시뮬레이션과 3D 프린팅 기술을 함께 사용해야 하는 이유
적층 제조 기술을 기존의 이전 기술과 비교할 때 예상해야 할 한 가지 문제는 대비되는 재료 특성의 차이입니다. 왼쪽 차트는 성능 기준에 대한 개요와 3D 프린팅과 CAE를 비교하는 방법을 제공합니다.
각 3D 프린팅 기술은 사출 성형 도구를 통해 생산된 구성 요소와 구별되는 레이어 접합 품질뿐만 아니라 다양한 기계적 및 열적 특성을 제공합니다. 재료가 열가소성이든 열경화성이든 관계없이 이러한 품질은 잠재적인 응용 기회 범위를 정의합니다.
FDM 3D 프린팅 기술 및 대중적인 소재
융합 증착 모델링 3D 인쇄 기술 진정한 열가소성 수지를 사용하는 특별한 이점이 있습니다. 이를 통해 엔지니어는 친숙한 생산 재료와 유사하게 작동하는 재료를 선택할 수 있습니다. 인기 있는 FDM 자료 폴리카보네이트 및 나일론 12와 같은 재료는 사전 생산 구성 요소에 사용할 수 있지만 3D 프린팅의 적층 품질은 테스트 시나리오에서 부품이 어떻게 작동하는지 구별하는 이방성 특성을 생성합니다.
시뮬레이션 기술로 가상으로 설계 성능 검증
여기에서 시뮬레이션이 예측 공허함을 채우고 나쁜 아이디어를 인쇄하는 것을 방지하는 데 도움이 됩니다. 물론, 나는 부드러운 도구로 틀을 짜거나 주조하는 것보다 나쁜 아이디어를 인쇄하는 편이 낫습니다. 3D 프린팅은 빠릅니다 비용은 줄었지만 설계 성능 평가를 중단하면 사실상 프린터에서 낭비되는 주기를 줄이는 데 도움이 되고 현장 성능에 대한 더 많은 통찰력을 얻을 수 있습니다.
생산 품질에 매우 가까운 도구 부품이 있는 경우에도 가상 테스트는 물리적 테스트에 비해 몇 가지 뚜렷한 이점이 있습니다. 특히, 사과와 사과 디자인을 진정으로 비교할 수 있는 완벽한 "소음" 없는 환경입니다. 또한 시뮬레이션을 통해 물리적으로 정량화하는 데 방해가 되거나 비용이 많이 드는 유체 흐름 또는 응력과 같은 양을 시각화할 수 있습니다.
물리적 테스트와 가상 테스트 비교
이제 3D 프린팅을 사용하여 분석 결과를 시각화할 수 있습니다. 시뮬레이션은 항상 훌륭한 시각화 도구였지만 이제는 그 결과를 "느끼고" 손에 쥐고 있을 수 있습니다!
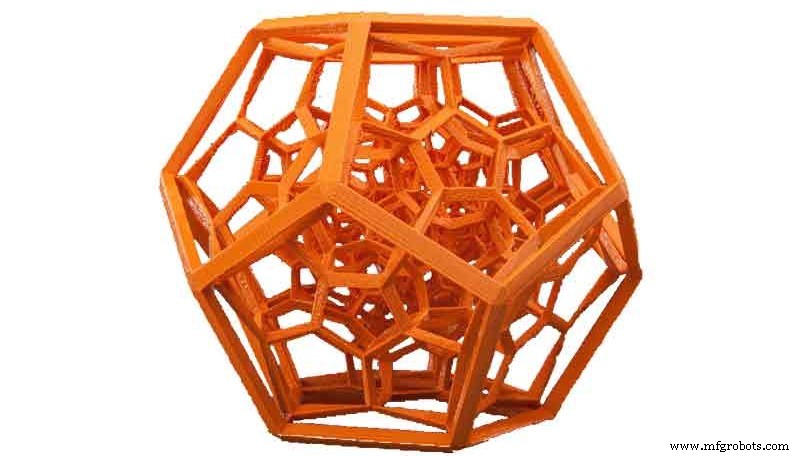
설계 최적화를 위한 시뮬레이션 및 3D 인쇄 기술 사용
가장 흥미로운 발전 두 가지 CAE 및 3D 프린팅에서 형상 최적화를 위한 도구입니다. 단일 부하 시나리오에 대해 단일 연구를 실행하는 것이 중요합니다. solidThinking Inspire와 같은 도구 내부의 시뮬레이션 기술을 사용하여 여러 사용 또는 로드 케이스에 걸쳐 자동으로 최적화할 수 있을 때 그 가치는 몇 배나 증가합니다.
solidThinking Inspire를 사용한 최적화 워크플로
토폴로지 최적화 도구는 꽤 오랫동안 사용되어 왔으며 초기에는 일반적인 제조 방법의 모양 제약으로 인해 제한적이었습니다. 그런 다음 이러한 코드는 최적화된 설계가 실현 가능한지 확인하기 위해 제조 제약 조건에 대한 조항을 포함하도록 더 똑똑해졌습니다.
이제 3D 인쇄가 제조 옵션 이 되었습니다. 그것은 우리가 이전에 "버려야 했던" 형태의 문을 열어줍니다. 전통적인 제조 방법과 마찬가지로 고려해야 할 공정 효과가 있습니다.
3D 프린팅 프로세스 시뮬레이션 워크플로
다른 빌드 경로와 프로세스 설정을 사용하여 수백 개의 부품을 물리적으로 인쇄할 수 있지만 이는 곧 엄청난 비용과 시간이 됩니다. 시뮬레이션 도구는 이제 엔지니어가 최종 부품에 대한 3D 인쇄 프로세스 효과를 예측할 수 있도록 인쇄 변수를 고려하는 데 사용됩니다.