ~ 2018년.
Clean Sky 2 COFRARE 2.0 프로젝트의 목표는 지역 항공기용 합성 패널 기반 동체에 사용할 탄소 섬유 합성 프레임에 대한 경쟁력 있고 실현 가능한 제조 프로세스를 개발하는 것이었습니다. 포함된 파트너:
<울>
나폴리에 위치한 Tier 1 항공우주 공급업체 및 엔지니어링/산업화 회사 DEMA (Design Manufacturing SpA, Somma Vesuviana, 이탈리아)
유레캣
Appplus+ Laboratories의 한 부서인 LGAI Technological Center S.A. 스페인 바르셀로나에서 테스트를 제공했습니다.
차세대 COFRARE 2020 프로젝트의 목표는 Clean Sky 2 동체/캐빈 통합 지상 실증기에 사용할 본격적인 합성 프레임 및 전단 타이를 제조하는 것입니다. 이 시연기는 Clean Sky 2의 지역 항공기 IADP(Innovative Aircraft Demonstrator Platform)에 구성되어 있으며 2015년 3월 공동 기술 프로그램 문서의 섹션 5.2.2에 자세히 설명되어 있습니다.
“지역 항공기는 Clean Sky의 핵심 요소입니다. 전용 ITD(Integrated Technology Demonstrator) - 그린 지역 항공기(GRA)를 통해 , 환경을 존중하고 안전하고 원활한 이동성을 보장하며 유럽에서 산업 리더십을 구축하는 항공 운송 시스템을 위한 필수 구성 요소를 제공합니다. 클린 스카이 2에서 , ... 지역 항공기 IADP의 시연 목표는 현재의 Clean Sky 보다 훨씬 더 복잡하고 포괄적이며 도전적입니다. GRA 프로젝트 , 예산과 시간 제약 내에서 일하도록 강요받았습니다. …”
2015년 합동 기술 프로그램(Joint Technical Program)은 2개의 비행 테스트 베드와 5개의 대규모 통합 지상 실증기를 포함하는 지역 항공기 개발의 개요를 설명합니다. 후자는 전면적인 혁신적인 동체 및 객실 시연기를 포함합니다. :“동체는 복합 재료, 구조 및 제조를 위한 기술의 전면적인 시연이 될 것입니다. (영향 제로를 향하여) 수명 주기 전반에 걸쳐 에코 디자인 및 에너지 소비 최적화를 통해 무게와 비용 절감을 [달성]하고 환경 영향을 최소화하는 것을 목표로 하고 있습니다."
COFRARE 2020 프로젝트 파트너는 다음과 같습니다.
<울>
레오나르도 주제 관리자로서
유어캣
DEMA
항공기 부품 및 조립품 제조 A. 아베테 (놀라/마릴리아노, 이탈리아).
"COFRARE 2020에서 우리는 RTM(수지 이송 성형)을 사용하여 동체 프레임을 만들고 있으며, 이는 동체 시연기에 통합될 것입니다."라고 Lagraña가 설명합니다. "우리는 수지 주입에 적합한 프리폼을 생산하는 Shikibo(일본 오사카)의 Ziplus 기술을 사용하고 있습니다." Shikibo Ltd.는 Composite Alliance Corp.(미국 텍사스주 댈러스)에 속해 있으며 다양한 섬유 예비 성형 기술을 제공합니다.
이 프로그램의 흥미로운 측면 중 하나는 수지 도착, 온도, 압력, Tg 및 경화의 실시간 모니터링을 위해 Synthesites(Uccle, Belgium)의 센서를 사용한다는 것입니다. "센서는 합성 부품의 특정 영역과 RTM 도구에 위치하여 수지 주입 전략을 최적화합니다."라고 Lagraña는 말합니다. 주입은 또한 Composite Alliance Corp의 일부인 ISOJET(Corba, France)에서 제공하는 고도로 자동화된 시스템을 사용하여 이루어집니다. 합성 센서는 유전 센서이지만 교류(AC)를 기반으로 하는 대부분의 유전 분석(DEA)과 다릅니다. , 합성은 직류(DC)를 사용합니다. "우리 센서는 수지와 같은 고저항 재료에서 잘 작동하며 단일 전압을 적용하기 때문에 여러 주파수를 분석할 필요가 없지만 경화가 끝난 후에도 높은 정확도를 달성합니다."라고 Synthesites의 이사인 Dr. Dr. 니코스 판텔리스.
"우리는 2011년 SAMPE 회의에서 Synthesites를 만났습니다."라고 Lagraña는 회상합니다. “그들은 경화 주기를 단축하는 센서에 대해 이야기했습니다. 우리는 동체 프레임을 위한 프리폼을 자동화하는 방법과 HP-RTM(고압 RTM)으로 더 빠른 처리를 사용하는 방법을 모색하고 있지만 여전히 3-4시간의 처리 시간에 있습니다. 그러나 Synthesites를 사용하여 Tg를 모니터링하여 경화 주기를 50% 단축했습니다. 우리는 지금 속성을 테스트하고 있습니다. 이 센서는 고압에서 작동할 수 있지만 RTM 처리에서는 8bar의 압력만 사용합니다.”
Synthesites DC 유전체 센서, OptiFlow 액체 수지 흐름 모니터링 시스템 및 OptiMold 경화 모니터링 시스템은 다양한 윈드 블레이드 제조업체에서 생산 시연되었습니다. 그들은 또한 Bombardier Aerospace(영국 벨파스트)에서 현재 Airbus 220인 C-시리즈용 액체 복합 성형 날개를 생산하는 데 사용됩니다. 오토클레이브 프리프레그 및 RTM, National Composites Center(NCC, Bristol, UK)는 반응성이 높은 수지의 경우에도 수지 온도 및 저항의 센서 측정으로 이루어진 실시간 Tg 계산이 경화된 패널에서 측정한 Tg만큼 정확하다는 것을 입증했습니다. 시차주사열량계(DSC) 사용.
TPC 전단 타이로 프레임 결합
COFRARE 2020의 또 다른 핵심 부분은 RTM 동체 C-프레임을 합성 동체 패널에 결합하는 데 필요한 수백 개의 전단 타이 및 브래킷을 생산하는 보다 많은 양의 생산 방법입니다. Lagraña는 "압축 성형으로 생산된 열가소성 복합재 브래킷을 위해 255가지 다른 형상을 개발 중입니다."라고 말합니다. (GKN Fokker는 대형 여객기 IADP의 다기능 동체 데모용 TPC 브래킷을 생산할 여러 Clean Sky 2 프로젝트를 가지고 있습니다. COFRARE 2020의 이 작업은 더 작은 지역 항공기를 위한 것입니다.) 기본 방법은 일치하는 강철 도구와 가열 프레스를 사용하여 아래에 나와 있습니다. "이러한 압축 성형 도구의 비용은 2,000유로에 불과하며 RTM 도구에 비해 매우 저렴합니다."라고 그는 덧붙입니다. "스탬핑은 또한 매우 짧은 주기 시간을 달성합니다."
EURECAT은 복합 재료 기술 개발의 최전선에 남아 있기 위해 투자하고 있다고 Lagraña는 말합니다. “우리는 깨끗한 환경에 대한 압력이 모든 운송에서 복합 재료의 사용을 극적으로 증가시킬 것이며 경제성과 성능이 함께 갈 것이라고 믿습니다. 이것이 우리가 고객에게 제공할 자동화된 오토클레이브 외부 기술에 집중하는 이유입니다.”
Clean Sky 2 STUNNING 및 MECATESTERS 프로젝트에 대한 내 블로그를 계속 지켜봐 주시기 바랍니다. 이 블로그에서는 다기능 동체 데모용 용접 TPC 브래킷의 개발과 이 프로젝트를 위한 PAEK의 전체 특성에 대해 논의할 것입니다. 또한 합성물 분야에서 CETMA의 더 많은 개발과 함께 Synthesites에 대해 더 자세히 블로그에 글을 남길 것입니다. 2020년은 복합 재료에 있어 매우 흥미로운 해가 될 것입니다!