방전 가공(EDM) :원리, 작동, 장점 및 단점
방전 가공(EDM)은 재료 제거 또는 제조 기술입니다. 1770년 Joseph Priestly에 의해 처음 소개되었습니다. 그러나 기술과 장비의 현대화와 함께 이 기술은 이제 컴퓨터 수치 제어(CNC)와 통합되었습니다. EDM 프로세스에는 열 에너지를 사용하여 물체에서 과도한 재료를 제거하여 작업에 필요한 모양을 만드는 과정이 포함됩니다.
가장 널리 사용되는 CNC 가공 공정은 아닙니다. 그러나 엔지니어는 처리할 수 없는 부품을 만들기 위해 그것에 의존합니다. 과도한 재료를 제거하기 위해 기계적 힘이 필요하거나 사용하지 않습니다. 이것이 많은 사람들이 비 전통적인 제조 공정이라고 생각하는 이유입니다. 이 프로세스는 다양한 산업 분야에서 성형 및 가공을 용이하게 합니다. 이 기사에서는 작동 원리, 사용 가능한 다양한 유형, 장점 및 응용 프로그램을 연구합니다.
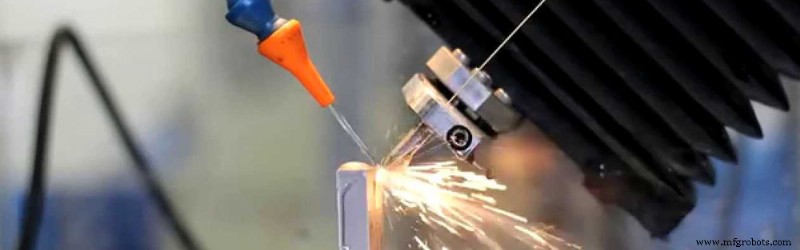
방전 가공(EDM) 개요
방전 가공(EDM)은 물질을 반복적으로 제어되는 방전에 노출시켜 제거하는 공정입니다. 열전 현상에 적합합니다. 전극/선과 워크 사이에 방전이 발생하면 워크에 열에너지가 발생합니다. 이것은 재료 층의 제거로 이어진다. 일반적으로 EDM은 Die-sink EDM, small fast hole EDM 및 wire-cut EDM의 세 가지 유형으로 나뉩니다. 그러나 현대 생산 공정에서 와이어 EDM 공작 기계는 CNC와 통합됩니다. 따라서 자동화된 EDM 기계는 업계에서 일반적으로 사용됩니다.
이것은 매우 정확한 프로세스이며 공작물에 도구를 사용하지 않습니다. 단단한 재료를 가공하거나 복잡한 모양을 형성해야 하는 경우 일반적으로 EDM이 최선의 선택입니다.
방전 가공은 어떻게 작동합니까?
정의가 간단해 보이지만 물리적 프로세스는 더 복잡합니다. 공작물에서 재료를 제거하기 위해 EDM을 사용하는 것은 전극 사이에서 일련의 반복적인 급속 전류 방전에 의해 달성됩니다. 이 전극은 유전체 유체를 사용하여 분리됩니다. 그런 다음 전압이 유전체 유체를 통해 전송됩니다. EDM 제조는 전도성 물질에만 적합합니다.
이 전극 중 하나는 정확한 목적에 맞게 모양을 변경하는 데 사용됩니다. 전극은 공작물 전극 또는 "양극"입니다. 가장 일반적으로 사용되는 전극 재료는 구리, 텅스텐 합금, 주철, 강철, 은 텅스텐 합금 및 흑연입니다. 다른 전극은 도구 전극 또는 "음극"입니다. 이 프로세스의 기본 원리는 제어된 전기 스파크로 재료를 부식시키는 것입니다. 이러한 이유로 두 전극이 서로 닿지 않아야 합니다.
공작물과 전극 사이에 펄스 형태로 전위차가 인가됩니다. 전극이 공작물에 접근함에 따라 전극 사이의 작은 간격에 존재하는 전기장이 증가합니다. 이는 고장 수준에 도달할 때까지 계속됩니다.
방전으로 인해 재료가 극도로 가열됩니다. 가열하면 재료의 일부가 녹습니다. 유전체 유체의 안정적인 흐름은 과잉 물질을 제거하는 데 도움이 됩니다. 액체는 또한 처리 중 냉각을 돕습니다.
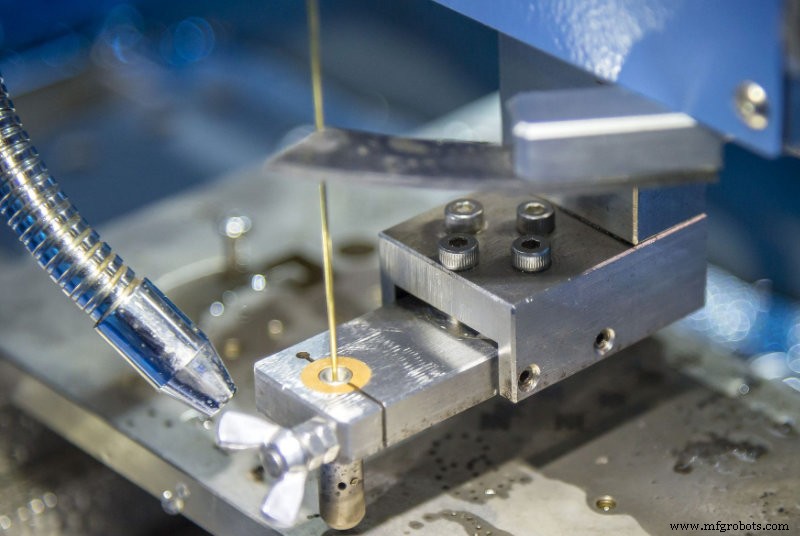
방전 가공 유형
EDM 프로세스는 독특하고 전통적입니다. 그러나 이것이 이 프로세스에 하나의 방법만 있다는 것을 의미하지는 않습니다. EDM에는 세 가지 유형이 있습니다. 이는 유형이 적합하지 않을 때 대안이 있는지 확인하는 데 도움이 됩니다. 다양한 유형의 방전 가공에는 다음이 포함됩니다.
와이어 EDM
와이어 침식 또는 스파크 EDM이라고도 하는 와이어 EDM은 널리 사용되는 공정입니다. 황동 와이어 또는 얇은 구리를 사용하여 공작물을 절단하는 작업이 포함됩니다. 여기에서 가는 와이어는 전극 역할을 합니다. 이 경우 유전체 액체는 일반적으로 탈이온수입니다. WEDM 처리 중 스풀은 자동 공급 장치에서 와이어를 지속적으로 푸는 데 사용됩니다.
워크와 전선에 의해 방전이 영향을 받을 수 있기 때문입니다. 따라서 절단에 새로운 배출 경로가 필요합니다. 이 방법은 매우 효과적입니다. 그러나 엔지니어는 와이어가 공작물을 완전히 통과해야 한다는 점에 주의해야 합니다. 따라서 기본적으로 3D 부품에 2D 컷을 생성합니다. 기존 CNC 가공 프로세스와 유사한 결과를 얻을 수 있습니다.
구멍 EDM
홀 EDM 공정은 EDM의 또 다른 유형입니다. 이름에서 알 수 있듯 빠르게 구멍을 뚫는 데 도움이 됩니다. 홀 방전 가공에 사용되는 전극은 관형으로 되어 있어 전극을 통해 유전체 유체가 쉽게 흐를 수 있습니다.
기존 드릴링 방법과 달리 홀 EDM은 매우 작은 깊은 홀을 처리할 수 있습니다. 또한 이러한 구멍에는 디버링이 필요하지 않습니다. 금속의 경도나 종류에 관계없이 이 공정은 기존 방법보다 더 빠르게 정밀한 구멍을 효과적으로 드릴링할 수 있습니다.
싱커 EDM
이것은 Ram EDM, 싱킹 다이 또는 캐비티 EDM으로도 알려진 전통적인 EDM입니다. 캐비티 유형, 다양한 주조 응용 분야(예:사출 성형)에 대해 복잡한 캐비티 모양을 생성할 수 있기 때문입니다.
이 프로세스는 사전 처리된 구리 또는 흑연 전극을 사용하여 원하는 모양의 "포지티브" 모양을 형성합니다. 그런 다음 전극을 공작물에 눌러 원래 재료 모양의 음극 필름을 만듭니다. 특정 요인은 EDM에서 전극 재료 선택에 영향을 미칠 수 있습니다. 여기에는 전극의 내식성 및 전도성이 포함되며 흑연은 일반적으로 구리보다 처리하기 쉽습니다. 그러나 구리가 더 강하고 유리합니다.
EDM의 장점 가공 :
기존의 절단 도구로 생산하기 어려운 복잡한 모양.
매우 엄격한 공차가 있는 매우 단단한 재료입니다.
매우 작은 공작물의 경우 기존 절단 도구는 과도한 절단 도구 압력으로 인해 부품을 손상시킬 수 있습니다.
공구와 공작물 사이에 직접적인 접촉이 없습니다. 따라서 미세한 부품과 약한 재료를 변형 없이 가공할 수 있습니다.
좋은 표면 조도를 얻을 수 있습니다.
아주 미세한 구멍을 뚫을 수 있습니다.
EDM의 단점 가공 :
재료 제거 속도가 느립니다.
연료유 기반 유전체 사용과 관련된 잠재적인 화재 위험
스탬핑/전기 해머 EDM용 전극을 만드는 데 추가 시간과 비용이 듭니다.
소비 전력이 매우 높습니다.
높은 전력 소비.
비전도성 재료는 특정 프로세스 설정을 통해서만 처리할 수 있습니다.
적용 EDM 가공
EDM은 특히 소량 생산에서 잘 알려져 있습니다. 방전 가공을 사용하여 다양한 공정을 수행할 수 있습니다. 이러한 프로세스에는 밀링, 터닝 및 작은 구멍 드릴이 포함됩니다. 이 고유한 프로세스는 자동차에서 항공우주 산업에 이르기까지 광범위한 산업에서도 유용합니다.
EDM은 독특하고 정확한 모양을 생성할 수 있어 다음 응용 분야에 도움이 됩니다.
사출 성형
작은 구멍 드릴링
다이캐스팅