미래의 복합재 제조 - AFP 및 적층 제조
사전 제작된 CFRP 표면 및 브래킷 (왼쪽 상단)에 "중복 인쇄" , 3D 프린팅 및 필라멘트 와인딩과 같은 하이브리드 공정 (오른쪽 상단) , AFP 라미네이트 위의 3D 프린팅 코어 및 3D 프린팅 코어의 AFP 스킨 (오른쪽 하단) 및 45도에서 CEAD AM Flexbot 3D 프린팅 (왼쪽 하단) . 사진 제공:TU 뮌헨, 탄소 복합 재료 회장
9월에는 AFP(Automated Fiber Placement)와 AM(Additive Manufacturing)에 대한 가상 심포지엄 "FUTURE COMPOSITE MANUFACTURING – AFP &AM"에 참석했습니다. 이 심포지엄은 에서 탄소 복합 재료(LCC) 의장이 주최했습니다. 뮌헨 공과 대학 (TUM, 뮌헨, 독일). 이 행사에는 TUM의 연구 파트너인 Australian National University(ANU, Canberra)도 포함되었습니다. 심포지엄에서는 TUM과 ANU의 복합재료 R&D 역량과 AFPT, Airbus, BMW, CEAD, DLR, Fraunhofer, GKN Aerospace, INOMETA, SGL Carbon 및 Victrex를 포함한 산업 파트너와의 완료 및 진행 중인 프로젝트를 검토했습니다.
ANU와의 TUM 협력은 열가소성 복합 재료로 압축 천연 가스(CNG) 저장 탱크를 개발하기 위한 AutoCRC 프로젝트와 함께 2010년에 시작되었습니다. 그 이후로 공동 R&D는 호주 연구 위원회(Australian Research Council)의 AMAC(Automated Manufacture of Advanced Composites) 센터와 ANU의 세 가지 주요 중점 분야의 형성을 포함하여 계속되었습니다.
<울>
재료 강화 - 탄소 복합재의 기능적 특성 향상을 위한 나노 스케일 소재 및 코팅
- 열 및 전기 전도성을 위한 그래핀 강화 프리프레그 테이프
레이저-AFP - Ford와 복합 강화강 개발 프로젝트
- 가열 바이어스의 디지털 제어, 예:모서리/3D 형상에 대한 공정 안정성
X선 CT를 사용한 고급 진단
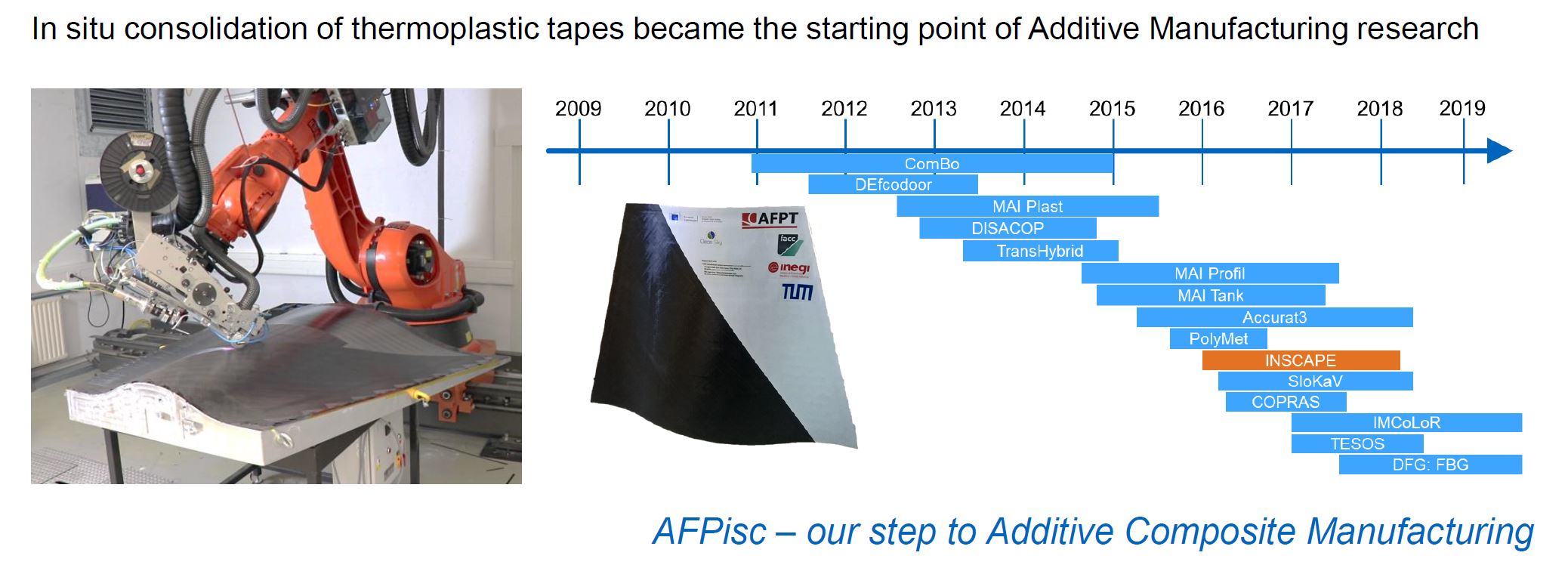
사진 제공:Dr.-Ing 교수의 "AFP와 AM 병합에 의한 새로운 지평" Klaus Drechsler, TUM 심포지엄 2020년 9월.
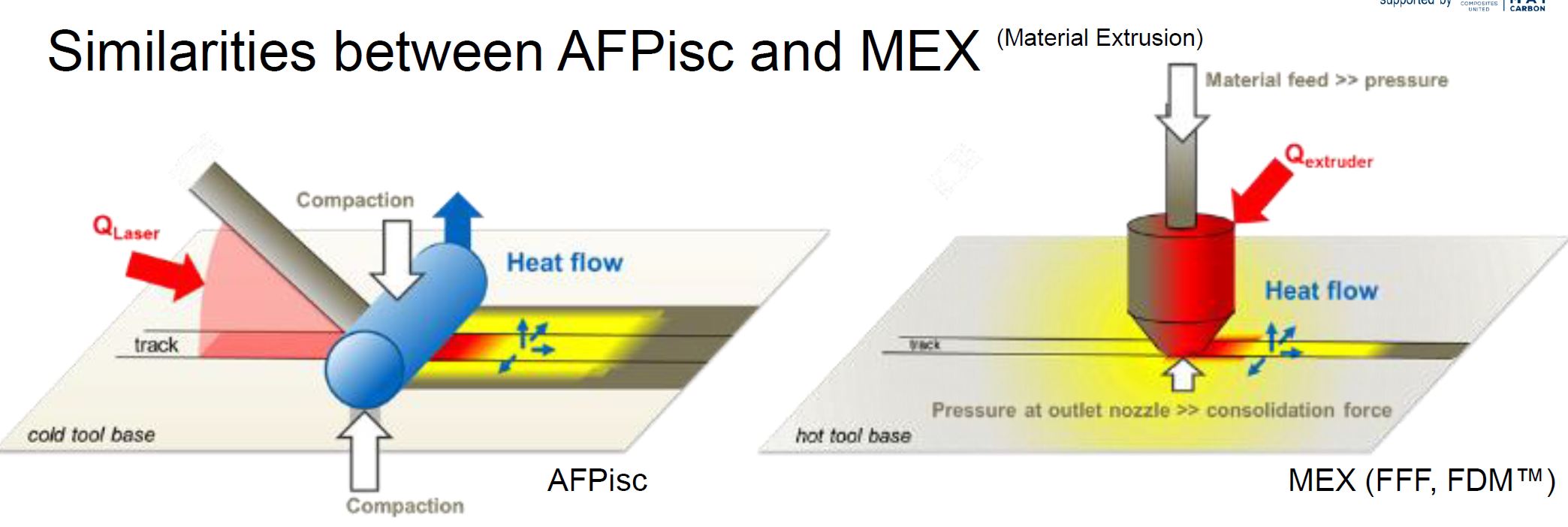
사진 제공:Klaus Drechsler, 2020년 9월 TUM 심포지엄.
그는 3D 인쇄 섬유 강화 복합 재료에 사용되는 가장 일반적인 공정인 재료 압출(MEX)과 AFP ISC 간의 유사점에 대해 논의했습니다.
<울>
국부적, 반복적 열처리
레이어 기반 설계 및 직교 이방성 재료 속성
2D 및 3D 프로그래밍 경로를 따라 재료 배치 및 레이어 간 열 활성화
그런 다음 Drechsler는 복합 재료에 대한 미래의 요구 사항과 AFP와 MEX를 결합하여 비용 효율적이고 생태학적으로 지속 가능한 고성능 경량 구조의 단기 및 장기적 구조를 포함한 솔루션을 제공할 수 있는 방법에 대해 논의했습니다.
LCC의 기능을 설명하면서 Drechsler는 MEX 장비와 적층 제조 분야의 과거 및 진행 중인 R&D 프로젝트에 대한 개요를 설명했습니다.
ISC AFP와 관련하여 LCC의 최근 및 진행 중인 개발은 다음과 같습니다.
<울>
수소 저장 탱크를 포함한 압력 용기와 같은 구조물의 산업화를 지원하는 용기 와인딩 헤드
레이저 빔 가열의 폐회로 제어
유체 냉각 롤러를 사용하여 통합
ISC 최적화를 위한 테이프 특성화
MEX 및 3D 프린팅 분야에서 LCC의 발전은 향후 2일 동안 여러 프레젠테이션에서 더 자세히 조사되었습니다.
CEAD 및 대규모 3D 프린팅
Drechsler의 기조연설 후 다음 프레젠테이션은 CEAD(Delft, 네덜란드)의 전무이사인 Maarten Logtenberg가 진행했습니다. 2014년에 설립된 CEAD는 갠트리 기반 밀폐형 셀(CFAM Prime) 및 로봇 기반 시스템(AM Flexbot)으로 연속 섬유 적층 제조(CFAM) 기술을 기반으로 하는 상용 시스템을 판매했습니다. LCC는 후자를 소유하고(위 표 참조) 여러 프로젝트에서 LCC와 협력합니다(CW 참조). CEAD 및 TUM LCC와의 작업에 대한 기사).
Logtenberg 프레젠테이션의 하이라이트에는 CNC 밀링, 대형 가열 인쇄 베드(1.2m x 3m 및 1.2m x 2m) 및 가열 회전 인쇄 베드를 통합하는 하이브리드 솔루션의 CEAD 개발이 포함되었습니다. 또한 상업용 항공기 부품의 연속 오토클레이브 생산을 위한 섬유 강화 도구의 인쇄뿐만 아니라 더 큰 셀과 45도 인쇄도 추구하고 있습니다.
Logtenberg는 3D 인쇄된 오토클레이브 도구의 주요 문제 중 하나는 열팽창이며 4미터보다 훨씬 큰 도구는 너무 많이 팽창하는 경향이 있어("하이브리드, 대형 적층 도구" 참조) 도구 설계를 통해 충분히 보상하기 어렵습니다. . 그가 제시한 해결책은 현재까지 주로 사용되는 절단된 섬유 보강재를 AM Flexbot과 같은 시스템에서 증착된 연속 섬유로 교체하는 것입니다.
이 경로는 "복합재 플랩 생산을 위한 3D 인쇄 트랙 강화 장치 소개 프레젠테이션에서 두 번째로 언급되었습니다. "는 독일 뮌헨의 GKN Aerospace에서 Thomas Herkner가 제공한 것입니다. 이 3D 인쇄 CFRP 강화 장치는 Airbus A350 및 A330용 CFRP 착륙 플랩 생산의 도구로 사용됩니다. GKN의 이 성공적인 프로그램은 절단 섬유 강화를 사용했지만 Herkner는 3D 인쇄 도구와 궁극적으로 항공기 부품 자체에 연속 섬유를 사용하는 것을 포함하는 추가 개발을 위한 로드맵을 보여주었습니다.
이 경로는 최근 CW 블로그에서 LCC 리서치 Patrick Consul에 의해 잘 설명되었습니다.
영사는 또한 TUM 심포지엄에서 대규모 압출 기반 AM을 위한 공정 설계를 살펴보며 발표했습니다. 그는 아래에 표시된 유리 및 상전이가 CFAM 및 AM Flexbot과 같은 3D 인쇄 시스템에서 용융 및 압출되는 절단 섬유 강화 펠릿의 재료 특성에서 가장 큰 변화를 나타내는 방법에 대해 논의했습니다.
Consul의 연구는 폴리머 점도, 압출 온도 및 토크와 같은 MEX 매개변수가 인쇄된 복합재의 결정도에 어떻게 영향을 미치는지 분석했으며, 이는 다시 3D 인쇄 중에 레이어를 함께 용접하는 능력에 영향을 미칩니다. 이러한 레이어 간 결합 외에도 Consul은 인쇄된 레이어의 섬유 정렬 및 잔류 응력도 조사했습니다. 제시된 솔루션 중 하나는 오늘날 열가소성 복합 재료의 ISC AFP에서 널리 사용되는 인쇄 중 기판을 예열하기 위해 레이저를 사용하여 AFP에서 AM으로 지식을 이전하는 것이었습니다. 초기 실험에서는 제어 가능한 레이저 다이오드의 링을 사용했습니다.
Consul의 동료인 Matthias Feuchtgruber는 공정 설계 및 재료 특성화에서 복합 재료 AM을 위한 가상 공정 체인 개발로 나아가는 과정을 나중에 발표했습니다.
그런 다음 Alexander Matschinski는 복합 AM의 끝없는 섬유 통합에 대해 발표했으며 아래 차트를 제시했으며 이는 CW에서 사용한 수정된 차트의 기초가 되었습니다. 의 연속 섬유 3D 프린팅에 대한 차세대 보충 기사. Matschinski는 또한 연속 섬유 AM 구조의 설계 작업과 사전 제작된 CFRP 부품 및 표면에 "중복 인쇄"의 미래 개발에 대해 논의했습니다.
SGL Carbon의 Christopher Ebel 박사는 자동차용 강철 하부 구조를 강화하고 부품 수를 37개에서 9개로 줄이고 중량을 41% 줄이는 것을 포함하여 연속 섬유의 다른 흥미로운 적용을 보여주었습니다. 또 다른 개념은 하중 최적화 구조를 위해 스냅 경화 에폭시 수지가 함침된 토우프레그를 사용하는 3D 와인딩이었습니다. 이 디지털 기반 접근 방식은 복잡한 로드 및 토폴로지 최적화의 단순화로 시작하여 자동화된 제조가 이어집니다. 결과 부품은 인서트를 구조에 고정하는 형태를 활용하여 강성 손실 없이 하중을 도입할 수 있습니다. 최신 3D 금속 인쇄 공정을 이러한 인서트에 사용할 수 있어 부하 처리 효율성과 비용 절감을 더욱 최적화할 수 있습니다.
DLR의 Sebastian Nowotny는 AFP 라미네이트에 3D 인쇄하고 부분적으로 열린 3D 인쇄 구조에 AFP를 인쇄하는 것을 포함하여 열가소성 복합 재료의 ISC AFP와 3D 인쇄를 결합하는 것에 대해 논의했습니다. 첫 번째 실험에는 미리 만들어진 CFRP 스킨에 코어를 3D 인쇄한 다음 3D 인쇄 코어 위에 AFP/테이프를 놓는 것이 포함됩니다. 시편을 만든 다음 인장 전단 테스트를 거쳐 스킨-코어 결합을 평가했습니다.
슬라이드쇼 제목
사진 제공:Sebastian Nowotny, DLR, TUM 심포지엄 2020년 9월
하이브리드 3D 프린팅과 AFP를 사용하여 만든 쿠폰의 인장 전단 테스트. 사진 제공:Sebastian Nowotny, DLR, TUM 심포지엄 2020년 9월
사진 제공:CEAD, TUM 심포지엄 2020년 9월
복합 재료 생산 중 컴퓨터 단층 촬영의 향후 적용. 사진 제공:Australian National University, 2020년 9월 TUM 심포지엄
하이브리드 CFRP 금속 구조를 만들기 위해 레이저 AFP를 사용한 개발 작업. 사진 제공:Australian National University, 2020년 9월 TUM 심포지엄
열 및 전기 전도성을 위한 그래핀 강화 프리프레그 테이프. 사진 제공:Australian National University, 2020년 9월 TUM 심포지엄
이전 다음
Airbus Central Research &Technology의 재료 책임자인 Christian Weimer는 미래 항공기의 위치를 확보하기 위해 복합 재료가 달성해야 하는 비용 절감과 지속 가능성 증가를 목표로 하는 진화하는 기술 환경의 일환으로 연속 섬유 인쇄에 대해 논의했습니다. 그는 진정으로 효율적인 3D 합성물이 다음을 사용해야 한다고 강조했습니다.
<울>
적절한 원료 및 중간체 – 섬유, 반제품
효율적인 프로세스 및 인터페이스 - AM 열가소성 수지, 사출 성형
적응된 디자인 및 크기 조정 - 통합, 완전히 3D 부하 최적화됨)
표면 및 기능 – ESN(전자 일련 번호), SHM(구조 상태 모니터링)
그는 또한 긴급한 기후 및 환경적 지속 가능성 목표를 달성하기 위해 바이오 유래 섬유 및 수지의 필요성에 대해서도 논의했습니다.
TUM 심포지엄은 ANU에서의 작업 요약을 포함하여 더 많은 프리젠테이션을 선보였으며 모두 복합 재료가 어떻게 앞으로 나아가고 있고 LCC가 전 세계 파트너와 협력하여 복합 재료가 달성하고 우리 산업을 발전시킬 수 있는지 계속 구상하는 방법을 보여주는 데 매우 흥미로웠습니다.