열가소성 복합재 용접의 새로운 지평
이 블로그는 2018년 9월 특집 "열가소성 복합재 용접"과 함께 합니다. 유도 용접 개발 일정과 미래 상용 항공기 자격에 대한 세부 정보, 수리, 자동차 및 열경화성 열가소성 수지(TS) 개발에 대한 짧은 섹션을 포함하여 인쇄 기사에 맞지 않는 이미지와 세부 정보 모음입니다. -TP) 용접.
용접된 열가소성 복합재(TPC) 어셈블리가 항공우주 및 자동차 경량 구조 모두에 관심이 있는 이유를 반복하기 위해 Airbus A320 후방 압력 격벽 아래의 두 이미지를 비교하십시오. 상단 이미지는 알루미늄으로 만든 현재 버전입니다. 많은 수의 리벳에 주목하십시오. 이제 이를 베를린에서 열린 2018 ILA 에어쇼에서 Premium Aerotec에서 선보인 용접 TPC 데모와 비교해 보십시오. 리벳이 없는지 확인하십시오. 복합 재료의 경우 이는 패스너의 무게, 시간 및 비용을 없앨 뿐만 아니라 구멍을 배치하고 드릴링하고 구멍을 청소하고 검사하는 시간과 비용을 제거합니다. 또한 하중을 견디는 섬유를 통해 절단을 오프셋하는 데 필요한 라미네이트 패드 업이 없는 훨씬 가벼운 구조를 의미합니다.
용접된 열가소성 합성물 A320 후방 압력 격벽(하단)은 현재 알루미늄 구조(상단)에 비해 리벳이 없는 솔루션을 제공합니다.
출처:RUAG(상단) 및 Premium Aerotec(하단), 경량 생산 기술을 위한 DLR 센터(독일 아우크스부르크)
TPC 재료 공급업체 TenCate-Toray Group의 열가소성 복합 재료 R&D 및 제품 개발 이사인 Dr. Hans Luinge는 "또 다른 이점은 용접 구조에 대한 검사가 접착 결합된 어셈블리보다 더 쉽다는 것입니다."라고 말합니다. “C-스캔은 잘 작동하여 라미네이트에 다공성이 없는지 보여줍니다. 이는 용접이 양호함을 의미합니다. 접착식으로 결합된 구조의 경우 감지하기 어려운 키스 결합 또는 오염 물질이 있을 수 있습니다.” TenCate-Toray는 용접 기술 자체를 개발하지 않지만 다양한 산업 및 고객 프로젝트를 지원합니다. Luinge는 "필요에 따라 재료를 최적화하고 TAPAS와 같은 노력과 KVE Composites, TPRC, 계층 공급업체 및 OEM과 같은 파트너와의 오랜 참여를 바탕으로 올바른 방향으로 개발을 주도하도록 돕습니다."라고 말합니다.
유도 용접 개발
KVE Composites는 2001년부터 TPC용 유도 용접을 개발했습니다. 초기 응용 분야에서는 Gulfstream G650 및 Dassault Falcon 5X 비즈니스 제트 항공기용 엘리베이터 및 방향타를 포함하여 탄소 섬유 직물/PPS 라미네이트를 사용했습니다.
KVE 복합 재료가 도움이 됨 GKN Fokker의 Gulfstream G650(오른쪽) 및 Dassault Falcon 5X 항공기용 유도 용접 엘리베이터 및 방향타(왼쪽) 생산을 개발하기 위해.
출처:KVE Composites, GKN Fokker(왼쪽) 및 Gulfstream(오른쪽).
기타 유도 용접 TPC 응용 분야에는 AVIACOMP S.A.S.에서 생산한 연료 탱크 액세스 도어가 포함됩니다. (프랑스, Launaguet 및 현재 Sogeclair Group의 일부) Airbus A220 날개(이전 Bombardier CSeries)용. (Aviacomp는 2017년 파리 에어쇼에서 선보인 STELIA의 용접 TPC 동체용 스트링거도 생산했습니다.)
Aviacomp는 유도를 사용합니다. KVE Composites가 Airbus A220 내로우바디 항공기용 TPC 연료 탱크 접근 도어를 생산할 때 개발한 용접 기술.
출처:Sogeclair Group의 Aviacomp.
이 일반적인 범주의 액세스 도어는 KVE Composites가 완료한 설계 및 제조 연구에서 볼 수 있듯이 TPC 용접이 비용을 절감할 수 있는 기회입니다. 더 작은 항공기라도 이러한 액세스 패널을 최대 60개까지 가질 수 있으며, 모두 모양이 다르며 일반적으로 가공된 벌집형 코어가 있는 복합 샌드위치 구조를 사용하여 만들어집니다. KVE Composites 상무이사인 Harm van Engelen은 "용접된 열가소성 어셈블리를 사용하면 단 $100,000의 툴링 비용으로 항공기용 액세스 패널을 모두 만들 수 있어 상당한 절감 효과를 얻을 수 있습니다."라고 말했습니다. “우리는 코어를 가공할 필요가 없습니다. 평평한 시트와 스탬핑된 보강재와 같은 '레고 같은' 구성 요소를 사용하여 다양한 모양을 형성하기만 하면 됩니다. 또한 우리의 도구는 용접 지그에 가깝기 때문에 오늘날 사용하는 것에 비해 상대적으로 비용이 저렴합니다. 항공기의 모든 액세스 패널은 단일 용접 셀에서 만들 수 있습니다.”
항공기 오버행 패널용 용접된 열가소성 어셈블리 자동 성형 및 용접 셀을 사용하여 제작 도구 비용을 $100,000 절약하십시오. 출처:KVE 합성물.
KVE Composites는 아래 일정에 나와 있는 것처럼 TPC 용접 기술의 개발을 계속하고 있습니다. 2019년 하단에 표시된 생산 셀은 GKN Fokker가 개발한 초음파 용접 엔드 이펙터를 사용하여 Boikon(Leek, The Netherlands)에서 생산한 Falko ATL(자동 테이프 부설) 기계입니다. R&D Maarten Labordus의 KVE Composites 대표는 "이 로봇 셀은 현재 사용되는 픽 앤 플레이스 방식과 비교하여 다음 단계의 대량 TPC 부품 생산을 위한 보다 효율적인 프로세스 및 제어 시스템을 가능하게 합니다."라고 설명합니다. "예를 들어, 지역 제트 제어 표면(약 60mm x 3m)에 대한 스킨 및 리브 라미네이트를 완전 자동 레이업하고, 오토클레이브 외부 통합 및 성형 단계를 적용한 다음, 조립을 완료할 수 있습니다. 인접한 용접 셀." Falko ATL 기계는 또한 초음파 용접을 위해 GKN Fokker가 이미 개발한 폐쇄 루프 제어를 보여줍니다. GKN의 Aerostructures R&T 책임자인 Arnt Offringa는 "이 기계는 재료 유형, 두께 및 모양별로 필요에 따라 에너지 수준을 제어할 수 있지만 나중에 완성된 TPC 부품을 성형하는 동안 평평한 프리폼의 완전한 용융 통합이 필요합니다"라고 설명합니다. 포커.
출처:KVE 합성물 자격
2017년의 핵심 개발 이니셔티브로 위에 표시된 자격 TPC 항공구조물에 대한 유도 용접 공정은 지속적인 우선 순위입니다. 4
에서 열리는 KVE Composites의 발표에 대한 초록에 따르면 국제 회의 및 Thermoplastic Composites 전시회(ITHEC, 독일 브레멘에서 2018년 10월 30-31일)에서 지난 몇 년 동안 열가소성 복합 재료(TPC) 용접은 PPS 및 PEI와 같은 폴리머에서 PEEK와 같은 고급 폴리머로 이동하는 것을 보았습니다. , PEKK 및 현재 Low Melt PAEK(LM PAEK, 내 블로그 "PEEK vs. PEKK vs. PAEK ..."에서 자세히 읽어보기) 뿐만 아니라 자동으로 배치된 UD 테이프 및 더 많은 하중을 받는 구조를 위한 더 두꺼운 라미네이트에 대한 것입니다. 이에 대한 대응으로 KVE Composites는 FEA 기반 시뮬레이션 모델뿐만 아니라 도구 및 장비를 개선하고 표준화하기 위해 노력했습니다.
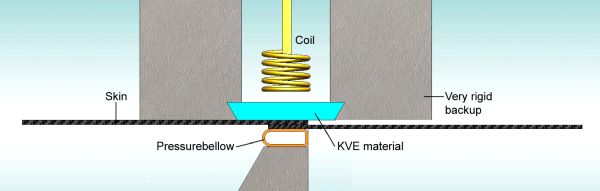
신소재를 사용한 유도 용접의 인증을 위한 표준화된 설정.
출처:KVE 합성물
이러한 새로운 복합재 라미네이트로 유도 용접 프로세스의 성숙 및 자격을 지원하기 위해 KVE 복합재는 단일 랩 전단 및 L 및 T 풀오프 테스트 쿠폰 용접을 위한 표준화된 설정을 개발했습니다. 이 설정에는 다음이 포함됩니다.
<울>
용접하는 동안 라미네이트에 압력을 가하여 하중을 받는 견고한 프레임입니다.
표준 패널의 재현 가능한 용접을 허용하기 위해 프레임 아래에 배치할 수 있는 하부 도구 블록입니다.
용접 시 열을 제한하기 위해 특수 방열판(위 그림의 "KVE 재료")에 대해 용접되는 라미네이트를 압축하기 위해 한 방향으로만 확장될 수 있는 하부 도구 블록의 팽창식 맨드릴(위 그림의 압력 벨로우즈) 인터페이스.
하단 도구 블록을 교환하여 다양한 표준 쿠폰을 용접한 다음 초음파로 검사한 후 더 작은 쿠폰을 절단하고 기계적으로 테스트할 수 있습니다. 이 표준화된 설정은 다음에서 이미 설치했습니다.
<울>
열가소성 연구 센터(TPRC, Enschede, 네덜란드)
사우스 캐롤라이나 대학교 McNair 센터(미국 사우스캐롤라이나주 콜럼버스)
네덜란드 항공우주 센터(NLR, Marknesse, The Netherlands).
표준화된 유도 용접 KVE에서 설정(왼쪽) 및 용접선에서 온도를 기록하기 위해 열전대가 있는 용접된 UD 탄소 섬유/PEKK 샘플(오른쪽).
출처:KVE 합성물.
수리
또 다른 주요 개발 영역은 TPC 항공기 구조를 수리하는 방법입니다. "우리는 먼저 자격을 갖춘 CF 패브릭/PPS 구조에 초점을 맞추고 있습니다."라고 Labordus는 말합니다. “공정은 기본적으로 열경화성 복합재 수리에 사용되는 것과 동일합니다. 손상된 재료를 제거하고 테이퍼 스카프로 해당 영역을 준비한 다음 프리프레그 수리 패치로 접착합니다. Labordus는 문제 중 하나가 실온에서 열가소성 프리프레그가 딱딱하고 달라붙지 않아 "기하학적 형상을 맞추기가 어렵다"고 말합니다. 그러나 그는 Airbus, Lufthansa 및 기타 업체에서 개발 중인 로봇 수리 시스템이 솔루션을 제공한다고 믿습니다.
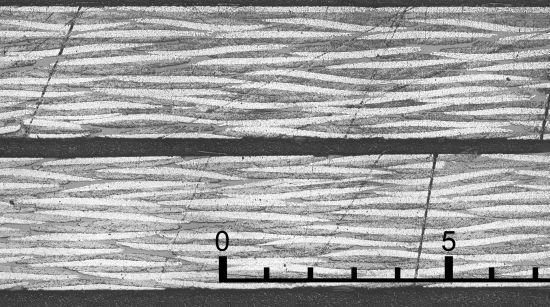
용접된 구조용 열가소성 복합 재료 수리의 지속적인 개발의 일환으로 KVE Composites는 균일한 두께와 90%의 고유 재료 특성을 가진 CF 직물/PPS 라미네이트에서 유도 용접된 2D 선형 테이퍼 조인트를 달성했습니다.
출처:KVE 합성물.
이러한 시스템은 계측을 사용하여 로봇으로 가공된 테이퍼 스카프를 정밀하게 측정한 다음 일치하도록 로봇으로 테이퍼 가공된 미리 만들어진 패치를 접착합니다. Labordus는 "유도 용접을 사용하여 열가소성 패치를 원래 구조에 용접하기를 원하지만 아직 해결해야 할 문제가 있습니다. “부품과 패치의 모양에 따라 와전류가 모든 곳에서 형성되지 않기 때문에 차가움이나 과열 영역이 생길 수 있습니다. KVE Composites는 이를 통해 균일한 두께와 완벽한 용접으로 CF 패브릭/PPS 라미네이트에서 2D 선형 테이퍼 조인트를 달성할 수 있었습니다. "우리는 처녀 재료 속성의 10% 이내였습니다."라고 Labordus는 말합니다.
다음 단계는 각각 스카프 가장자리가 있는 두 개의 직사각형 부품을 유도 용접한 다음 테이퍼 스카프로 원형/타원 구멍에 테이퍼 패치를 용접하는 것입니다. 이는 본질적으로 열경화성 복합재 수리에 사용되는 방법입니다. "만약 그것이 효과가 있다면 우리는 PEEK와 PEKK로 만든 UD 라미네이트로 이동할 것입니다."라고 Labordus는 말합니다. 그는 유도 코일을 사용하여 현장에서 수리하는 시스템이 아직 시연되지 않았지만 "실험실에서는 할 수 있습니다"라고 말합니다. 또 다른 문제는 보수 패치와 테이퍼 표면 사이에 충분히 밀착되도록 압력을 가하는 방법입니다. “현재 실험실 도구에 사용되는 압력은 5bar입니다. 진공 백만으로 충분한 압력인지는 모르겠지만 더 평평한 UD 소재를 사용하면 진공 백에서 1bar만 사용해도 괜찮을 것입니다.”
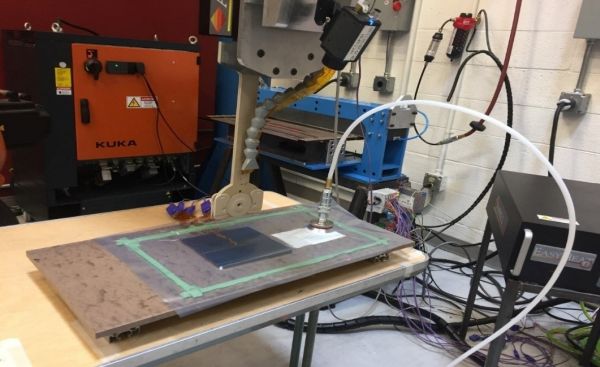
미래의 현장 열가소성 복합재 수리를 가능하게 하는 진공 백 아래의 유도 용접은 사우스 캐롤라이나 대학 McNair 센터의 Michel van Tooren과 그의 팀에 의해 개발되고 있습니다. 출처:미셸 반 투렌.
KVE 복합 재료의 이 작업은 사우스 캐롤라이나 대학교(미국 사우스캐롤라이나주 컬럼비아) McNair 센터의 일부인 SmartState Center for Multifunctional Materials and Structures의 책임자인 Michel van Tooren에 의해 확장되고 있습니다. "우리는 진공 백 아래에서 열가소성 복합 재료를 유도 용접하고 있습니다. 이는 오늘날 핫 본더와 열 블랭킷을 사용하여 현장 복합 재료 수리가 수행되는 방식과 매우 유사합니다."라고 그는 설명합니다. “진공 백은 두 부분을 압축하기 위한 부드러운 도구처럼 작동합니다. 유도 전류를 적용하고 용융 수선을 달성합니다. 프로세스 경계와 매개변수만 정의하면 됩니다. 어떤 면에서는 열경화성 수지 수리보다 더 쉽습니다. 필요한 경우 수리를 다시 녹일 수 있기 때문입니다. 세계 반대편에서나 20년 동안 서비스를 받은 후에도 마찬가지입니다. 그리고 그 결과 접착 결합이 아니라 응집 부품이 생성되므로 결합과 관련된 모든 문제를 제거하고 열경화성 수리에서 결합이 양호한지 확인하는 방법을 알 수 있습니다.” 그는 또한 현재 개발 중인 자동화된 로봇 수리 기술로 "유도 용접 수리가 비교적 간단할 것"이라고 믿습니다.
열가소성 용접에 대한 열경화성
Van Tooren은 또한 열경화성 및 열가소성 복합 재료를 접합하기 위한 유도 용접을 개발하고 있습니다. "우리는 열경화성 복합 재료에 열가소성 수지를 도입하지만 용접하려는 부분에만 적용됩니다."라고 그는 설명합니다. “우리는 나노입자에 이식하고 약간의 교차 중합을 합니다. 그 결과 열경화성 복합 재료에 주입되고 화학적으로 함께 용융된 열가소성 수지 섬이 생성됩니다. 그런 다음 열가소성 섬에 용접할 수 있습니다.” 다시 말하지만, 비전은 드릴링 구멍과 기존의 접착 결합과 관련된 문제를 피하는 복합 재료 결합 및 조립을 위한 대체 방법입니다.
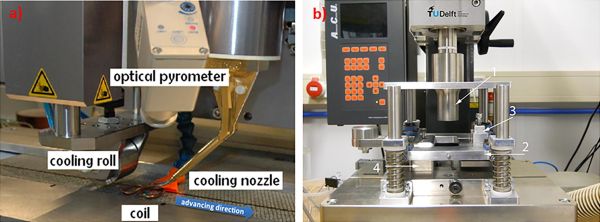
용접 전 PVB 열가소성 커플링 레이어를 통한 TSC-TSC 조인트의 개략도(상단). 유도 용접(왼쪽) 및 초음파 용접(오른쪽)의 설정(아래).
출처:"CF/에폭시 기반 복합 재료의 하이브리드 용접".
열경화성 복합재(TSC) 라미네이트와 TPC 라미네이트의 용접(또는 TS-TP 용접)은 여러 연구 기관에서 추진하고 있습니다. 인쇄 기사에서 TPC의 연속 초음파 용접 개발의 리더로 언급된 TU Delft의 Irene Fernandez Villegas는 "탄소 섬유 강화 에폭시 기반 복합 재료의 하이브리드 용접"이라는 제목의 2017년 논문을 Francesca Lionetto와 함께 공동 저술했습니다. 살렌토 대학(이탈리아 레체), CETMA Composites의 실비오 파파다(이탈리아 브랜디시) 등 기본 사항은 다음과 같습니다.
<울>
Polyvynilbutyral(PVB)은 150-170°C의 용융 온도를 갖는 반결정질의 저가 열가소성 중합체로, 우수한 결합 및 필름 형성 능력 및 여러 표면에 대한 접착력을 특징으로 합니다.
PVB(Mowital, Kurakay에서 공급)를 결합층으로 사용하고 14겹 탄소 섬유 직물/에폭시 TSC 라미네이트(58% 섬유 부피 함량 및 180% 섬유 부피 함량을 갖는 Hexcel 3501-6 프리프레그 °C 경화).
PVB 결합 층과 CF/에폭시 복합재 사이의 거시적 기계적 연동은 동시 경화 및 공동 경화 동안 TSC의 첫 번째 층(일반적으로 두께가 10에서 수백 마이크론 사이)으로 PVB 수지의 부분적인 침투를 통해 달성되었습니다. PVB 열가소성 필름으로의 에폭시 단량체의 확산
유도 용접 및 초음파 용접 공정은 적절하게 강한 용접 조인트를 생성했으며, PVB 커플 링 레이어를 통해 용접된 결과 CF/에폭시 대 CF/에폭시 조인트는 랩 전단 강도가 ≈25 MPa의 일반적인 범위 내에 있음을 나타냅니다. CF/에폭시 접착 접합부의 강도 값
자동차
열가소성 용접 인쇄 기사에 포함된 거의 모든 회사는 자동차 및 항공우주 응용 분야를 고려하고 있습니다. GKN Fokker의 Offringa는 "용접은 복합 재료를 알루미늄에 비해 경쟁력 있게 만드는 데 도움이 됩니다. “자동차는 또한 접합에 대한 빠른 대안으로 용접을 고려하고 있습니다. 우리는 복합 재료의 빠른 처리에 관해 여러 자동차 회사와 이야기를 나눴습니다." 그는 탄소 섬유 복합재 자동차 차체가 대부분 열경화성이며 지정된 두께의 접착제로 접착된다고 지적합니다. "열가소성을 사용하여 이러한 부품을 만들 수 있다면 조립품을 용접하여 구성 요소 사이의 간격을 제거하고 더 단단한 본체 구조를 만들 수 있으므로 무게, 비용 및 성능상의 이점이 있습니다."
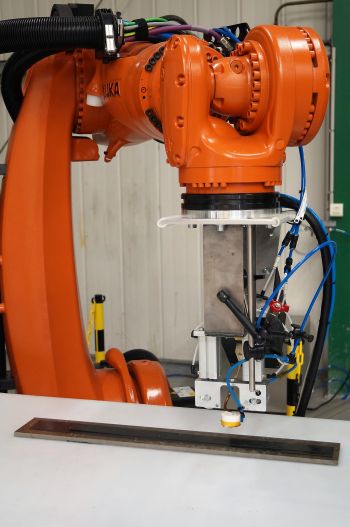
복합 무결성의 동적 유도 용접 프로세스 설정.
출처:복합 무결성.
Composite Integrity의 비즈니스 개발 관리자인 Jérôme Raynal도 가능성을 보고 있습니다. 그의 회사는 STELIA Aerospace와 협력하여 2017년 파리 에어쇼에서 공개된 TP 시연기에서 CF/PEKK UD 테이프 스트링거 및 동체 스킨을 결합하는 데 사용되는 동적 유도 용접 프로세스를 개발했습니다. "우리는 폴리아미드[PA, 나일론] 및 폴리프로필렌[PP] 복합 재료를 사용하여 자동차용 저항 용접을 개발했습니다."라고 Raynal은 말합니다. “우리는 이를 위한 다양한 기술을 보유하고 있습니다. 예를 들어, 금속 와이어를 한 부품에 내장하고 다른 부품과 접촉시켜 전류를 주입할 수 있습니다. 또한 용접 인터페이스에 탄소 섬유 저항 패치를 배치하여 필요한 용접 열을 생성할 수 있습니다.” 한 개발에서는 CF/PA로 만든 두 구성 요소를 동일한 폴리머와 유리 섬유 플리스로 만든 특수 설계된 저항성 패치를 사용하여 용접하여 인접한 라미네이트를 전기적으로 절연하고 웰드라인에 에너지를 집중시켰습니다. 자동차 부품에 매우 일반적으로 사용되는 금속 인서트는 어떻습니까? "금속 인서트가 있는 부품은 저항 용접에 문제가 없으며 유도 용접을 사용하면 특수 설계된 코일을 사용하거나 다른 방식으로 전자기장 및 전류를 수정할 수 있습니다."라고 Raynal은 대답합니다. "이것은 개발되어야 하지만 항공기 구조의 자동화 생산에 대해 이미 시연한 것과 유사합니다."
추가 개발 및 기타 프로젝트
오프닝 이미지에 대한 한 가지 참고 사항. 초음파 용접을 사용하여 DLR Center for Lightweight Production Technology(DLR ZLP, Augsburg, Germany)에서 개발한 자동화 프로세스의 CAD 렌더링을 보여줍니다. KUKA Quantec KR210 산업용 로봇을 타고 A320형 항공기의 후방 압력 격벽(RPB)에 8개의 TPC 섹션을 결합합니다. 함께 제공되는 TPC 용접 기사에서 DLR ZLP의 저항 용접 개발에 대해 논의했습니다. 베를린에서 열린 2018 ILA 에어쇼에서 전시된 프리미엄 에어로텍의 A320 RPB 시연기에 사용된 방법입니다. DLR ZLP의 조립 및 접합 기술 그룹 관리자인 Lars Larsen에 따르면 "'용접 브리지'를 사용하는 저항 용접 프로세스와 병행하여 로봇 작동식 초음파 용접 헤드도 개발했습니다. 우리는 관련 용접 공정 매개변수를 결정하기 위한 예비 테스트를 완료했으며 다음 달에 우리는 로봇에 초음파 용접 엔드 이펙터의 통합을 개선할 것입니다. 우리의 목표는 열가소성 합성물을 사용하여 만든 항공기 동체 스트링거와 후방 압력 격벽을 모두 용접하기 위한 단일 산업 공정을 개발하는 것입니다.”
이번에 다룰 기회가 없었던 다른 프로젝트로는 EireComposites와 Ybridio 및 Innova 프로젝트에 참여하여 비용을 절감하고 자동화를 향상시키기 위해 용접 가능성을 추구하는 프로젝트가 있습니다. 이 회사는 CF/PEEK, CF/PEKK 및 GF/PP 합성물에 대한 유도 용접 및 저항 용접 기능을 보고하며 Bombardier CSeries(현재 Airbus A220) 날개에 대해 열가소성 용접이 평가되었다고 보고합니다.
현재 Unitech Aerospace의 일부인 Tods Aerospace는 금속 내장 임플란트를 사용하지 않는 저항 용접 기술의 개발을 살펴보는 Rolls-Royce가 후원하는 NATP(National Aerospace Technology Exploitation Program)에 참여했습니다. TenCate-Toray와 National Composites Center(영국 브리스톨)도 파트너였습니다.
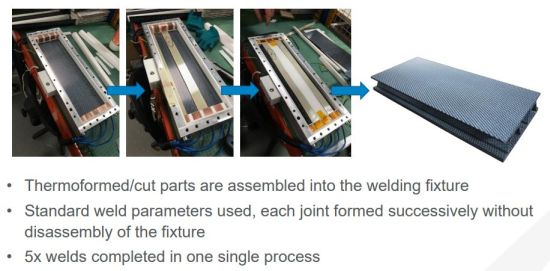
이 공정 시연자는 모자 강화 TPC 구조를 제조하는 방법을 탐구했습니다. 출처:Unitech Aerospace(섹션 6, p. 39에서 시작)
가까운 장래에 열가소성 복합 재료의 레이저 용접으로 Laser Zentrum Hannover(LZH)의 개발을 다룰 계획이므로 계속 지켜봐 주십시오.
출처:LZH 레이저 Zentrum Hannover eV