RTM 플래퍼론, 외골격 등을 위한 3D 프린팅 CFRP 몰드
사진 제공:TU 뮌헨 탄소 복합 재료(LCC) 및 QPoint 합성 의장
탄소 복합 재료의 의장(Lehrstuhl für Carbon Composites 또는 LCC)은 SGL Carbon(독일 비스바덴)의 자금 지원으로 뮌헨 공과 대학(TUM, 뮌헨, 독일)의 기계 공학과에서 2009년에 설립되었습니다. 그 임무는 시뮬레이션 및 테스트 프로젝트를 포함하여 탄소 섬유 강화 폴리머(CFRP) 재료, 공정 및 응용 분야에서 R&D를 수행하는 것입니다. 독일 대학 시스템에서 "의자"는 교수와 그의 팀으로 구성된 가장 작은 단위입니다. LCC 팀은 Dr. -Ing. Klaus Drechsler는 현재 30명의 전임 연구원을 고용하고 있습니다. SGL 자금 지원은 2016년에 종료되었지만 LCC는 복합 재료 R&D에서 리더십을 계속해 왔습니다. 여기에는 MFFD(다기능 동체 시연기)의 하단에 대한 금형 제작이 포함되며 아래 사이드바 참조, 이제 3D 인쇄/첨가제도 포함됩니다. 제조.
이 블로그는 CEAD(네덜란드 델프트)에서 LCC가 로봇 팔을 사용하는 3D 프린팅을 위해 압출기 기반 AM 플렉스봇 시스템 중 하나를 구입했다고 나에게 알렸을 때 시작되었습니다. 그러나 LCC 연구원인 Patrick Consul과의 후속 인터뷰에서는 Clean Sky 2 내에서 열경화성 복합재 항공기 플래퍼론 생산을 위한 열가소성 복합 RTM 몰드를 3D 인쇄하는 COMBO3D와 도구를 생산하는 EMOTION을 포함한 프로젝트의 보고를 밝혔습니다. Clean Sky 2의 열가소성 합성물 MFFD(Multifunctional Fuselage Demonstrator)의 하반부를 성형할 뿐만 아니라 동일한 동체가 직접 현장 통합(오토클레이브 외부)을 통해 생산될 수 있는 방법을 보여주기 위한 2차 부분 도구입니다. TUM이 어떻게 이 지경에 이르렀고 어디로 향하고 있는지에 대한 전체 토론이 흥미로웠습니다.
MMFD 하반부 금형
2020년 2월 블로그:"다기능 동체 데모용 LM PAEK 용접 증명"을 참조하십시오. 이 사이드바는 GKN Fokker(네덜란드 Hoogeveen)의 MFFD 프로그램 관리자인 Bas Veldman이 작성한 2020년 2월 논문 "다기능 동체 시연자 개발"에서 발췌한 것입니다.
MFFD 하반부의 쉘은 용접 스트링거, 클립 및 프레임으로 강화된 열가소성 스킨으로 구성됩니다. 시연할 제조 공정은 세 가지 주요 단계로 구성됩니다.
<올>
NLR의 기존 레이저 AFP 기계로 평평한 기울어진 테이블에 실연자의 큰 피부용 프리프레그 테이프를 올려 놓습니다.
레이업은 흡입 컵과 함께 로봇 방식으로 암형 통합 몰드로 옮겨지고 가열 없이 그 안에 드레이프됩니다.
진공 포장 후 피부는 오토클레이브에서 통합됩니다.
암형 통합 몰드를 사용하면 수컷 공구보다 훨씬 단순한(평평한) 표면을 제공하는 동시에 피부의 외부 표면 품질에 대한 공기역학적 제약을 직접 제어할 수 있습니다.
MFFD 프로젝트는 또한 오토클레이브 외부 를 요구합니다. 대형 다기능 동체 시연기와 병렬로 시작하여 후속 소형 시연기에서 조사할 프로세스. 특히, 현장 열가소성 합성물 레이업 동안 통합이 달성되는 제조는 오토클레이브 단계를 완전히 제거하여 제조를 단일 단계 절차로 줄일 수 있기 때문에 고려됩니다.
Autoclave Consolidation 또는 EMOTION(https://cordis.europa.eu/project/id/864474) 안팎의 열가소성 동체용 강화 금형은 MFFD 하부 쉘 툴링을 생산하기 위한 Clean Sky 2 프로젝트입니다. 프로젝트 코디네이터인 TU 뮌헨의 Patrick Consul은 "간단하게 들리지만 실제로는 400°C까지 가열해야 하기 때문에 상당히 어렵습니다. 이는 Invar36이 CTE(열팽창 계수)가 크지 않은 온도 범위보다 훨씬 높습니다.” Invar는 고온 경화 주기 동안 팽창이 적기 때문에 복합 성형 도구에 일반적으로 사용됩니다. 그러나 Invar의 CTE는 온도에 따라 증가합니다. 영사는 "문제는 가열 및 냉각 중 열팽창을 제어하는 것입니다. 경화 중 8m x 4m 몰드 및 동체 스킨의 열팽창을 제어하는 것입니다."라고 말합니다. 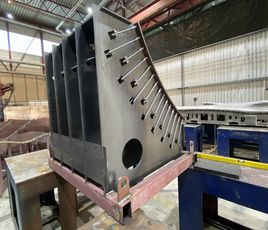
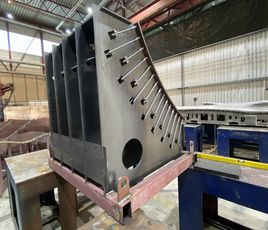
사진 제공:탄소 복합 재료 의장
적층 제조의 발전
영사는 "저희는 LCC 내에서 적층 가공을 하는 8-9명의 직원입니다."라고 말합니다. 그는 2012년 LCC가 AFPT(독일 Dörth)에서 레이저 보조 열가소성 복합 테이프 배치 기계를 구입하면서 이 작업의 역사를 시작했습니다. 나중에 자동 섬유 배치(AFP)를 가능하게 하기 위해 Coriolis Composites(프랑스 Quéven) 기계를 추가했습니다. ) 열경화성 프리프레그. 최초의 필라멘트 기반 데스크탑 프린터는 2017년에 구입했습니다. "저도 2017년에 합류하여 Clean Sky 2와 같은 제안서 작성을 포함하여 새로운 응용 프로그램 및 연구 프로젝트 개발을 지원했습니다." 그는 Clean Sky 2 프로젝트가 공개적으로 발표된 제안 요청(CFP)에 대한 응답으로 주제 관리자에게 제출된 제안을 기반으로 수여된다고 설명합니다. LCC는 CFP08 COMBO3D 프로젝트와 CFP09 EMOTION 프로젝트에 대한 제안에 성공했습니다. 둘 다 아래에서 논의됩니다.
Consul은 "우리는 몇 가지 다른 프로젝트를 진행하고 있으며 일부는 연속 섬유 강화재를 사용한 3D 프린팅을 검토하고 있습니다. “다른 사람들은 복합 기판을 예열하여 이미 통합된 CFRP 부품에 인쇄하거나 인쇄된 층 사이의 층간 전단 강도(ILSS)를 증가시키기 위해 레이저 통합 프린트 헤드를 사용합니다. 다른 프로젝트는 예를 들어 특수 복합 부품 수가 적은 툴링 응용 프로그램을 탐색합니다."
"이러한 프로젝트는 프린팅 프로세스 중 및 이후에 적층 제조 부품의 동작을 예측하기 위해 수치 시뮬레이션을 통해 지속적으로 지원됩니다."라고 그는 말합니다. “LCC는 또한 3D 인쇄된 CFRP를 사용하여 외골격을 제조하는 것을 목표로 하는 런던 임페리얼 칼리지(Imperial College of London)와 함께 프로젝트에 참여하고 있습니다. 또 다른 프로젝트는 강성, 강도 또는 에너지 흡수와 관련하여 3D 인쇄 부품의 특성을 최적화하기 위해 격자 구조를 연구합니다."
프린터의 진행 상황
Consul은 "Apium(독일 칼스루에)의 FDM(융합 증착 모델링) 기반의 간단한 3D 프린터를 사용하여 높은 강성이 필요한 특수 테스트 고정구를 인쇄하는 것으로 시작했습니다."라고 설명합니다. “프린터는 인쇄 시간을 줄이기 위해 높은 재료 출력으로 길이 3미터, 너비 1미터였습니다. 연속 섬유를 사용할 수는 없었지만 PEEK, PEKK 및 쵸핑된 탄소 섬유 강화 PEEK로 인쇄하기에 잘 설계되었습니다. 가열 베드뿐만 아니라 프린트 헤드 주변의 가열 플레이트를 사용하여 인쇄물에서 균일한 온도 분포를 생성하여 열 스트레스를 줄이고 결정화를 보장하는 데 도움이 되었습니다.”
"우리는 또한 Markforged(미국 매사추세츠주 케임브리지) 프린터를 잠시 사용하다가 Anisoprint[룩셈부르크 Esch-sur-Alzette]를 얻었습니다."라고 영사는 말합니다. Markforged 프린터는 연속 섬유로 FDM을 가능하게 했지만 LCC 팀은 이를 유지하지 않기로 결정했습니다. 영사는 "우리가 가진 문제는 시스템이 매우 폐쇄적이라는 것이었습니다."라고 설명합니다. “Markforged의 슬라이서 소프트웨어는 우리가 할 수 있는 일을 심각하게 제한했기 때문에 연구에 사용하기가 너무 어려웠습니다. 우리는 연속 섬유 재료 층을 인쇄한 다음 그 위에 짧은 섬유 강화 열가소성 필라멘트 층을 인쇄할 수 있었습니다. 코드를 생성하는 슬라이서는 우리의 G 코드를 허용하지 않습니다. 따라서 각 레이어 등에 연속 섬유를 사용하여 원하는 방식으로 인쇄하도록 기계에 지시할 방법이 없었습니다.”
이에 대해 질문을 받았을 때 Markforged는 자사 시스템이 연구용으로 사용되도록 의도된 것이 아니라 대신 규칙 기반 광섬유 경로를 활용하고 슬라이서를 구성하는 데 적은 노력과 시간이 필요한 부품 제작에 널리 사용되도록 간단하고 견고하게 설계되었다고 설명합니다. . Eiger 소프트웨어는 사용자가 개별적으로 레이어를 구성할 수 있도록 하며 Markforged는 피드백을 환영하며 고객을 위한 사용자 경험 개선을 우선시합니다.
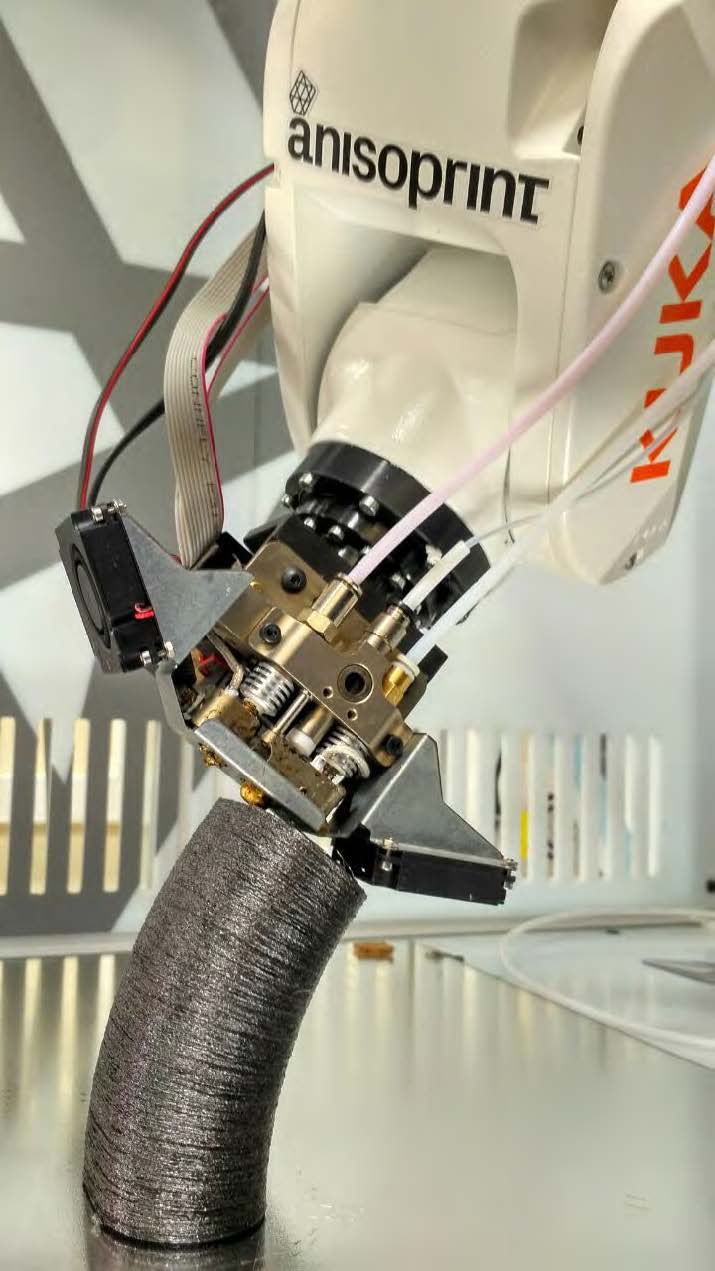
사진 제공:Ansoprint
Consul은 "완전히 개방된 G 코드 슬라이서를 사용하는 Anisoprint를 통해 프로세스에 더 많이 액세스할 수 있었습니다."라고 말합니다. “또한 연속 탄소 섬유를 2D 레이어뿐만 아니라 3D 곡선에서도 평면 밖으로 인쇄할 수 있습니다. 우리는 1m x 1m 부품을 생산할 수 있는 소형 Kuka 로봇용 Anisoprint 프린트 헤드를 보유하고 있습니다. 이는 대부분의 데스크탑보다 크지만 로봇 시스템에서는 작습니다."
그러나 Anisoprint의 이중 매트릭스 는 어떻습니까? 열경화성-열가소성(TS-TP) 재료? Anisoprint의 2019년 블로그에서 설명했듯이 "... 먼저 연속 섬유 강화에 열경화성을 함침시킵니다. 폴리머는 인쇄하는 동안 용융된 열가소성 필라멘트로 압출됩니다." 영사는 TS필라멘트와 TP사이의 접착력이 꽤 좋다고 답합니다. “첫 번째 시도에서 Markforged 프린터에 비해 더 많은 양의 광섬유를 얻을 수 있었지만 이는 G 코드를 수정할 수 있었기 때문입니다. Anisoprint 프린트 헤드는 TS 필라멘트를 TP로 밀어 넣은 다음 배치합니다. 우리는 그 프린터를 외골격 부품에 사용할 계획입니다. 고강도 섬유를 통합하는 쉬운 방법입니다."
압출 펠릿 프린터
다음 진행은 처음에는 단섬유 강화 TP를 사용한 다음 연속 섬유 TP를 사용하는 대규모 프린터로 진행되었습니다. “저희는 먼저 로봇에 장착된 압출기를 개발했고, 그 후 CEAD 기계에 대한 관심이 빠르게 따랐습니다. 우리는 내년에 이 두 시스템에 연속 광섬유를 통합하기를 희망합니다.”
그러나 이미 로봇 팔에 압출기가 있는 경우 CEAD 기계가 필요한 이유는 무엇입니까? Consul은 "초기 압출기는 Dyze Pulsar 펠릿 압출기의 베타 버전으로, 최대 약 2kg/hr 및 PAEK의 경우 약 1kg/hr을 출력하지만 20% 이상의 탄소 섬유 로딩으로 어려움을 겪습니다."라고 말합니다. “그러나 로봇은 인쇄 중에 자주 가속 및 감속하기 때문에 평균 출력이 더 낮습니다. COMBO3D의 경우 초기의 소규모 절반 금형에는 이미 최소 36kg이 필요했기 때문에 단일 절반을 인쇄하는 데 약 48시간이 필요했습니다. 또한 재료 공급 라인이 막히거나 부품이 휘는 것과 같은 오류가 언제든지 발생할 수 있기 때문에 항상 누군가와 함께 있어야 했습니다."
COMBO3D 최종 데모는 초기 소규모 부품보다 약 10배 크기 때문에 이 첫 번째 압출기 시스템을 사용하여 인쇄하는 것은 불가능하다고 Consul은 말합니다. “또한 빅트렉스가 우리에게 공급한 일부 재료는 점도가 더 높았고 이 첫 번째 압출기는 이러한 폴리머를 압출하기에 충분한 토크를 제공할 수 없었습니다. CEAD 프린터의 경우 최대 출력이 약 12.5kg/hr이었고 몇 시간의 시도 끝에 약 5-6kg/hr의 안정적인 평균 출력을 얻었습니다. 이를 통해 8시간 이내에 작은 크기의 반쪽 금형을 인쇄할 수 있었고 더 많은 섬유 함량을 사용하여 뒤틀림을 줄일 수 있어 전체 공정을 더 쉽게 제어할 수 있었습니다."
"따라서 Pulsar는 이미 펠릿을 사용하고, 높은 재료 출력을 달성하고, 로봇의 자유도를 활용할 수 있게 해주었지만, CEAD 프린터는 더 큰 부품, 더 높은 섬유 함량 및 더 넓은 범위의 폴리머로 우리의 능력을 확장합니다. . Pulsar는 우리의 필라멘트 기반 프린터와 CEAD 사이의 격차를 출력뿐만 아니라 노즐 크기 및 결과적인 출력 세부 사항에서도 연결합니다.”
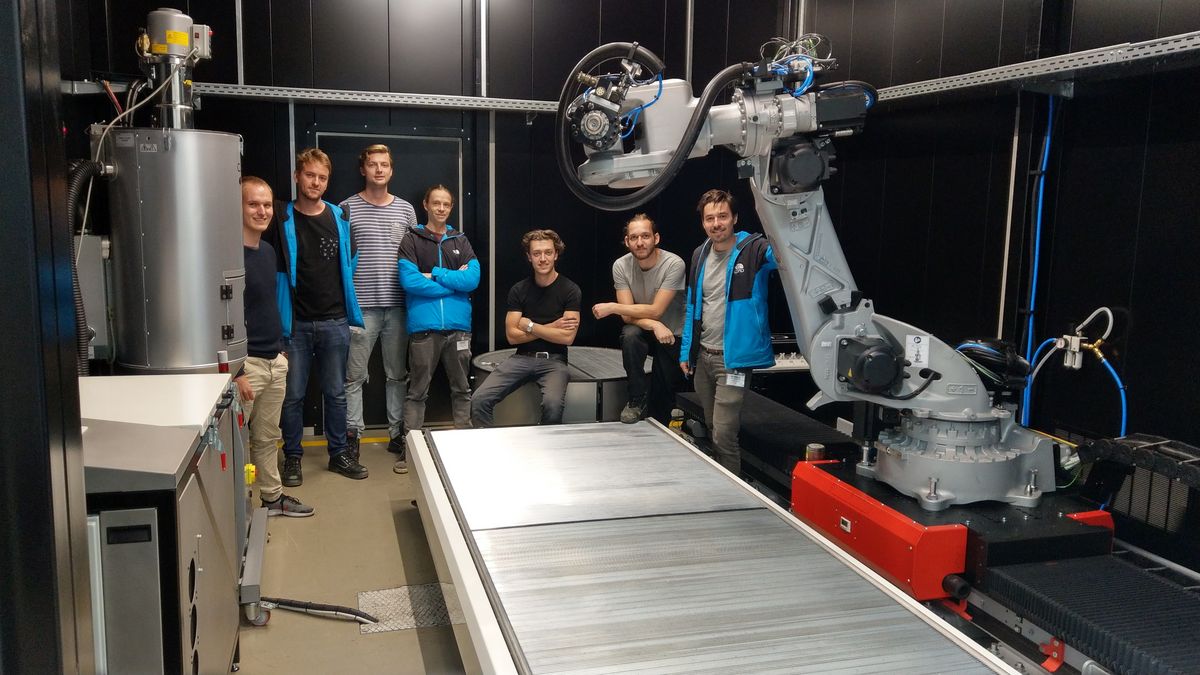
사진 제공:탄소 복합 재료 의장
CEAD AM Flexbot 기술 데이터:
<울>
AM Flexbot 기술 데이터:
펠렛 기반 압출 인쇄 시 최대 12.5kg(비보강 및 단섬유 강화)
최대 450°C의 재료 처리
빌드 볼륨 3000 x 1200 x 1700밀리미터
회전 테이블 또는 플랫 테이블(가열식)에 제작판
밀링 헤드를 사용한 재작업
콤보3D
이 Clean Sky 2 프로젝트의 목적은 작업 패키지 A-3.1:고속 및 저속을 위한 종합 날개의 일부인 대형 여객기용 시연용 복합 플래퍼론(1.5 x 3m)을 생산하기 위해 금형을 3D 인쇄하는 것입니다. 적층 제조를 사용하는 목표는 공구 생산 리드 타임을 단축하는 것입니다. 이 프로젝트는 2019년 1월에 시작하여 2021년 3월에 종료됩니다. 파트너에는 Alpex Technologies(오스트리아 Mils bei Hall), 경량 금속 전문업체 Leichtmetallkompetenzzentrum Ranshofen(오스트리아 란스호펜) 및 Victrex(영국 Thornton Cleveleys), 고성능 열가소성 수지 공급업체가 포함됩니다. 폴리아릴에테르케톤(PAEK).
프로젝트의 또 다른 핵심 부분은 이 탄소 섬유/에폭시 플래퍼론이 오토클레이브 경화 프리프레그 대신 RTM(수지 전이 성형)으로 만들어질 수 있다는 것을 입증하는 것입니다. RTM 부품은 오토클레이브 부품과 동일한 180°C에서 경화됩니다. 열 안정성을 보장하기 위해 공구는 용융 온도가 305°C인 짧은 탄소 섬유 강화 PAEK로 인쇄됩니다.
경화 주기를 단축하기 위해 3D 프린팅된 금형은 능동 온도 제어를 통합합니다. "우리는 오토클레이브에 비해 금형을 더 빨리 가열하고 냉각할 수 있어야 합니다."라고 Consul은 말합니다. “우리는 금형 표면 아래 3밀리미터의 전기 가열 요소 메쉬를 사용하고 금형 표면 아래 6밀리미터에 가열된 오일 또는 공기를 위한 인쇄 채널을 통합할 것입니다. 이러한 방식으로 금형 표면을 매우 빠르게 가열할 수 있지만 채널을 사용하여 도구 볼륨 전체를 가열할 수도 있습니다. 우리는 오토클레이브보다 50% 더 빠른 가열 및 냉각 속도를 목표로 하고 있으며 최소 30% 더 빠른 속도를 달성할 수 있다고 확신합니다.”
3D 프린트에 통합할 발열체는 무엇입니까? "우리는 헬리콥터 로터 블레이드용 CFRP 몰드에서 다양한 히터 영역을 구현하기 위해 히터 요소로 유리 섬유 직물에 탄소 로빙의 맞춤형 섬유 배치(TFP)를 사용했습니다."라고 Consul은 설명합니다. “이것은 우리가 QPoint Composite(독일 드레스덴)과 함께 작업을 완료한 Clean Sky 1 프로젝트를 위한 것이었습니다. 우리는 COMBO3D 금형에 대해 유사한 개념으로 작업할 것입니다.”
인쇄된 도구의 전체 개발은 시뮬레이션을 통해 지원됩니다. 도구 설계는 열 시뮬레이션에서 가열 및 냉각 시스템을 구현하여 최적화됩니다. 제조 공정도 시뮬레이션되어 인쇄 중 온도 분포에 대한 지식을 생성하고 이를 경로 계획과 연관시켜 인쇄 공정을 지원합니다.
CEAD 기계 설치 및 프로젝트 진행
"CEAD 시스템은 주문에서 설치까지 단 6개월 만에 매우 빠르게 배송되었습니다."라고 Consul은 말합니다. “이때까지 우리는 재료 테스트를 완료하고 플레이트 툴링을 설계했으며 작은 부품 인쇄를 시작했습니다. CEAD AM Flexbot으로 프로세스를 제대로 실행하는 데 시간이 오래 걸릴까 걱정했지만 첫 번째 시도에서는 잘 작동했습니다.”
플레이트 툴링? "쿠폰 테스트를 위한 CFRP 플레이트를 생산하기 위해 이미 냉각 채널과 히터 요소를 통합한 작은 금형입니다."라고 그는 설명합니다. "이 테스트는 3D 인쇄된 CFRP RTM 몰드의 품질이 Saab이 오토클레이브 공정으로 생산하는 현재 CFRP와 비교할 수 있는지 확인하기 위한 것이었습니다."
불행히도 프로젝트는 COVID-19로 중단되었지만 "이제 모든 것이 순조롭게 진행되고 있으며 우리는 따라잡고 있습니다"라고 영사는 말합니다. 그리고 3D 프린팅된 금형에 PAEK를 사용하는 것은 어떻습니까? "현재 유일한 문제는 PAEK의 Tg[유리 전이 온도]가 130-140°C라는 점입니다. 이는 데모 부품의 180°C 경화보다 낮습니다."라고 Consul은 말합니다. "그래서 우리는 크리프가 발생하거나 표면이 손상되기 전에 경화 온도에서 얼마나 많은 사이클을 완료할 수 있는지 확인해야 합니다."
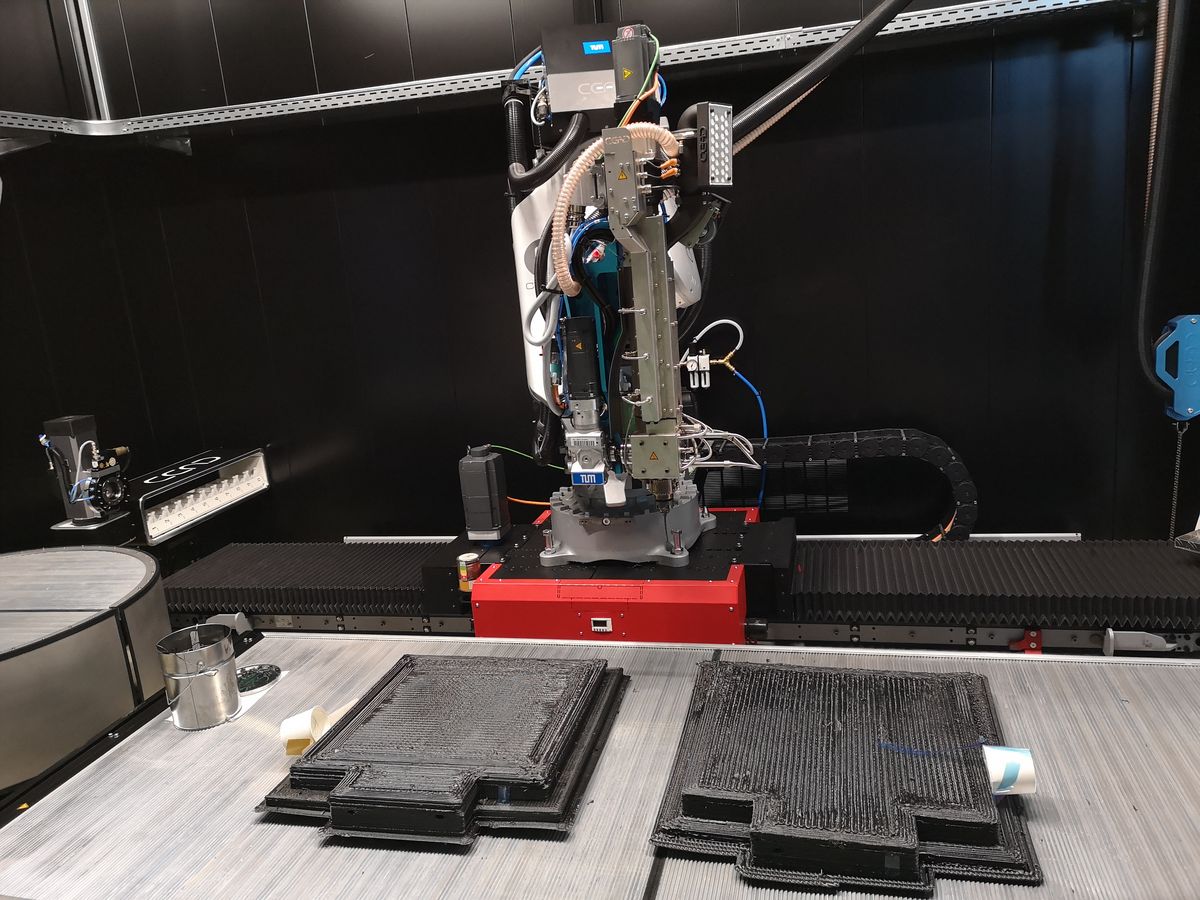
사진 제공:탄소 복합 재료 의장
다른 프로젝트에서 CEAD 기계?
"우리는 CEAD 기계와 폴리에테르설폰(PESU)을 사용하는 GKN Aerospace Deutschland(Munich)와 함께 내년에 시작되는 항공우주 툴링 프로젝트에 지원하고 있습니다."라고 Consul이 말했습니다. [참고:독일의 GKN은 A330 및 A350용 합성 날개 플랩과 Bombardier Global 비즈니스 제트기 제품군용 에일러론을 생산합니다.] “CEAD는 연속 탄소 섬유용 기계 개발을 책임지는 이 부분의 일부가 될 것입니다. 우리는 또한 CEAD 기계를 내부적으로 사용하여 RTM용 프로토타입 금형을 만들 계획입니다. 그렇지 않으면 외주를 받았을 것입니다. 작업을 가속화하는 데 도움이 됩니다.”
영사는 PESU가 PAEK보다 Tg가 더 높다고 말합니다. "또한 반결정이 아닌 비결정질이므로 크리프 저항이 문제가 될 수 있지만 인쇄하기가 더 쉬워야 합니다. 우리가 하려는 것은 PEI(폴리에테르이미드)를 피하는 것입니다. 과거에 우리는 에폭시 수지에 대한 PEI 결합 문제를 살펴보았습니다. RTM6[RTM용 에폭시]은 PEI를 용해하여 둘 사이의 우수한 접착력을 유도합니다. 이것은 부품에 달라붙는 것이 아니라 풀어야 하는 3D 인쇄 금형에서 원하지 않는 것입니다.”
미래의 산업(및 비행) 3D 인쇄 합성물
LCC가 적층 제조 분야에서 추진하고 있는 다른 프로젝트에 대해 논의하면서 저는 Consul에게 외골격에서 CFRP를 억제한 이유가 무엇인지 묻습니다. “외골격은 착용자마다 맞춰야 하기 때문에 부품이 특화되어 있어 부피가 크지 않습니다.”라고 그는 대답합니다. “우리 프로젝트는 환자별 하지 외골격 구성요소의 생산을 가능하게 하여 24시간 이내에 환자별 외골격의 생산을 가능하게 하는 것을 목표로 합니다. 이 외골격은 생물학적 특성과 독특한 의료 재활 요구를 기반으로 뇌졸중 환자의 재활을 지원할 것입니다.” (CW 기사 "C-FREX 외골격은 CFRP에 의존…" 참조)
“사람들은 3D 프린팅이 모든 부품을 프린팅할 수 있다는 개념을 가지고 있지만 먼저 3D 프린팅과 복합 재료에 대한 경험이 있어야 합니다. 예를 들어, 이해해야 하는 층간 접착 및 이방성과 관련된 문제가 있는 경우가 많습니다. 3D 인쇄된 복합 부품은 현재 플라스틱 및 금속으로 만들어진 것과 동일한 디자인이 아닙니다."
그는 고성능 항공기 부품 생산을 위해 3D 인쇄된 복합 재료를 사용하는 경우 여전히 극복해야 할 문제가 있다고 지적합니다. 예를 들면 다음과 같습니다. 적층 제조를 위해 이러한 부품을 어떻게 설계합니까? 적층 제조가 가치를 더하는 부품을 어떻게 식별합니까? Consul은 “항공우주 툴링은 우리 팀이 현재 검토하고 있는 주요 응용 분야입니다. “3D 프린팅 금형이 잘 맞습니다. 이러한 금형은 부품과 동일한 경화 조건을 모두 견뎌야 하지만 금형과 관련된 위험이 플라잉 부품과 관련이 적습니다. 좋은 예는 날개용 리브 보강재로, 여러 부품이 있지만 부품당 사이클이 많지 않습니다. 따라서 이것은 기술에 대한 경험을 생성하는 좋은 방법입니다. 날아갈 구조 부품을 시도하기에는 너무 이르다. 우리는 이것을 장기적으로 목표로 하겠지만, 프린팅 도구를 사용하면 고성능 속성으로 충분히 안정적인 3D 프린팅 프로세스를 얻을 수 있고 시뮬레이션에서 이러한 부품과 프로세스를 정확하게 예측하는 능력도 개발할 수 있습니다.”